Проверка зуба колеса на изгиб 
3.7.1 YF2 = 3,6
3.7.2 Yε – коэффициент перекрытия зуба;
Yε = 1 
3.7.3 Yβ – коэффициент наклона зубьев;
Yβ=1- 
3.7.4 kFα – коэффициент распределения нагрузки между зубьями;
kFα = 1,35 
3.7.5 kFβ – коэффициент неравномерности напряжения по ширине зубчатого венца
kFβ = 1,18 
3.7.6kFV – коэффициент динамической нагрузки зубчатого колеса
kFV = 1,1 
МПа
МПа < МПа
3.8 Проверка зубьев на пластическую деформацию перегрузки при изгибе

МПа
МПа
3.9 Производим геометрический расчёт колёс, согласно расчёту и выполняем эскиз одного колеса с размерами для обоих колёс.
3.9.1 Делительный диаметр
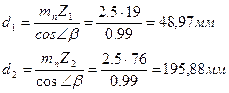
3.9.2 Диаметр выступов

3.9.3 Диаметр впадин

3.9.4 Ширина колёс
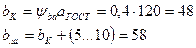
3.9.5 Толщина обода колеса , но не менее 8…15см

3.9.6 Диаметр ступицы колеса

3.9.7 Размеры фасок

3.9.8 Длина ступицы

3.9.9 Диаметр отверстия в диске

3.9.10 Толщина диска
с=0,2…0,3 от ширины колёс
с=0,2∙bк=16,0
3.9.11 Диаметр расположения отверстия в диске

3.9.12 Диаметр обода колеса

Пар-ры
| mn
| Z
| d12
| dа12
| df12
| bк,ш
| dСТ
| lСТ
| dотв
| Dотв
| с
| δо
| Dо
| Шестер
| 2,5
|
| 48,97
| 53,97
| 42,88
|
|
|
|
|
|
|
|
| колесо
| 2,5
|
| 195,88
| 200,88
| 189,63
|
|
|
| 48,09
| 118,6
| 16.0
|
| 169,63
|
4.ЭСКИЗНАЯ КОМПОНОВКА ПЕРВЫЙ ЭТАП.
4.1 Проводим расчет валов по чистому кручению по пониженным напряжениям, исходя из условий прочности на кручение:
[τкр.] = 15…25 МПа
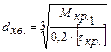
Определяем диаметр хвостовика
мм
Принимаем диаметр хвостовика по ГОСТ 6639–69 dхв=20мм :
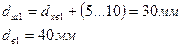
Для второго вала:

Принимаем диаметр хвостовика по ГОСТ 6639–69 мм мм
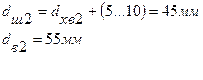
При Vзац<2.5 подшипники смазываются консистентной смазкой (литол), закладывая в карманы подшипников качения, устанавливаем маслоотражающие шайбы с внутренней стороны редуктора на 10 мм.
Выбираем подшипники для 1го вала №306 (ГОСТ8338-75)
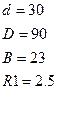
Выбираем подшипники для 2го вала №309
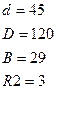
5. РАСЧЕТ ВАЛОВ.
Определяем силы действующие на валы.
Исходные данные к расчетам
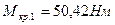
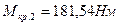

Диаметра колес
мм
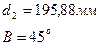
Материал валов Ст. 45 (ГОСТ 1050–72) у которой 

Отношение допускаемых напряжений

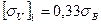
Схема нагружения валов редуктора
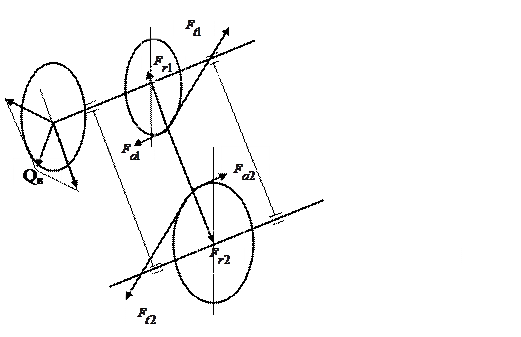
5.1 Определяем силы, действующие в зацеплении
5.1.1 Окружные
Н
Н
Принимаем Ft = 1780,4 Н
5.1.2 Радиальные
Н


5.1.3 Осевые
Н
5.2 Составляем схемы нагружения валов, определяем опорные реакции, строим эпюры нагружения валов. Расчет валов ведем в двух плоскостях.
а) Вертикальная плоскость:
1) Определяем реакции в опорах А и В
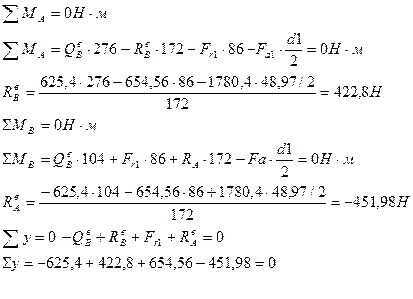
2) Строим эпюры нагружения вала от сил, действующих в вертикальной плоскости.
Сечение I - I (справа):
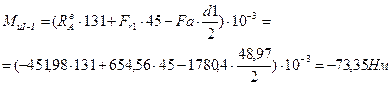
Сечение I I - I I (слева):

Сечение III - III (слева):

б) Горизонтальная плоскость
1) Определяем реакции опор, для чего составляем уравнение моментов.
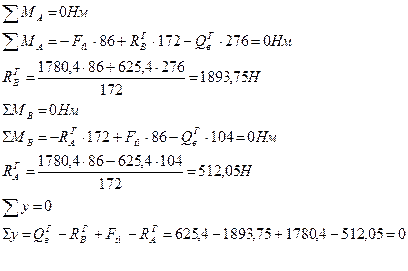
2) Строим эпюры нагружения вала от сил, действующих в горизонтальной плоскости.
Сечение I – I (Справа)

Сечение I I – I I (Слева)

Сечение Ш – Ш (Слева)

3)Определяем суммарные изгибающие моменты в сечениях I – I, I I–I I,III–III и строим эпюру нагружения суммарного изгибающего момента.
а) Сечение I – I: 
б) Сечение I I – I I: 
в) Сечение III – III: 
г) Момент крутяший Мкр=45,12Нм
д) Определяем приведённый (эквивалентный) момент в наиболее нагруженном сечении:

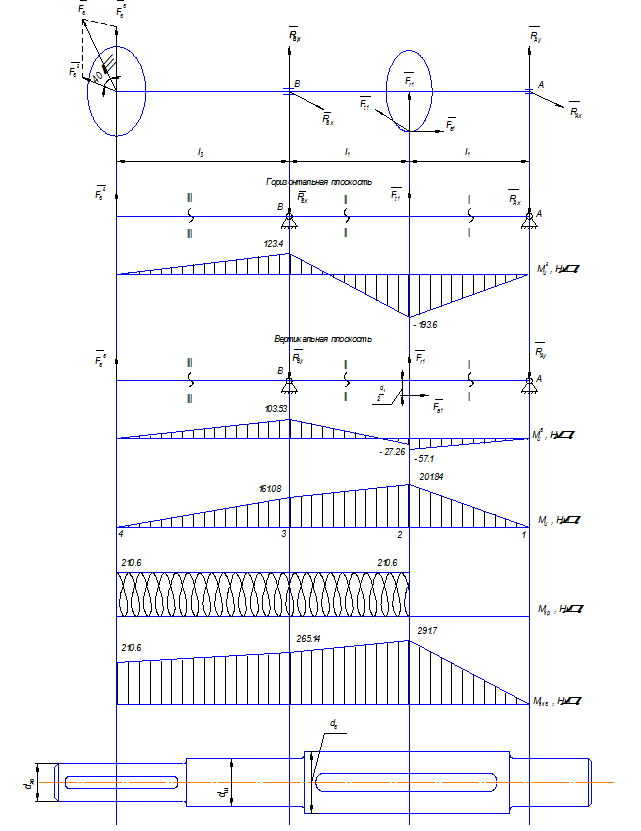
4.Определяем диаметр вала из условия прочности на изгиб:
, где МПа
мм
Учитывая ослабление вала шпоночным пазом, то увеличиваем сечение вала на 5% , но т.к. у нас шпоночный паз отсутствует, то согласно ряду диаметров по ГОСТ 6636 – 69 dв = 40 мм.
Тогда dшипа = dшейки = dв – 10 мм = 40 – 10 = 30 мм
dхв = dш – 10 мм = 30 – 10 = 20 мм
Расчёт вала на выносливость
Определяем действительный запас прочности вала в различных сечениях.
Определяем запас прочности вала в наиболее нагруженном сечении I – I.
Общий запас прочности:
, где [n] = 1,5 … 2,5 … 4
nσ, nτ – запасы прочности по нормальным и касательным напряжениям.
; 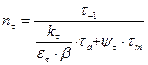
τ-1; σ-1 – пределы выносливости по нормальным и касательным напряжениям.
σ-1 = 0,43· σв = 0,43·610 = 262,3 МПа
τ-1 = 0,6· σ-1 = 0,6·262,3 = 158 МПа
kσ ; kτ – эффективный коэффициент концентрации напряжений, который зависит от обработки поверхности, формы и прочности материала.
; .
Т.к. поверхности валов шлифуются не нижи 1о класса, то и поверхности принимаем равным 1, и 


[2] стр. 300
εσ ; ετ – масштабные факторы, учитывающие абсолютные размеры детали.
εσ = 0,854 и ετ = 0,77 при dв = 32 мм
β – коэффициент шероховатости поверхности вала.
β = 1, т.к. поверхность вала шлифуется.
[2] стр. 298
Ψσ ; Ψτ – коэффициенты симметрии цикла по нормальным и касательным напряжениям, зависят от предела прочности σв.
Ψσ = 0,05 и Ψτ = 0 для σв = 520 … 750 МПа
[2] стр. 299
σа и τa – амплитудные значения нормального и касательного напряжений.
σm и τm – среднее значение нормального и касательного напряжений.
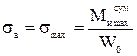
мм3
МПа
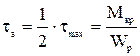
мм3
МПа
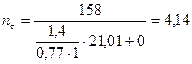

В сечении III – III
МПа
МПа
kσ = 1,7 и kτ = 1,4 (для шпоночной канавки)
εσ = 0,92 и ετ = 0,63 (для шпоночной канавки)
МПа
МПа
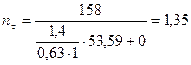
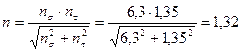
Поскольку n > 1,5 , то нам не нужно увеличивать диаметр хвостовика.
5.3 Составляем схему нагружения второго вала, определяем опорные реакции и строим эпюры нагружения вала, расчет вала ведем в двух плоскостях.
Вертикальная плоскость.
1. Определяем реакции в опорах



Проверка: 
= –1890,12+1842.76+47,36 = 0
2. Строим эпюры нагружения вала от сил, действующих в вертикальной плоскости.
Сечение I - I (справа):

Сечение I - I (слева):

Горизонтальная плоскость.
3. Определяем реакции в опорах

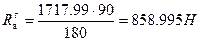
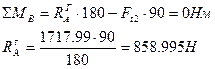

= 858.995-1717.99+858.995=0Н
4.Строим эпюры нагружения вала от сил, действующих в горизонтальной плоскости.
Сечение I - I (слева):

Сечение I - I (справа):

5.строим эпюру крутящего момента: Мкр = 168,26 Нм
6.определяем суммарный изгибающий момент в сечениях и строим суммарную эпюру загружения
сечение I – I: Нм;
7.определяем приведенный (эквивалентный) момент в сечениях
Нм
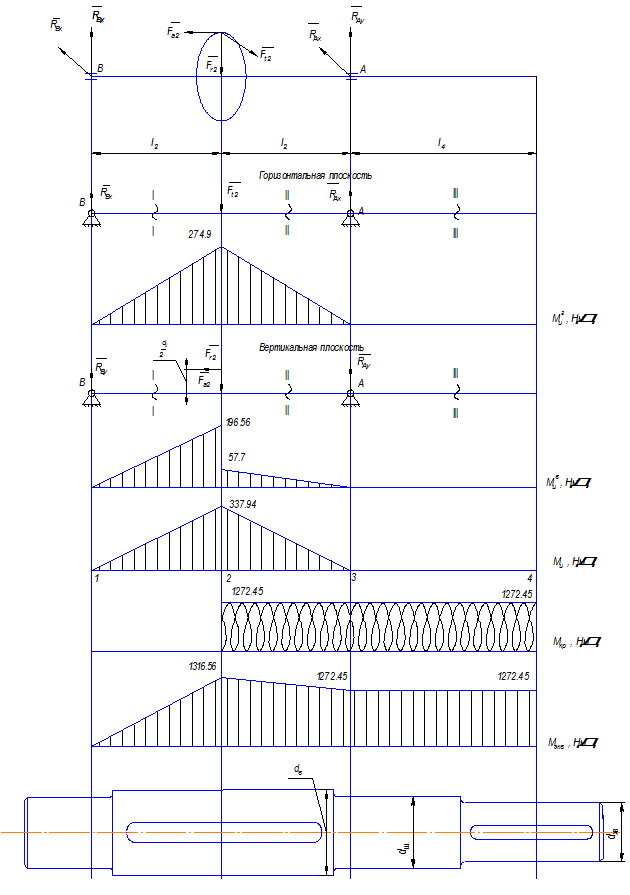
8.определяем диаметр вала в месте наибольшего нагружения на изгиб
, где МПа
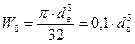
мм
Учитывая ослабление вала шпоночным пазом, то увеличиваем сечение вала на 5% dвI = 54,42+2,721 = 47,141мм
Принимаем dв = 50 мм по ГОСТ 6636-39 учитывая ступенчатую конструкцию вала принимаем :
dш = 40 мм
dхв = 35 мм
Расчёт вала на выносливость
Определяем действительный запас прочности вала в различных сечениях.
Определяем запас прочности вала в наиболее нагруженном сечении III – Ш.
Общий запас прочности:
, где [n] = 1,5 … 2,5 … 4
nσ, nτ – запасы прочности по нормальным и касательным напряжениям.
; 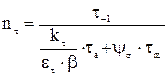
τ-1; σ-1 – пределы выносливости по нормальным и касательным напряжениям.
σ-1 = 0,43· σв = 0,43·610 = 262,3 МПа
τ-1 = 0,6· σ-1 = 0,6·262,3 = 158 МПа
kσ ; kτ – эффективный коэффициент концентрации напряжений, который зависит от обработки поверхности, формы и прочности материала.
; .
Т.к. поверхности валов шлифуются не нижи 1о класса, то и поверхности принимаем равным 1, и 


[2] стр. 300
εσ ; ετ – масштабные факторы, учитывающие абсолютные размеры детали.
εσ = 0,83 и ετ = 0,72 при dв = 60 мм
β – коэффициент шероховатости поверхности вала.
β = 1, т.к. поверхность шеек шлифуется.
[2] стр. 298
Ψσ ; Ψτ – коэффициенты симметрии цикла по нормальным и касательным напряжениям, зависят от предела прочности σв.
Ψσ = 0,05 и Ψτ = 0 для σв = 520 … 750 МПа
[2] стр. 299
σа и τa – амплитудные значения нормального и касательного напряжений.
σm и τm – среднее значение нормального и касательного напряжений.
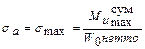
мм3
Подбираем шпонку в зависимости от диаметра вала:
Основные размеры [2] cт.302(в Х h хt1хt2=18х11х7х4,4)


МПа

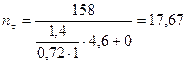

|