Кінематична схема механізма підйому кисневої фурми
МЕТОДИЧНІ ВКАЗІВКИ
для виконання практичних робіт
з предмета: «Механічне та підйомно-транспортне обладнання сталеплавильних цехів»
м. Алчевськ
Розробила: В.С. Стрижак – викладач І категорії
Рецензент: С.Б. Єссельбах – кандидат технічних наук,
професор, викладач кафедри МЧМ ДонДТУ
Затверджено: О.М. Присяжнюк – заступник директора з НР,
голова методичної ради
Розглянуто та схвалено на засіданні предметної комісії металургійних дисциплін
Протокол № _______
від «_____» ________ 2005р.
Голова комісії _________ О.М. Проскуріна
Зміст
Вступ 4
1. Практична робота № 1.
Визначення розмірів барабана та
перевірочний розрахунок його стінки
на міцність, вибір канату 5
2. Практична робота № 2.
Розрахунок потужності електродвигунів
механізмів мостового крана. 12
3. Практична робота № 3.
Розрахунок потужності електродвигуна
привода механізму підйому кисневої
фурми конвертера 17
4. Практична робота № 4.
Визначення завантаженості
стріпперних кранів 20
Вступ
Вирішальну|ухвальну| роль в забезпеченні високої якості металопродукції грають сталеплавильні цехи|. Постійне вдосконалення устаткування|обладнання| сталеплавильних цехів, поліпшення|покращання| технічних показників і підвищення надійності металургійних машин – неодмінна умова технічного прогресу в сталеплавильному виробництві.
Подальше|дальше| нарощування виробництва сталі здійснюватиметься шляхом розвитку киснево-конвертерного виробництва. Особливо важлива|поважна| роль в збільшенні об'єму|обсягу| виробництва і поліпшення|покращання| якості сталі належить кисневим конвертерам, що мають вищу продуктивність і краще технико0-экономические показники, чим мартенівські печі. Поєднання в конвертерах донного і верхнього продування металу киснем розширює їх можливості|спроможності|. В даний час|нині| освоєні і успішно експлуатуються в промисловості великотоннажні кисневі конвертери. Оснащені здійсненими по конструкції приводами повороту, устаткуванням|обладнанням| для завантаження|загрузки| скрапу і заливки чавуну, системами для подачі кисню і сипких матеріалів, сучасні конвертери забезпечують високу продуктивність і точність дозування.
Технічний прогрес в сталеплавильному виробництві нерозривно зв'язаний розвитком машин безперервного литва|лиття| заготовок.
В результаті|унаслідок,внаслідок| виконання практичних робіт студенти повинні уміти:
1. Проводити|виробляти,справляти| розрахунок потужності електродвигунів різних приводів машин і механізмів.
2. Уміти складати і читати кінематичні схеми.
3. Користуватися Гостами, технічною і довідковою літературою.
Практична робота № 1
Тема:Визначення розмірів барабана та перевірочний розрахунок його стінки на міцність, вибір каната.
1. Мета роботи: ознайомитися з методикою розрахунку і вибору канатів, а також вивчити конструкцію барабана механізму підйому та перевірки його стінки на міцність.
2. Початкові дані для розрахунку:
По табличним динним в залежності від номеру за списком вибираємо вхідні данні (таблиця № 1)
Q = 15 m, вантажопідйомність крану.
G = 300 кг, маса крюкової підвіски.
Н =12м, висота підйому.
Режим роботи - середній.
Блоки змонтовані на підшипниках кочення
3. Розрахунок:
3.1 По табличним даним приймаємо, Zц число несучих віток, та η – к.к.д. поліспасту, коефіцієнт запасу міцності к.
3.2. Zц = 6
η = 0,96
к = 5,5
3.3 Визначаємо максимальне зусилля на одну вішку канату.
S = (Q+G)10/Zк * η
S = (15000+300) 10/6 • 0,96 =26563 Н
3.4 Визначаємо розривне зусилля в канаті
Sp = k*S = 5,5 26563 -14609 7 Н.
3.5 По таблиці приймаємо канат типу ЛК-Р 6х19 +1 о.с., з межею витривалості [σ] = 1700 Н/мм, та розривним зусиллям Sk = 151000 Н, діаметр канату dк = 16,5 мм.
3.6 Визначаємо дійсний запас міцності канату.
Кд = S*Z*η/(Q + G)10 = 151000-6-0,96/(15000+300)10 = 5,68
Дійсний запас міцності канату перевищує розрахунковий, отже канат вибрано вірно.
3.7 Визначаємо діаметр барабану по дну канавки.
Dб = dK (е-1),
де е- коефіцієнт, який залеже від режиму роботи.
Dб = 16,5 • 24 = 396 мм.
Згідно зі стандартного ряду приймемо діаметр рівний 400 мм.
3.8 Визначаємо діаметр барабана по центрам каната.
D=Dб + dK = 400 +16,5 = 416,5 мм.
3.9 Приймаємо матеріал барабана сталь 35Л, так як механізм працює у важких умовах.
3.10 Визначаємо товщину спинок барабана.
δ = (l,l+l,2) * dк
δ = 1,15-16,5 = 19 мм.
Для чавунних барабанів δ = 0,02-D6 + (6... 10), виходячи з умов виготовлення чавунних барабанів товщина спинки повинна бути не менше ніж 12 мм.
3.11 Визначний внутрішній діаметр барабана.
Do = 06-23=400 -219 = 362 mm.
3.12 Визначаємо шаг нарізки
t = dk + (2...3мм)
t =16,5+2,5=19 mm.
3.13 Визначаємо глибину канавки.
С = (0,25...0,4)dк = 0,35 16,5 = 6 мм.
3.14 Визначаємо радіус канавки.
К=0,6...0,74к=0,616,5 = 10мм.
3.15 Визначаємо довжину канату.
Lk =Н * і, м
де і – кратність поліспаста
i=Z/2 = 6/2 = 3.
Lk = 12000 * 3 = 36000мм = 36м.
3.16 Визначаємо число витків нарізки на одній половині барабана.
Z = Lk / π Dб + (1,5 ...2)= 36000/3,14400 +2 = 31
3.17 Визначаємо довжину парики на одній половини барабана.
lн=Zt
Ін=31 * 19 = 589 мм.
3.18 Визначаємо довжину нарізки з кожної сторони барабана, яка використовується для закріплення канату.
Із =4t,
Із =4 19 = 76.
3.19 Визначаємо відстань між правою та лівою нарізками.
L = b-2h-tgα,
де b — відстоїть між осями ручаїв крайніх блоків,
b = 268 мм.
h - відстань між віссю барабана і віссю блоків, що рухається в крайньому верхньому положенні вантажу.
h = 650 мм.
α - кут відхилення, α = 4…6° приймаємо α =4°.
L= 268 -2 650 tg4°= 177 мм.
3.20 Визначаємо повну довжину барабана.
L6 = 2 (Із + Іh)L = 2 (589 + 76) * 177=1507 мм.
3.21 При L <5*D перевірка стінок барабану виконується тільки на стискання, а при L> 5*D перевірка виконується на стискання, згин та кручення,
5D = 5* 416,5 = 2082,5 мм, >L= 1507
3.22 Перевіряємо стінки барабана на стискання
σc= S1/St < [σс]
де - [σс] - допустиме напруження на стисканні для сталі 35Л, [σс] = 140 Н/мм
σс = 26563/1919 = 73,58 Н/мм <[σс] = 140 Н/мм
Напруження на стискання менше німе допустиме, отже барабан відповідає умовам міцності.
При L>5D, необхідно перевірити барабан по таких формулах
3.23 Витрачаємо крутний момент, який передає барабан
Мкр = S1D = 26563 * 0,4165=11063,49 Нм.
3.24 Визначаємо згинаючий момент
Мзг = S1l/
де l/ - відстань від точки прикладання зусилля S1 до середини торгового диску барабана
l/ = ін * (0,01...0,02)
l/ = 0,589 * 0,015 = 0,574 м.
Мзг = 26563 -0,574 = 15247,16 Нм
3.25 Визначаємо екваторіальний момент опору перерізу барабана
W=0,1Dб - Do/Do,
W= 0,1* 0,4 - 0,362 /0,362 = 0,002328 м
3.26 Визначаємо сумарне напруження від згину та кручення
σ = Мзг. + (φ •Мкр) /W
де φ — коефіцієнт приведення напружень, φ = 0,75
φ = 15247,16 + (0,75 • 11063,49) /0,002328 = 7,46 Н/мм
3.27 Визначаємо процент сумарного напруження від напруження стискання.
σ /[σ с]100%<15%
7,46/140100% = 5,33%< 15%.
Висновок; напруження від згину та кручення в стінці барабана не перевищують 15 % від напружень стискання, отже умови міцності виконані.
Таблиця № 2 - Кількість вішок поліспасту в залежності від вантажопідйомності
Вантажопідйомність
| Кількість несучих вішок
| Головний підйом
| Допоміжній підйом
|
|
| -
|
|
| -
| 15/3
|
|
| 20/5
|
|
| 30/10
|
|
| 50/10
|
|
| 75/15
|
|
| 100/20
|
|
| 125/20
|
|
|
Таблиця № 3 – к.к.д. поліспаста
Кількість
несучих вішок
| Кількість блоків,
що обертаються
| Кратність
поліспаста
| Коефіцієнт запасу міцності
К
| к.к.д
| Підшипник кочення
| Підшипник ковзання
|
|
|
|
| 0,98
| 0,94
|
|
|
| 5,5
| 0,96
| 0,92
|
|
|
|
| 0,94
| 0,90
|
|
|
|
| 0,92
| 0,88
|
|
|
|
| 0,91
| 0,85
|
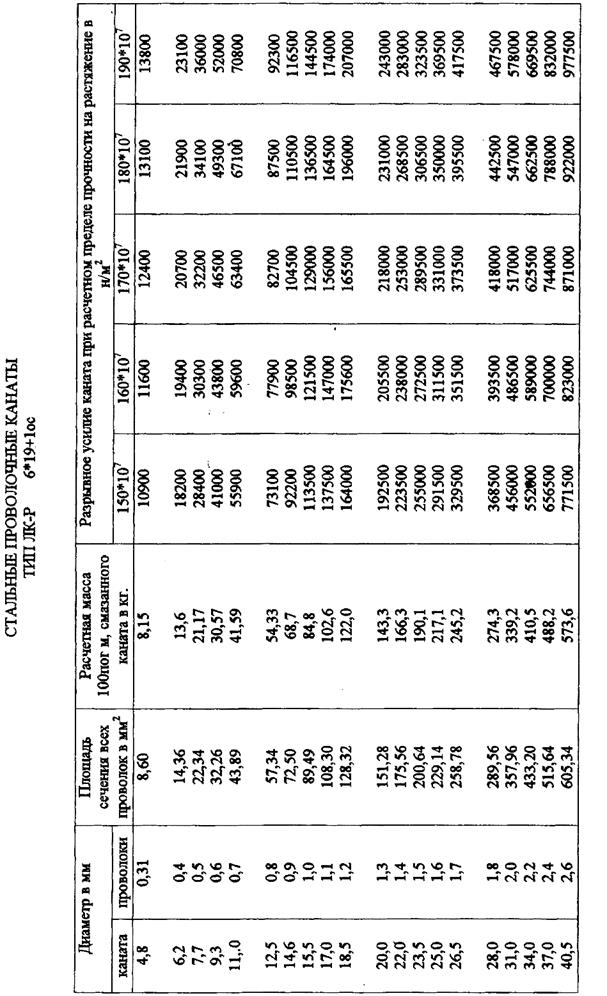
Таблиця № 1 – Початкові дані до практичної роботи № 1
№ варіанту
| Q, т
| G, кг
| Н, м
| Режим робіт
| Блоки змонтована підшипниках
|
|
|
|
| Легкий
| Ковзання
|
|
|
|
| Легкий
| Ковзання
|
|
|
|
| Легкий
| Ковзання
|
|
|
|
| Легкий
| Ковзання
|
|
|
|
| Середній
| Ковзання
|
|
|
|
| Середній
| Ковзання
|
|
|
|
| Середній
| Ковзання
|
|
|
|
| Середній
| Кочення
|
|
|
|
| Середній
| Кочення
|
|
|
|
| Середній
| Кочення
|
|
|
|
| Середній
| Кочення
|
|
|
|
| Середній
| Кочення
|
|
|
|
| Середній
| Кочення
|
|
|
|
| Середній
| Кочення
|
|
|
|
| Середній
| Кочення
|
|
|
|
| Важкий
| Кочення
|
|
|
|
| Важкий
| Кочення
|
|
|
|
| Важкий
| Кочення
|
|
|
|
| Важкий
| Кочення
|
|
|
|
| Важкий
| Кочення
|
|
|
|
| Важкий
| Кочення
|
|
|
|
| Важкий
| Кочення
|
|
|
|
| Важкий
| Кочення
|
|
|
|
| Важкий
| Кочення
| 4. Контрольні питання:
1. Які розрізняють види вантажопідйомних машин по значенню, принципу дії?
2. приведіть схеми і опис основних типів вантажопідйомних машин (домкрата, лебідки, талі).
3. Що таке відносна тривалість включення|приєднання| (ПВ| %)
4. Як враховується режим роботи при визначенні розрахункових навантажень?
5. За яких умов застосовують універсальні і спеціальні вантажопідйомні пристосування?
6. Опишіть однорогі і дворогі вантажні крани, їх контур, конструкція, матеріал, технологію виготовлення.
7. Пластинчасті|пластинчаті| крюки|гаки|: матеріал, технологія виготовлення, область застосування|вживання|.
8. Як підбираються крюки|гаки| по Госту?
9. У чому переваги барабана з|із| гвинтовою нарізкою?
10. Як визначається довжина барабана?
11. Що таке поліспаст|?
12. Які бувають поліспасти|?
13. Як визначається кратність поліспаста|?
14. Призначення підвісів, крюків|гаків|.
Висновок
6. Література:
1. Александров В.П. Подъемно-транспортные машины. М. «Высшая школа», 1985, 570 с.
2. Виниолии И.И. Механическое и транспортное оборудование сталеплавильных цехов. М. «Металлургия», 1972, 2-е издание, 368 с.
Практична робота № 2
Тема: Розрахунок потужності електродвигунів
механізму мостового крану.
Мета роботи
Оволодіти методикою розрахунку потужності електродвигуна привода механізму підйому кисневої фурми конвертора.
Початкові дані
2.1. Згідно з табличними даними в залежності від номеру по списку вибираємо вихідні донні
Q = 36m = 36000 кг - вантажопідйомність крану;
G = 350 кг - маса крюкової підвіски;
Vв = 75 м/хв — 0,25 м/с - швидкість підйому вантажу;
Вб = 710 мм - діаметр барабану;
ТВ = 30% - тривалість включення;
Режим роботи — середній.
Розрахунок
3.1 Визначаємо потужність двигуна
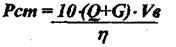
де η - коефіцієнт корисної дії механізму (к.к.д.)
η = 0,85.
Рст =10 (36000 + 350) – 0,25/0,85 = 106912 Вт
3.2 Визначаємо номінальну потужність двигуна.

де ТВн – стандартне значення тривалості включення.
Режими роботи
| ТВ у %.
| Легкий
| 15%
| Середній
| 25%
| Важкий
| 40%
| Дуже важкий
| 60%
|
Приймаємо ТВ = 25 %.

3.3 По знайденому значенню потужності вибираємо двигун типа МТН 712 -10 з потужністю Рдв = 125 кВт (при ТВ = 40%) з частотою обертання ротора nдв = 585 об/хв, з максимальним моментом Мтах = 5800 Нм. Маховий момент GD = 510Hm.
3.4 Визначаємо частоту обертання барабану.
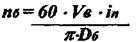
де in - кратність поліспаста, згідно табличних даних in = 4.
nб = 60-0,25 4/3,14 -0,71 = 26,91 об/хв.
3.5. Визначаємо передаточне відношення механізму
Up = nд/nб = 585/26,91=21,74.
3.6 Редуктор механізму підйому вибираємо, враховуючи потужність на швидкохідному валу редуктора, частоту обертання його швидкохідного вала, передаточне відношення та заданий режим роботи механізму. Вибираємо редуктор циліндричний горизонтальний двоступінчатий крановий типорозміру Ц2У- 650 -19,88 - 4М. Сумарна міжосьова відстань аw=650mm, передаточне відношення U = 19,88, схема збірки 4, вал тихохідний з кінцем під зубчасту муфту.
3.7 Визначаємо фактичну частоту обертання барабана
пб.ф = n/U= 585/19,88=29,43 об/хв.
3.8 Визначаємо фактичну швидкість підйому вантажу.
Vвф.= π Dб nб.ф./60 іn = 0,273 м/с.
3.9 Визначаємо статичний момент приведений до валу двигуна.
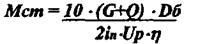
Мст =10 (36000+350)-0,71 /2419,88-0,85 = 1909,14 Нм.
3.10 Визначаємо динамічний момент, який затрачується на прискорення мас, які рухаються поступально.
Мд1 = 10 * (Q+G) * Dб nд/375 * tp * Up * in * η
де tn – час розгону механізму, tn 5 Vв.ф., tn = 5 * 0,273 = 1,356 с.
Мд1 = 10 * (36000+350) * 0,71 * 585/375 * 1,365 * 19,88 * 4 * 0,85= 38,96 Нм .
3.11. Визначаємо динамічний момент, який затрачується на прискорення мас, які обертаються.
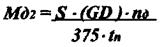
де — S- коефіцієнт, який враховує махові моменти деталей механізму
S = 1,1 1,25.
Мд2 = 1,2-510-585/3751,365 = 699,43 Нм .
3.12 Визначаємо пусковий момент двигуна.
Мn = Мст + Мд1+ Мд2 = 1909,14+38,96+699,43=2647,53 Нм.
3.13 Визначаємо номінальний момент двигуна.
Мн=Рд/ω
де ω- кутова швидкість двигуна.
ω = π n/30 = 3,14-585/30 = 61,23 с-1 (рад/сек)
Мн = 125*1000/61,23 = 2041,48 Нм.
3.14 Перевіряємо вибраний електродвигун на фактичну кратність пускового моменту.
λ = Mn / Мст < [λ]
де [λ] - допустима кратність пускового моменту
[λ] = Mmax / Мн = 5800/2041,48=2,84
λ= 5800/2041,48 = 2,84 1 = 2647,53/1909,14 = 1,39.
Якщо λ [λ], то вибраний двигун відповідає умовам роботи механізму. Якщо λ > [λ], то необхідно вибрати інший двигун більшої потужності, по таблицям та перевірити його на перевантаження по формулам пунктів 2.9 — 2.14.
Таблиця - значення к.к.д. основних частин кранового механізму підйому.
Найменування елементів
| мед.
|
При опорах
|
ковзання
| кочення
| Відкриті зубчасті передачі: Ціліндричні Конічні
| 0,93*0,95 0,92*0,94
| 0,95*0,96 0,93*0,95
| Закриті зубчасті передачі та редуктори:
| 0,95*0,97
| 0,97*0,98
| Черв'ячні передачі (редуктори): при однозахідному черв'яку при двозаходному черв'яку
| 0,50*0,75 0,75*0,80
| 0,50*4,75 0,75*0,80
| Блоки та барабани для стальних канатів:
| 0,94*0,96
| 0,96*0,98
| Зубчасті та інші види муфт:
| 0,99
| 0,99
| Механізми підйому вантажу: з ціліндричними зубчастими передачами з черв'ячною передачею
| 0,75*0,80 0,65*075
| 0,80*0,85 0,65*0,75
|
Таблиця - Кратність поліспасту при різних вантажопідйомностях.
Характер навивання
канату на барабан
| Тип поліспаста
| In при вантажопідйомності, Н
|
До 1
| 2...6
| 10...15
| 20.. .30
| 40...50
| Безпосередньо (наприклад мостові крани та талі)
| Здвоєний простий
|
|
| 2,3
-
| 3,4
-
| 4,5
-
| Через напрямний блок, (наприклад стрілові крани)
| Простий здвоєний
| 1,2
-
| 2,3
| 3,4
2,3
| 5,6
-
| -
-
|
Таблиця - вхідні данні до практичної роботи № 2
Номер варіанту.
| Q, т
| G,кг
| Vгр, м/хв
| Dб, мм
| ТВ,%
| Режим роботи
|
|
|
|
|
|
| легкий
|
|
| ПО
| 15,5
|
|
| легкий
|
|
|
|
|
|
| легкий
|
|
|
| 14,5
|
|
| легкий
|
|
|
|
|
| І5
| середній
|
|
|
| 13,5
|
|
| середній
|
|
|
|
|
|
| середній
|
|
|
|
|
|
| середній
|
|
|
| 11,5
|
|
| середній
|
|
|
|
|
|
| середній
|
|
|
| 10,5
|
|
| середній
|
|
|
|
|
|
| середній
|
|
|
| 9,5
|
|
| середній
|
|
|
|
|
|
| середній
|
|
|
| 8,5
|
|
| важкий
|
|
|
|
|
|
| важкий
|
|
|
| 7,5
|
|
| важкий
|
|
|
|
|
|
| важкий
|
|
|
| 6,5
|
|
| важкий
|
|
|
|
|
|
| важкий
|
|
|
| 5,5
|
|
| важкий
|
|
|
|
|
|
| важкий
|
|
|
| 4,5
|
|
| важкий
|
|
|
|
|
|
| важкий
| 4. Контрольні питання
1. Який привід вантажопідйомних машин ви знаєте?
2. У яких кранах використовується ручний привід?
3. Що таке «кішка»?
4. Приведіть формулу передавального числа ручної лебідки?
5. Що входить до складу електроприводу ПТМ|.
6. Призначення останов. Приведіть схему крана останов.
7. Перерахуйте типи гальм.
8. Призначення мостових кранів.
9. Як класифікуються крани залежно від типу вантажозахватних пристроїв|устроїв|?
10. Призначення кран-балки.
11. З|із| яких вузлів складається мостовий кран загального|спільного| призначення.
12. Які приводи механізму пересування крана ви знаєте.
13. Приведіть кінематичну схему механізму пересування ножа:
а) з|із| швидкохідною трансмісією;
б) з|із| тихохідною трансмісією;
в) з|із| індивідуальним приводом.
Висновок
6. Література:
1. Виниолии И.И. Механическое и транспортное оборудование сталеплавильных цехов. М. «Металлургия», 1972, 2-е издание, 368 с.
2. Александров В.П. Подъемно-транспортные машины. М. «Высшая школа», 1985, 570 с.
Практична робота № 3
Тема: Розрахунок потужності електродвигуна привода
механізму підйому кисневої фурми конвертора.
Мета роботи
Оволодіти методикою розрахунку потужності електродвигуна привода механізму підйому кисневої фурми конвертора.
Початкові дані
2.1. Швидкість підйому фурми Vф = 0,25 – 0,5 м/с
2.2. Висота підйому фурми Н = 6,35 м
2.3. Тягове зусилля на барабані F= 38 кН
2.4. Швидкість навивання каната на барабані Vк = 0,98 – 1,0 м/с
2.5. Дані, яких не вистачає для розрахунку, вибрати самостійно.
Кінематична схема механізма підйому кисневої фурми
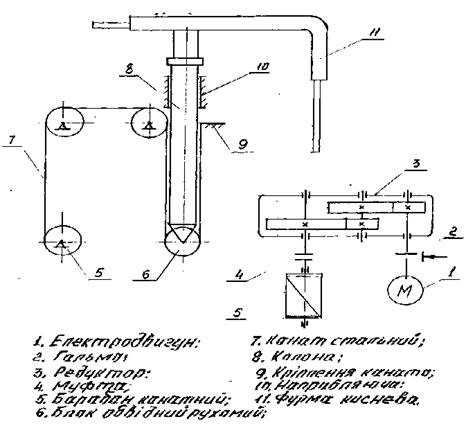
Розрахунок

4.1. Визначаємо статичну потужність електродвигуна
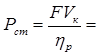
де η = 0,9 – орієнтовний ККД редуктора.
В приводі механізму підйому кисневої фурми установлений електродвигун:
Тип МП – 52
Потужність 40 кВт
Число обертів ротора 635 об/хв.
Частота включення ТВ = 25%
4.2. Визначаємо розривне зусилля в канаті
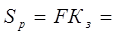
де Кз =5,5 – коефіцієнт запасу міцності каната для середнього режиму роботи по ДОСТ 2677-80 приймаємо канат
4.3. Визначаємо діаметр барабана

4.4. Визначаємо кутові швидкості:
а) електродвигуна
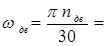
б) канатного барабана
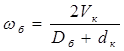
в) Визначаємо передатне відношення редуктора
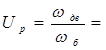
По каталогу приймаємо редуктор з наступною характеристикою:
1. Тип РМ-650
2. Швидкість обертання вхідного вала n = 750 об/хв.
3. Передаточне число Up =
4. Потужність на вхідному валі Рвх =
5. Частота включення ТВ =
5. Контрольні запитання
1. Які приводи конвертера ви знаєте?
2. Призначення приводу конвертора.
3. Яка швидкість повороту конвертора при сливі стали і шлаку?
4. Чому вісь обертання конвертора повинна бути вище за загальний|спільний| центр тяжіння?
5. Що є фурма?
6. Чому фурми з|із| центральним підведенням кисню одержали|отримали| широке застосування|вживання| в порівнянні з фурмами| з|із| центральним підведенням охолоджуючої води?
7. Що вважається|лічиться| важливим|поважним| конструктивним вузлом будь-якої фурми?
8. Чим контролюється положення|становище| фурми в конвертері?
9. Перерахуйте типи машин для подачі кисню в конвертер.
10. Які недоліки|нестачі| мають стаціонарні машини для подачі кисню в конвертер?
11. З якою метою здійснюють з'єднання|сполучення,сполуку| приводу конвертера з|із| цапфами універсальними шпінделями|шпинделями|?
12. Яка номінальна швидкість переміщення фурми?
Таблиця 5 – Початкові дані до практичної роботи №3
№ варіанту
| V, м/с
| Н, м
| F, кН
| Vk, м/с
|
| 0,25
| 5,0
|
| 0,8
|
| 0,27
| 5,25
|
| 0,82
|
| 0,29
| 5,35
|
| 0,84
|
| 0,31
| 5,45
|
| 0,86
|
| 0,33
| 5,5
|
| 0,88
|
| 0,35
| 5,65
|
| 0,9
|
| 0,37
| 5,75
|
| 0,92
|
| 0,49
| 5,85
|
| 0,94
|
| 0,50
| 5,9
|
| 0,96
|
| 0,26
| 6,0
|
| 0,98
|
| 0,28
| 6,15
|
| 1,0
|
| 0,30
| 6,25
|
| 0,95
|
| 0,34
| 6,35
|
| 0,91
|
| 0,36
| 6,45
|
| 0,84
|
| 0,32
| 6,55
|
| 0,86
|
| 0,40
| 6,75
|
| 0,88
|
| 0,42
| 6,85
|
| 0,97
|
| 0,44
| 6,95
|
| 0,95
|
| 0,39
| 7,0
|
| 0,93
|
| 0,48
| 5,15
|
| 0,91
|
| 0,45
| 5,6
|
| 0,89
|
| 0,41
| 5,8
|
| 0,837
|
| 0,47
| 6,4
|
| 0,85
|
| 0,28
| 6,8
|
| 0,83
|
| 0,26
| 6,28
|
| 0,81
|
Висновок
Література
1. Целиков Л.И. и др. Машины и агрегаты металлургических заводов. Т II. М., “Металлургия”, 1987 г.
2. В.М. Гребеник и др. Расчет металлургических машин и механизмов. К. “Вища школа”, 1988 г.
3. Виниолии И.И. Механическое и транспортное оборудование сталеплавильных цехов. М. «Металлургия», 1972, 2-е издание, 368 с.
4. Левин М.З. и др.. Механическое и транспортное оборудование сталеплавильных цехов. Киев. «Высшая школа», 1985, 165 с.
Практична робота № 4
Тема: Визначення завантаженності стриперних| відділень|відокремлень|
Мета|ціль|: визначити завантаженість стриперних| кранів і провести|виробити,справити| розрахунок його механізмів
У цеху запроектовані два стриперних| крап УЗТМ| 250/50, т. За даними хронометражу, заборгованість крапу па один злиток|зливок| спокійної сталі (зняття надставки, випробування злитка|зливка|) складає 2 мін, а для киплячої сталі (зняття злитка|зливка| разом з виливницею і установка їх на допоміжний склад) 1,4 мин. Приймаємо, що на допоміжні операції витрачається 20% часу основних операцій, а коефіцієнт нерівномірності роботи крана складає 1,2.
Визначимо число крано-годин, необхідного для виконання всіх операцій в стриперном| відділенні|відокремленні| при повному|цілковитій| виробництві цеха.
крано-годин
Крім того, слід врахувати 1,5 ч на огляд і дрібний|мілкий| ремонт кожного крана. Таким чином, для двох кранів необхідно 42 крано-години.
Визначимо завантаженість двох кранів:
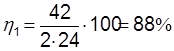
Для більшої гарантії безперебійної роботи цеху, якщо один з кранів зупинять на тривалий ремонт, слід передбачити в цеху третій кран чи стаціонарний товхач, що обслуговується прибиральним мостовим краном. При трьох стриперних| кранах завантаженість сягне:
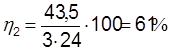
По табл. 4.1 в залежності від номеру по списку вибираємо вихідні дані.
2. Розрахунок механізмів стриперного| крана (механізм виштовхування)
2.1. Визначаємо діаметр гвинта, запровадивши розрахунок на деформацію стиснення|стискування|:
, мм (4.1)
де: 1,375 F — розрахункове завдання, (F — максимальне навантаження на вінт, н);
[σ]— допустиме напруження на стискання|стискування|, МПа;
d1 — внутрішній діаметр різьби гвинта, мм.
2.2 Визначаємо зовнішній діаметр гвинта по імперічному співвідношенню
мм (4.2)
де d — зовнішній діаметр гвинта, мм.
2.3. Визначаємо середній діаметр гвинта:
, мм (4.3)
2.4. Визначаємо шаг правої та лівої різьби| двоходового| гвинта:
S = 2t ,мм (4.4)
де t — відстань між сусідніми витками різьби, мм
2.5. Визначаємо хід штемпіля при одному обороті|звороті,оберті| гвинта:
Sшт = 2S,мм (4.5)
2. 6. Визначаємо число витків кожної нарізної частини|частки| гвинта:
(4.6)
де: 2 — число ходів;
l — довжина нарізаної частини|частки| гвинта, мм;
2.7. Число витків гайки визначаємо з|із| умов:
а) питомного тиску|тиснення|
, Па (4.7)
б) деформація зрізу
, Па (4.8)
де [q] —питомний тиск|тиснення| при бронзовій гайці [q] = 10 · 104 Па (100 кГ/см2);
[τ]ср = 0,6 [σ]ст , МПа
h = 0,7 t — для трапецеїдальної різьби.
Із|із| отриманих результатів обираємо найбільше число витків.
2.8. Визначаємо кут|ріг,куток| нахилу гвинтової лінії:
, де rср – середній радіус гвинта (4.9)
2.9. Приймаємо к.к.д. гвинта:
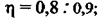
2.10. Визначаємо обертовий момент, для визначення опору тертя нарізці гвинта:
, Н·м (4.10)
2.11. Перевіряємо гвинт на повздовжній згин|згин|:
, Н/м2 (4.11)
де:
, м2 А - площа|майдан| поперечного перерізу
φ— коефіцієнт зменшення напруження|напруження|, обираємо з табл. в залежності від згину, приймаємо: φ = 0,846.
Гнучкість
(4.12)
де l — довжина гвинта, мм; ri — радіус інерції
, мм
де I — момент інерції (4.13)
, мм2 (4.14)
2.12. Визначаємо потужність електродвигуна стриперного| механізму;
, Вт (4.15)
де: F — максимальне зусилля штемпеля, н;
ηмех = 0,6 — к. п. д. механізму;
к — коефіцієнт перевантаження двигуна, к = 1 - 1,2.
2.13. Визначаємо передаточне число механізму:
(4.16)
де: nдв — число оборотів|зворотів,обертів| двигуна в хв-1;
nв — число оборотів|зворотів,обертів| гвинта в хв-1.
(4.17)
де: υ – max швидкість штемпеля; υ = 2,5-3 м/хв
Таблиця 4.1 – початкові дані до ПРП № 4.
№
| Вантажо-підйомність
Q,t. e.
| Коефіцієнт нерівномірної роботи крана
K
| Розрахункове зусилля
F,Кh
| Напруга|напруження|, що допускається, на стиснення|стискування|
[σ]ст МПа
| Відстань між сусідніми витками різьблення
t, мм
| Довжина нарізної частини|частки| гвинта
l, мм
|
| 200/30
|
| 5.000
|
|
|
|
| 200/30
|
| 6.000
|
|
|
|
| 200/30
|
| 7.000
|
|
|
|
| 200/30
|
| 8.000
|
| 1,5
|
|
| 210/40
| 1,1
| 9.000
|
| 1,5
|
|
| 210/40
| 1,1
| 10.000
|
| 1,5
|
|
| 210/40
| 1,1
| 11.000
|
| 1,5
|
|
| 210/40
| 1,1
| 12.000
|
|
|
|
| 220/40
| 1,15
| 13.000
|
|
|
|
| 220/40
| 1,15
| 14.000
|
|
|
|
| 220/40
| 1,15
| 15.000
|
| 2,5
|
|
| 230/45
| 1,15
| 16.000
|
| 2,5
|
|
| 230/45
| 1,15
| 17.000
|
| 2,5
|
|
| 230/45
| 1,15
| 18.000
|
| 2,5
|
|
| 240/45
| 1,2
| 19.000
|
|
|
|
| 240/45
| 1,2
| 20.000
|
|
|
|
| 240/45
| 1,2
| 21.000
|
|
|
|
| 250/50
| 1,2
| 22.000
|
|
|
|
| 250/50
| 1,2
| 23.000
|
|
|
|
| 250/50
| 1,2
| 24.000
|
|
|
|
| 250/50
| 1,2
| 25.000
|
|
|
|
Література:
1. Целиков Л.И. и др. Машины и агрегаты металлургических заводов. т. ІІ. М., «Металлургия», 1987г.
2. Виниолии И.И. Механическое и транспортное оборудование сталеплавильных цехов. М. «Металлургия», 1972, 2-е издание, 368 с.
|