Применение функции желательности для выбора материалов и упрочняющих технологий Цель работы: 1. На основании данных, полученных на предыдущих практических занятиях, выбрать марку материала и назначить технологию термической обработки для изделия.
1 Основные сведения
Рекомендации по решению задач. Выбор сплава и упрочняющей обработки для деталей машин и станков является ответственной и весьма сложной инженерной задачей. Правильное решение поставленной задачи в значительной степени определяет надежность, долговечность, точность и стоимость отдельных деталей и, в конечном счете, всей конструкции.
В задачах, приведенных ниже, требуется выбрать марку сплава и способ упрочнения для типовых деталей, наиболее часто встречающихся в машинах и станках (валы; зубчатые и червячные колеса; шпиндели; пружины; направляющие скольжения и качения; станины и т. д.).
Для решения поставленной задачи, прежде всего, необходимо проанализировать условия эксплуатации данной детали, а также выяснить требования, предъявляемые конструктором к механическим свойствам материала (сплава) из которого будет изготавливаться деталь.
В свою очередь механические свойства сплава будут определяться не только выбором химического состава (марки) сплава, но и способом его упрочнения (термическая; химико-термическая; термомеханическая обработка и др.). Кроме того, механические свойства сплава будут зависеть и от технологического режима упрочняющей обработки (температура; время выдержки; скорость охлаждения; состав газовой или жидкой среды при химико-термической обработке).
Типичные условия работы детали и основные требования к свойствам материала описаны для каждой типовой детали в соответствующем разделе. Исходя из этого, в каждом разделе приведены наиболее часто применяемые для изготовления типовых деталей сплавы (марки сплавов). Однако, в каждой конкретной задаче условия работы детали и, следовательно, требования к механическим свойствам материала могут существенно отличаться. Эти отличия в конечном итоге и будут определять выбор марки сплава и режима его упрочняющей обработки.
Наиболее сложной задачей и обязательной частью задания является обоснование выбора сплава и способа его упрочнения. Во всех случаях при обосновании выбора сплава и способа упрочнения рекомендуется придерживаться следующей последовательности.
1. Предварительно выбрать тип сплава (сталь, чугун, бронза и т.д.) в соответствии с условиями работы и требованиями, предъявляемыми конструктором к механическим свойствам материала.
2. Оценить необходимость применения упрочняющей обработки для выбранного сплава1. При этом главным критерием является уровень механических свойств, который необходимо обеспечить по условию задачи.
1 В случаях, когда детали работают при малых динамических нагрузках (например, валы большого диаметра с небольшой частотой вращения) упрочняющая обработка изделия не требуется и они применяются со структурой и, следовательно, механическими свойствами, которые имел сплав в состоянии поставки, т.е. после отжига или нормализации.
3. При необходимости упрочняющей обработки выбрать путем сравнения тот или иной способ упрочнения сплава, учитывая следующие факторы:
- требования к механическим свойствам поверхности и сердцевины изделия;
- требования к деформации изделия после упрочняющей обработки, что определяет в итоге точность размеров детали;
- производительность, трудоемкость и себестоимость упрочняющей обработки.
4. Рекомендовать марку сплава с учетом выбранного способа упрочнения.При этом необходимо учитывать:
- механические свойства сплава, которые можно получить в том или ином сечении, сравнивая с сечением детали;
- прокаливаемость выбранного сплава (для сталей приводится в справочнике), которая определяет однородность структуры и, следовательно, свойств сплава по сечению детали (важно для деталей, работающих при высоких напряжениях и, особенно, динамических нагрузках, которые воспринимает все сечение детали);
- среду охлаждения при закалке (вода, масло), что определяет величину остаточных напряжений и, следовательно, величину деформации и опасность возникновения трещин (важно для деталей малой жесткости, сложной формы, тонкостенных и имеющих концентраторы напряжений);
- сравнительную стоимость сплава, которую можно определить по количеству и дефицитности легирующих компонентов.
Во всех задачах необходимо выполнить следующее:
обосновать выбор сплава и способа упрочнения;
- привести химический состав выбранного сплава;
- привести последовательность операций термической или химико-термической обработки;
- для каждой операции привести режимы обработки (температура; время выдержки; скорость охлаждения; состав газовой или жидкой среды при химико-термической обработке; глубину упрочненного слоя);
- указать структуру и механические свойства сплава после окончательной обработки;
- если возможны варианты замены сплава и метода упрочнения, то сравнить их по трудоемкости и производительности.
Стальные накладные направляющие на. Станины станков.Стальные накладные направляющие скольжения и качения - одна из наиболее ответственных групп деталей станков, от которых зависит точность и долговечность всего станка. Как правило, стальные накладные направляющие работают в интенсивно изнашиваемых узлах станков в условиях абразивного загрязнения; в станках с программным управлением и обрабатывающих центрах; в универсальных легких и средних станках; в станках, предназначенных для работы в условиях массового и крупносерийного производства (токарные одношпиндельные и автоматы, полуавтоматы, сверлильные, фрезерные и другие станки). Стальные накладные направляющие изготавливают в виде планок прямоугольной и треугольной форм и в виде пластин толщиной от 10 до 100 мм и длиной до 2000 мм и более.
К рабочей поверхности накладных направляющих скольжения предъявляется ряд общих требований: высокая износостойкость, а для направляющих качения, кроме того, высокое сопротивление циклическим контактным нагрузкам (контактные напряжения достигают 2300¸2500МПа).
Для получения высокой износостойкости и контактной выносливости твердость стальных накладных направляющих должна составлять не менее 58¸59НRС, а толщина упрочненного слоя - не менее 1,2 мм. Кроме того, после упрочняющей обработки накладные направляющие должны иметь минимальное коробление, которое зависит от выбора марки стали, метода упрочнения и жесткости детали (размеры сечения и длина направляющих). Чем больше жесткость направляющей, тем меньше ее деформация и коробление в результате упрочняющей термической обработки.
Оценить жесткость длинномерных деталей в процессе их термической обработки можно условно, используя показатель Кж определяемый по формуле:
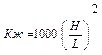
где Н - наружный диаметр детали, преобладающий по ее длине, или наименьший характерный размер ее поперечного сечения, мм; L - длина детали, мм.
В зависимости от величины показателя Кж длинномерные детали разделяют на три категории жесткости: высокая, средняя и малая (табл.1).
Для упрочнения стальных накладных направляющих применяют объемную закалку, а также поверхностные методы упрочнения. Однако для направляющих с Кж <2,0 (некруглая форма деталей) объемная закалка не применяется из-за значительного коробления. Наиболее часто для изготовления направляющих станков в зависимости от способа их упрочнения, жесткости, требований к точности, контактной выносливости применяют следующий ряд сталей: подшипниковые стали - ШХ15, ШХ15СГ; инструментальные стали - У10А, ХВГ, ХВСГ, 9ХС, 8ХФ, 7ХГ2ВМ2; цементуемые стали - 20Х, 18ХГТ, 25ХГТ, 12ХНЗА; азотируемые стали - ЗОХЗМФ, 38Х2МЮА, 20ХЗМВФА; и другие стали.
Таблица 3.1.
Показатель жесткости деталей различной формы.
Категория жесткости
| Показатель жесткости Кж для деталей с формой поперечного сечения
|
| Круглой
| некруглой
| Малая
| до 2,5
| до 4,5
| Средняя
| св.2,5 до 4,5
| св.4,5 до 7,5
| Высокая
| св. 4,5
| св. 7,5
|
Выбор и обоснование комплекса необходимых свойств для пружины подвески автомобиля. Для определения комплекса необходимых свойств для данной детали нам необходимо обратиться к условиям эксплуатации детали и а так же механизма к которому принадлежит деталь, определить задачу детали в механизме и соответственно важнейшие свойства детали.
Пружина является неотъемлемой частью подвески автомобиля соответственно далее будет рассмотрено назначение подвески и режим ее работы. Совокупность устройств, связывающих колеса и кузов автомобиля, образует подвеску. Основное назначение подвески состоит в преобразовании воздействия на автомобиль со стороны дороги в допустимые колебания кузова и колес. Эти взаимодействия должны быть такими, чтобы автомобиль не только быстро набирал скорость (разгонялся), но и мог еще быстрее замедлять ход (вплоть до полной остановки). Кроме того, машина во время движения должна легко управляться и быть устойчивой. Для выполнения названных задач и служит подвеска, конструкция которой определяет основные эксплуатационные свойства легковых автомобилей, включая безопасность движения.
При движении автомобиля колеса перемещаются относительно кузова и дороги в вертикальном и горизонтальном направлениях, а также под углом (вращение вокруг оси, наклон относительно кузова и дороги, вращение вокруг оси поворота — оси шкворня). Для выполнения требований, связанных с эксплуатационными свойствами автомобиля, приходится существенно ограничивать перемещение колес. При поперечном (боковом) перемещении колес в горизонтальных направлениях изменяется колея, а при продольном — база автомобиля. Наличие таких перемещений приводит к увеличению сопротивления движению, износу шин, ухудшению устойчивости и управляемости. Вертикальные перемещения колес относительно кузова у легковых автомобилей могут превышать 20 см. Углы поворота колес составляют 30... 45°.
Для того чтобы автомобиль успешно разгонялся и тормозил, хорошо «держал» дорогу, необходимо иметь надежное сцепление колес с ее поверхностью. Влияет ли подвеска на сцепление? Безусловно. Сцепление зависит не только от характеристик протектора шин и качества дороги, но и от нагрузки, которая передается на колеса. Изменение вертикальной нагрузки на колеса определяется прогибом пружин и усилиями со стороны амортизаторов. При уменьшении вертикальной нагрузки снижается сцепление колес с поверхностью дороги.
Подвеска легкового автомобиля содержит следующие основные устройства: направляющие устройства (рычаги, стойки, тяги, растяжки), упругие элементы (листовые рессоры, пружины, пневморессоры и т.п.), гасящие устройства (гидравлические амортизаторы) и, наконец, устройства регулирования и управления (регуляторы высоты и крена, ЭВМ и т. д.).
Упругие устройства (упругие элементы) служат для уменьшения нагрузок, действующих между колесом и кузовом. При наезде на дорожные неровности происходят деформации упругих элементов. После проезда неровностей упругие элементы вызывают колебания кузова и колес. Основной характеристикой упругих элементов является жесткость, т.е. отношение вертикальной нагрузки к прогибу (или осадке пружины). Упругие элементы подвески колес различают не только по конструкции, но и в зависимости от того, из какого материала они сделаны. Если используются упругие свойства металла (сопротивление изгибу или кручению), то имеют место металлические упругие элементы.
Упругие элементы подвески.
С появлением передней назависимой подвески пружины получили самое широкое распространение. Наиболее просты витые пружины с постоянной толщиной проволоки и неизменным шагом навивки. Такие пружины обеспечивают подвеске необходимый ход колес и малую жесткость.
Однако мягкие пружины не позволяют обеспечить подвеске защиту от ударов и толчков в конце хода колес вверх (сжатие) и вниз (отбой). Как правило, необходимо ужесточение подвески с пружиной в конце хода сжатия и отбоя, которое достигается за счет установки дополнительных упругих элементов.
Винтовая пружина (ее витки навиты по спирали) — наиболее распространенный тип упругого элемента подвески легкового автомобиля. Она воспринимает вес машины и снижает динамические воздействия, передаваемые на кузов от поверхности дороги при движении. Как правило, пружина работает на сжатие, уменьшая свою высоту при увеличении нагрузки. Для этого между ее витками при изготовлении оставляют зазоры, называемые шагом навивки. После снятия нагрузки пружина возвращается в исходное положение. Ее способность сопротивляться деформации называют жесткостью. Несмотря на простоту и надежность, со временем они выходят из строя. После длительной эксплуатации пружины проседают из-за усталости металла, при этом ход и энергоемкость подвески уменьшаются. Она начинает отрабатывать до упора, что приводит к разрушению деталей кузова.
Наиболее значимыми характеристиками пружин используемых в подвеске автомобиля являются их жесткость и постоянство упругих свойств во времени (количество циклов нагружения) Практика показывает, что во многих случаях пружины, изготовленные по принятой технологии и из качественной проволоки, выдержавшей установленные испытания, в условиях эксплуатации преждевременно теряют упругие свойства или быстро разрушаются, особенно пружины, работающие в динамических условиях. Это свидетельствует о наличии недостатков в технологиях производства пружин и о необходимости разработки способов повышения их несущей способности и постоянства упругих свойств во времени. Существенное влияние на усталостную прочность пружин оказывает качество поверхностного слоя проволоки.Поломки пружин вследствие усталости или потеря рабочих характеристик из-за релаксации напряжений приводят к выходу из строя узлов или всей машины в целом.
Большое влияние на формирование качества поверхностного слоя детали и, в связи с этим, на их эксплуатационные свойства, оказывает технология производства, а в особенности операции окончательной обработки.
Проблема повышения работоспособности пружин комплексная, состоящая из оптимальных конструктивных решений и применения технологических методов, обеспечивающих высокие эксплутационные свойства в конкретных условиях работы машин.
В нашем случае следует перейти от характеристик пружины как готового изделия к требованиям которые предъявляться к материалам из которых изготавливаются пружины. Нам удалось выяснить что наиболее важной и критичной характеристикой пружины является количество циклов нагружения которое пружина выдержит без «проседания» т.е. величина ее усталостной прочности, в свою очередь эта характеристика напрямую зависит от качества материала пружины и качества ее поверхности. Среди комплекса свойств которыми обладает пружинно-рессорная сталь выделим те, которые связанны с величиной усталостной прочности: предел текучести σ 0.2; предел выносливости σ -1; модуль сдвига G; плотность материала ρ.
Выбор и обоснование материала и технологии обработки наиболее полно отвечающего комплексу выявленных свойств при помощи функции желательности. Последовательность изготовления пружин выглядит следующим образом.
1. Получение проволоки.
2. Подготовка поверхности заготовки к предварительной обработке.
3. Предварительная обработка проволоки:
- волочение.
4. Окончательная обработка проволоки:
- шлифование абразивной лентой;
5. Термическая обработка проволоки.
6. Навивка пружин (холодная или горячая).
7. Термическая обработка пружин.
8. Дробеструйная обработка пружин.
9. Нанесение защитного покрытия на пружины.
10. Контроль пружин.
Работа пружин, рессор и тому подобных деталей характеризуется тем, что в них используют только упругие свойства стали. Большая суммарная величина упругой деформации пружины (рессоры и т. д.) определяется ее конструкцией — числом и диаметром витков, длиной пружины. Поскольку возникновение пластической деформации в пружинах не допускается, то от материала подобных изделий не требуется высокой ударной вязкости и высокой пластичности. Главное требование состоит в том, чтобы сталь имела высокий предел упругости (текучести). Это достигается закалкой с последующим отпуском при температуре в районе 300—400° С. При такой температуре отпуска предел упругости (текучести) получает наиболее высокое значение, а то, что эта температура лежит в интервале развития отпускной хрупкости I рода, в силу отмеченного выше обстоятельства не имеет большого значения.
Пружины, рессоры и подобные им детали изготавливают из конструкционных сталей с повышенным содержанием углерода (но, как правило, все же более низким, чем у инструментальных сталей) — приблизительно в пределах 0,5—0,7% С, часто с добавками марганца и кремния. Для особо ответственных пружин применяют сталь 50ХФ, содержащую хром и ванадий и обладающую наиболее высокими упругими свойствами. Термическая обработка пружин и рессор из легированных сталей заключается в закалке от 800—850° С (в зависимости от марки стали) в масле или в воде с последующим отпуском в районе 400—500° С на твердость НКС 35—45. Это соответствует ств= 1304-160 кгс/мм2.
Лучшими заданными свойствами обладают несколько сталей этой группы — стали 65Г, 60С2, 50ХФА, они подвергаются стандартной термической обработке закалке и высокому отпуску, соответствующие свойства которых взяты из справочной литературы (табл. 3.2).
Таблица 3.2
Свойства пружинных сталей
Сталь
| σ 0.2 ,МПа
| G ,ГПа
| ρ, кг/мЗ
| σ -1 ,МПа
| 65Г
|
|
|
|
| 60С2
|
|
|
|
| 50ХФА
|
|
|
|
|
Выбор оптимальной марки стали внутри этой группы неочевиден, поскольку сталь 65Г обладает лучшим пределом выносливости, сталь 60С2 — лучшая по пределу текучести и плотности, а сталь 50ХФА — лучшая по величине модуля сдвига.
Для оптимального выбора стали используем обобщенную функцию желательности. При вычислении функции Харрингтона необходимо вначале задать граничные значения свойств, а затем провести кодирование свойств.
В табл. 3.3 приведены граничные значения свойств в соответствии с требованиями, предъявляемыми к пружинам.
Таблица 3.3
Граничные значения свойств
Свойство
| Верхняя граница, у' = 3
| Нижняя граница у'=0
| Предел текучести σ 0.2 МПа
|
|
| Модуль сдвига G, ГПа
|
|
| Плотность ρ, кг/мЗ
|
|
| Предел выносливости σ -1 ,МПа
|
|
|
Значения кодированных свойств и рассчитанные по формулам частные и обобщенные функции желательности приведены в табл. 3.4, Проведенный анализ показал, что лучшим комплексом свойств обладает сталь 50ХФА.
Следует отметить, что выбор этой стали позволяет также существенно снизить материалоемкость изделия.
Для данного изделия целесообразно применить стандартную термообработку, необходимо провести последующую дробеструйную обработку и нанесение полимерного покрытия т.к. изделие эксплуатируется при атмосферных и абразивных воздействиях.
Таблица 3.4
Частные и обобщенные функции желательности выбранной группы сталей
|