Обратная связь
|
МАТЕРИАЛЫ С ОСОБЫМИ ТЕХНОЛОГИЧЕСКИМИ СВОЙСТВАМИ Студент должен
Знать:
· Стали с улучшенной обрабатываемостью резанием;
· Железоуглеродистые стали с высокими литейными свойствами;
· Свойства и классификацию меди и медных сплавов
Уметь:
· Расшифровывать марки латуней и бронз;
· Расшифровывать марки медных сплавов
Автоматные стали (ГОСТ 1414—75) содержат 0,08...0,45 % углерода и повышенное содержание серы (0,05—0,3 %), фосфора (0,05...0,16 %) и часто марганца (0,6 ... 1,55 %). Обогащение границ зерен феррита растворенным в нем фосфором и образование хрупких включений (MnS и др.) на границах зерен сталей облегчают резание, способствуют дроблению и легкому отделению стружки, обеспечивая чистоту обрабатываемой поверхности. Срок службы режущего инструмента при обработке автоматных сталей увеличивается. Улучшение обрабатываемости стали достигается также микролегированием свинцом, селеном, кальцием. Однако введение этих элементов снижает прочностные характеристики сталей, поэтому их применяют для изготовления малоответственных деталей, от которых не требуется высоких механических свойств.
Автоматные стали получили свое наименование в связи с их обработкой на станках-автоматах с повышенной скоростью резания для изготовления деталей массового спроса (шайбы, болты, гайки, шпильки и некоторые другие детали автомобилестроения). В обозначении марки первая буква А указывает, что сталь автоматная; цифры в ней показывают содержание углерода в сотых долях процента (например, А11, А40Г). Присутствие свинца обозначает буква С (например, АС35Г2), кальция — буква Ц (АЦ45Х, АЦ40Г2 и др.), селена — буква Е (А35Е, А40ХЕ и др.).
Литейные стали содержат до 0,9 % Мп, до 0,52 % Si и не более 0,06 % S и 0,08 % Р. При твердении отливок формируются крупные зерна аустенита, внутри которых при последующем охлаждении в сталях с содержанием углерода менее 0,4 % образуются направленные пластины избыточного феррита (видманштеттова структура). С увеличением содержания углерода доля феррита, образующего видманштеттову структуру, уменьшается, а доля феррита в виде равноосных зерен возрастает. Литая сталь с видманштеттовой структурой имеет низкие пластичность и ударную вязкость, и для повышения величин этих свойств отливки из сталей, содержащих менее 0,4%. С, подвергают полному отжигу или нормализации.
Литейные свойства сталей значительно хуже, чем чугунов и большинства литейных цветных сплавов. Трудности при литье создают высокая температура плавления, низкая жидкотекучесть. большая линейная усадка (до 2,3 %) и склонность к образованию горячих литейных трещин.
Низкоуглеродистые литейные стали применяют для изготовления деталей, подвергающихся ударным нагрузкам; арматуры; деталей сварно-литых конструкции. Среднеуглеродистые литейные стали применяют для отливки станин и валков прокатных станов, крупных шестерен, зубчатых колес. Стальные отливки часто подвергают термической обработке для уменьшения литейных напряжений.
Литейные легированные стали по свойствам уступают углеродистым сталям из-за того, что при легировании расширяется интервал кристаллизации и уменьшается теплопроводность и, следовательно, возрастают термические напряжения. Литейные легированные стали подразделяют на конструкционные (ГОСТ 977-88) и высоколегированные со специальными свойствами.
Многие литейные стали имеют ту же марку, что и деформируемые, отличаясь лишь буквой Л в конце марки (15Л, 20Л, 25Л, ЗОЛ, 35Л, 40Л, 45Л, 50Л и 35ХМЛ, 35ХГСЛ, 12Х18Н9ТЛ и др.). В этом случае химический состав литейной стали практически такой же, как деформируемой, и отличается лишь допустимым количеством вредных примесей (в литейной стали оно несколько больше). Однако немало легированных сталей разработано специально в качестве литейных и не имеют аналога среди деформируемых (например, сталь 20ФЛ, применяемая для отливки крупногабаритных деталей грузовых вагонов, и сталь 08ГДНФЛ — для изготовления ответственных крупных деталей в судостроении, работающих до - 60 °С
МЕДЬ И МЕДНЫЕ СПЛАВЫ
Получение меди и ее сплавов. В настоящее время медь получают из сульфидных руд, содержащих медный колчедан (CuFeS2). Обогащенный концентрат медных руд (содержащий 11 — 35% Сu), сначала обжигают для снижения содержания серы, а затем плавят на медный штейн. Цель плавки на штейн — отделение сернистых соединений меди и железа от рудных примесей. Чистая медь имеет 11 марок (М00б, М0б, Mlб, Mlу, MI. Mlр. М1ф, М2р, МЗр, М2 и МЗ).
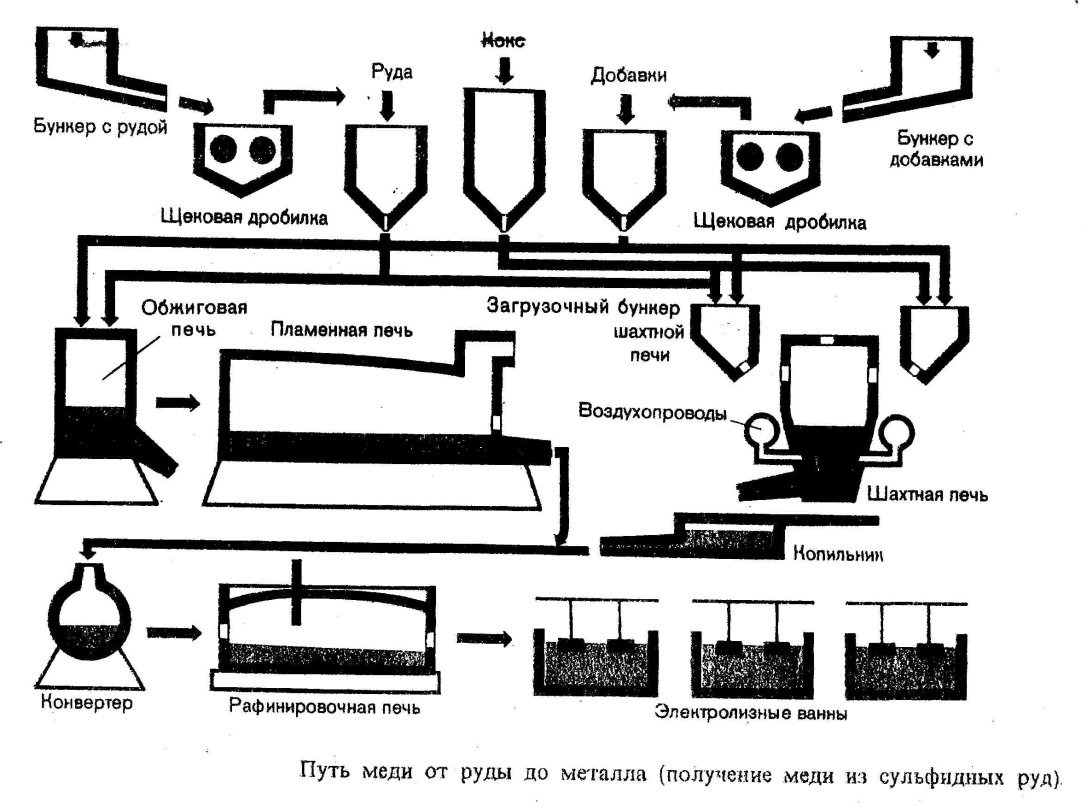
Рис. 2.14 Путь меди и руды до металла (получение меди из сульфидных руд)

Рис. 2.15 Выплавка меди
Механические свойства чистой отожженной меди: σв=220—240 МПа, НВ 40—50, δ = 45-50%. Чистую медь применяют для электротехнических целей и поставляют в виде полуфабрикатов — проволоки, прутков, лент, листов, полос и труб. Из-за малой механической прочности чистую медь не используют как конструкционный материал, а применяют ее сплавы с цинком, оловом, алюминием, кремнием, марганцем, свинцом. Легирование меди обеспечивает повышение ее механических, технологических и эксплуатационных свойств. Различают три группы медных сплавов: латуни, бронзы, сплавы меди с никелем.
Медно-никелевыминазывают сплавы на основе меди, в которых легирующим элементом является никель.
Медь с никелем образует непрерывный ряд твердых растворов. Добавка никеля к меди увеличивает твердость, прочность и электросопротивление, уменьшает термический коэффициент электросопротивления и повышает коррозионную стойкость во многих средах.
Медно-никелевые сплавы выделены в особую группу (ГОСТ 492—73). По направлению использования их делят на:
· конструкционные (мельхиор, нейзильбер, куниаль
· электротехнические (копель, константан, манганин) сплавы.
Медно-никелевые сплавы маркируют буквами МН и цифрой, указывающей суммарное содержание Ni+Co.
Например, МН19 — медно-никелевый сплав, содержащий 19% (Ni+Co), остальное — медь. Если сплав легируется, в марке указывают введенные элементы и их содержание через дефисы в порядке их упоминания.
Мельхиор —сплав Сu (основа), главным образом, с Ni (5...30 %). На пример мельхиоры (МН19 и МНЖМц30-0,8-1) — однофазные сплавы из α твердого раствора серебристого цвета; σв = 350...400 МПа. Они обладают высокой коррозионной и кавитационной стойкостью на воздухе и в воде, хорошей обрабатываемостью. Из мельхиоров изготавливают конденсаторные трубы в морском судостроении, трубы термостатов, медицинский инструмент, детали точной механики, химической аппаратуры, монеты, изделия массового потребления.
Нейзильбер — сплав Сu (основа) с Ni (5...35%) и Zn (13...45%). Обладает высокими коррозионной стойкостью и прочностью; при повышении со держания Ni нейзильбер приобретает красивый белый цвет с зеленоватым или синеватым отливом.
Нейзильбер МНЦ15-20 — однофазный сплав α - гвердого раствора Ni + + Zn + Со в меди; σв = 500...700 МПа. Обладает высокими коррозионной стойкостью и упругостью, хорошей полируемостью; хорошо обрабатывается давлением в холодном состоянии. Применяется в электротехнике (плоские пружины, реле, проволока для термопар и реостатов), автомобиле строении (игольчатые клапаны карбюраторов). Из него изготавливают приборы точной механики, плоские пружины реле, медицинский инструмент, паровую и водяную арматуру, художественные изделия, монеты.
Куниаль — сплав Сu (основа) с Ni (4...20 %) и Al (1...4 %). Обладает высокой коррозионной стойкостью в атмосферных условиях, пресной и морской воде; по прочности не уступает некоторым конструкционным сталям. Куниаль А (МНА13-3) применяется для изготовления деталей машин повышенной прочности; куниаль Б (МНА 6-1,5) — для изготовления пружин и других изделий электротехнической промышленности.
Копель — сплав Сu (основа) с Ni (43 %) и Мn (≈ 0,5 %), константан — сплав Сu (основа) с Ni (* 40 %) и Мп (» 1,5 %), а также манганин — сплав Си (основа) с Мn (11...13,5 %) и Ni (2,5...3,5 %), относятся к сплавам с высоким удельным электрическим сопротивлением, мало зависящим от температуры. Рабочая температура копеля до ≈ 600 °С, константана — ≈ 500 °С, а манганина — в интервале 15...35°С. Копель (например, МНМц43-0,5) и константан (например, МНМц40-1,5) идут на производство проволоки для измерительных и нагревательных приборов, термопар, компенсационных проводов, точных резисторов. Манганин (МНМц 3-12) характеризуется сочетанием низкого термического коэффициента электросопротивления и очень малой термо-ЭДС в паре с медью, что обусловливает его применение в электротехнических измерительных приборах и резисторах.
Латуни. Латунями называют двойные или многокомпонентные сплавы на основе меди, в которых основным легирующим элементом является цинк. При введении других элементов (кроме цинка) латуни называют специальными по наименованию элементов, например железофосфорномарганцевая латунь и т. п.
В сравнении с медью латуни обладают большей прочностью, коррозионной стойкостью и лучшей обрабатываемостью (резанием, литьем, давлением). Латуни содержат до 40—45% цинка. При большем содержании цинка снижается прочность латуни и увеличивается ее хрупкость. Содержание легирующих элементов в специальных латунях не превышает 7—9%.
Сплав обозначают начальной буквой Л —латунь. Затем следуют первые буквы основных элементов образующих сплавов: Ц — цинк, О — олово, Мц — марганец, Ж — железо, Ф — фосфор, Б —- бериллий и т. д. Цифры, следующие за буквами, указывают на количество легирующего элемента в процентах.
Расшифровка: ЛАЖМц66-6-3-2 алюминиевожелезомарганцовистая латунь, содержащая 66% меди, 6% алюминия, 3% железа, и 2% марганца, остальное цинк.
По технологическому признаку латуни, как и все сплавы цветных металлов, подразделяют на литейные и деформируемые. Литейные латуни (ГОСТ 17711—72) предназначены для изготовления фасонных отливок, их поставляют в виде чушек.
Деформируемые латуни выпускают (ГОСТ 15527—70) в виде простых латуней, например Л90 (томпак), Л80 (полутомпак), и сложных латуней, например ЛАЖ60-1-1, ЛС63-3 и др. Латуни поставляют в виде полуфабрикатов — проволоки, прутков, лент, полос, листов, труб и других видов прокатных и прессованных изделий. Латуни широко применяют в общем и химическом машиностроении.
Бронзы. Сплавы меди с оловом, алюминием, кремнием, марганцем, свинцом, бериллием называют бронзами. В зависимости от введенного элемента бронзы называют оловянными, алюминиевыми и т. д.
Бронзы обладают высокой стойкостью против коррозии, хорошими литейными и высокими антифрикционными свойствами и обрабатываемостью резанием. Для повышения механических характеристик и придания особых свойств бронзы легируют железом, никелем, титаном, цинком, фосфором. Введение марганца способствует повышению коррозионной стойкости, никеля — пластичности, железа — прочности, цинка — улучшению литейных свойств, свинца — улучшению обрабатываемости.
Бронзы маркируют буквами Бр, правее ставят элементы, входящие в бронзу: О — олово, Ц — цинк, С — свинец, А — алюминий, Ж — железо, Мц — марганец и др. Затем ставят цифры, обозначающие среднее содержание элементов в процентах (цифру, обозначающую содержание меди в бронзе, не ставят).
Расшифровка: марка БрОЦС5-5-5 означает, что бронза содержит олова, свинца и цинка по 5%, остальное — медь (85%).
Оловянные бронзы содержат в среднем 4—6% олова, имеют высокие механические (σв=150—350МПа; δ = 3—5%; твердость НВ60—-90), антифрикционные и антикоррозионные свойства; хорошо отливаются и обрабатываются резанием. Для улучшения качества в оловянные бронзы вводят свинец, повышающий антифрикционные свойства и обрабатываемость; цинк, улучшающий литейные свойства; фосфор, повышающий литейные, механические и антифрикционные свойства.
Различают деформируемые и литейные оловянные бронзы. Деформируемые бронзы (ГОСТ 5017—74) поставляются в виде полуфаб-рикатов (прутки, проволоки, ленты, полосы) нагартованном (твердом) и отожженном (мягком) состояниях. Эти бронзы применяют для вкладышей подшипников, втулок деталей приборов и т. п. Литейные оловянные бронзы содержат большее количество олова (до 15%). цинка (4— 10%), свинца (3—6%), фосфора (0,4—1,0%). Литейные бронзы (ГОСТ 614—73) применяют для получения различных фасонных отливок. Высокая стоимость и дефицитность олова — основ ной недостаток оловянных бронз.
Безоловянные бронзы содержат алюминий, железо, марганец, бериллий, кремний, свинец или различное сочетание этих элементов. Алюминиевые бронзы содержат 4—11% алюминия. Алюминиевые бронзы имеют высокую коррозионную стойкость, хорошие механические и технологические свойства. Эти бронзы хорошо обрабатываются давлением в горячем состоянии, а при содержании алюминия до 8% — и в холодном состоянии. Бронзы, содержащие 9—11% алюминия, а также железо, никель, марганец, упрочняются термической обработкой (закалка и отпуск). Наиболее поддающаяся закалке БрАЖН10-4-4 после закалки (980°С) и отпуска (400°) повышает твердость с НВ 170—200 до НВ400.
Марганцовистые бронзы (БрМИ5) имеют сравнительно невысокие механические свойства, но обладают хорошей сопротивляемостью коррозии и высокой пластичностью, а также сохраняют механические свойства при повышенных температурах.
Свинцовистые бронзы (БрСЗО) отличаются высокими антикоррозионными ми и теплопроводностью (в четыре раза большей, чем у оловянных бронз), применяют для высоконагруженных подшипников с большими ными давлениями.
Бериллиевые бронзы (БрБ2) после термообработки имеют высокие механические свойства, например у БрБ2 σв=1250МПа, НВ 350, высокий предел упругости, хорошая коррозионная стойкость, теплостойкость. Из бериллиевых бронз изготовляют детали особо ответственного назначения.
Кремнистые бронзы (БрКН1-З, БрКМц3-10) применяют как заменители дорогостоящих бериллиевых бронз.
Схема для закрепления пройденного материала
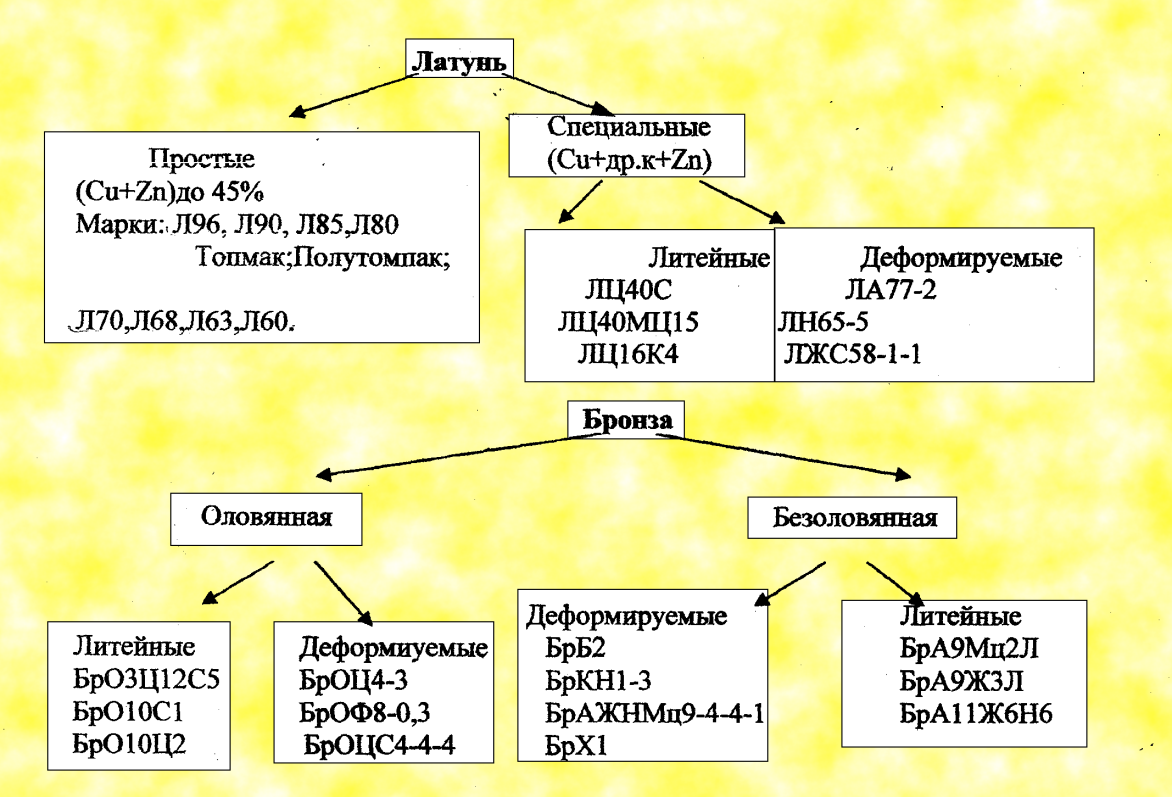
Рис. 2.16 Схема медных сплавов
Латунь– это сплав меди и цинка
Бронза – это сплав меди с другими компонентами
Свойствакрасновато-желтый цвет, удельный вес 8,9 гр/см3, t= 1083,обладает электро и теплопроводимостью, используется в электропромьшшенности и электротехнике.
ПРАКТИЧЕСКАЯ РАБОТА №4
«Расшифровка марок латуней и бронз, их применение»
Цель работы:Закрепить теоретические знания, полученные на уроке, приобрести навыки работы со справочной литературой, научиться расшифровывать марки медных сплавов.
Задание:
1. Изучить свойства и применение медных сплавов и расшифровать марки латуней и бронз.
Для специальности 151001, 050501
(190604) Для специальности 160203
Л96
| БрОЗЦ12С5
| Л96
| БрОФ7-0,2
| Л68
| БрА7
| Л62
| БрОФЮ-1
| ЛА77-2
| БрБ2
| ЛС59-1
| БрАЖМц 10-3-1, 5
| ЛО60-1
| БрКН1-3
| Л062-1
| БрАЖН 10-4-4
| ЛАКНМц 72-2-2,5-0,5-0,5
|
| ЛАЖ60-1-1Л
| БрБ2
| ЛЦ23А6ЖЗМц2
|
| БрКН 1-3
|
| БрОФ 7-0,2
|
| БрСЗО
|
| БрОЦ 4-3
|
| БрОС 5-25
|
| БрХ1
|
|
|
|
|
|
|
|
2. Результаты занести в таблицу.
№ п/п
| Марка сплава
| Расшифровка марки сплава
| Свойства
| Применение
|
|
|
|
|
|
|
|
|
|
|
|
|
|
|
|
3. Сделать вывод.
Ответить на вопросы:
1. Перечислите основные свойства меди.
2. Что такое латунь, бронза?
3. Классификация латуней и бронз.
ИЗНОСОСТОЙКИЕ МАТЕРИАЛЫ
НЕРЖАВЕЮЩИЕ СТАЛИ
Студент должен
Знать:
· классификацию видов изнашивания;
· антифрикционные материалы
Уметь:
· расшифровывать марки износостойких материалов
Нержавеющими называются стали, обладающие высоким сопротивлением коррозии при воздействии атмосферы воздуха, воды, растворов кислот, солей и многих других реагентов.
Углеродистые, а также мало- и среднелегированные стали отличаются низкой коррозионной стойкостью.
Легирование стали большим' количеством хрома или хрома и никеля сообщает ей высокое сопротивление коррозии.
Различают нержавеющие хромистые и хромоникелевые стали.
Высокая коррозийная стойкость нержавеющей хромистой стали объясняется тем, что на ее поверхности образуется очень тонкая, но прочная и непроницаемая окисная пленка Сr2О3, которая обладает высокими защитными свойствами. Высокая коррозионная стойкость нержавеющей хромоникелевой стали объясняется еще и однородной аустснитной структурой, которая получается благодаря высокому содержанию встали хрома и никеля.
Хромистые нержавеющие сталидолжны содержать не менее 12% хрома. Только в этом случае они будут обладать высокой коррозионной стойкостью. Свойства хромистой нержавеющей стали зависят от содержания в ней углерода. По мере увеличения в ней содержания углерода в большой степени возрастает закаливаемость и твердость стали. Закалка и отпуск сообщают хромистым нержавеющим сталям наилучшие механические свойства. Однако в связи с тем, что при отпуске выделяются карбиды хрома, однородность структуры и ее коррозионная стойкость снижаются. Поэтому наивысшую коррозионную стойкость, хромистые нержавеющие стали приобретают после закалки и последующей полировки.
Эти стали обладают высокой коррозионной стойкостью в атмосферных условиях, в речной воде и удовлетворительной стойкостью в азотной кислоте при комнатной температуре. Соляная и серная кислоты разрушают хромистые нержавеющие стали. Кроме того, эти стали не окисляются на воздухе до 700° С.
Стали: Х13 (ЭЖ1), 3Х13(ЭЖ3), Х18(ЭИ229), 0Х17Т (ЭИ645), Х17Н2(ЭИ268).
Хромоникелевые нержавеющие стали.Благодаря высокому содержанию хрома и никеля свойства этих сталей по сравнению свойствами хромистых нержавеющих сталей значительно улучшилось: повысились механические свойства, увеличилась коррозионная стойкость и стойкость в кислотах. Это стали аустенитного класса. Они нашли широкое применение в авиационной промышленности. Для получения аустенита сталь закаливают с 1100° С в воде. Высокая температура нагрева при закалке необходима для растворения карбидов и получения однофазной структуры .
Аустенитные хромоникелевые стали в закаленном состоянии, кроме высокой коррозионной стойкости, имеют хорошие технологические свойства. Они обладают высокой пластичностью, в холодном состоянии, хорошо поддаются прокатке, штамповке и волочению. Эти стали хорошо свариваются всеми видами сварки.
Сталь Х18Н9(ЭЯ1), 0Х18Н9(ЭЯО), Х18Н9(ЭЯ1), 2Х1ЗН4Г9(ЭИ100), Х18Н9Т(ЭЯ1Т), 0Х18Н12Б(ЭИ402) .
Дополнительное легирование этих сталей небольшим количеством бора (0,01%) повышает их предел длительной прочности. Разработана новая группа нержавеющих сталей, обладающих при работе до температур 400—450° С прочностью, превосходящей прочность нержавеющих сталей аусте-ного и мартенситного классов. Эти стали переходного аустенитно - мартенситного или полуаустенитного класса нашли применение в конструкции высокоскоростных летательных аппаратов, подвергающихся аэродинамическому нагреву.
После закалки или нормализации этих сталей получается структура, как и у сталей аустенитного класса.
Сталь Х15Н9Ю(ЭИ904) является сталью полуаустенитного класса. Химический состав ее подобрано так, что мартенситная точка находится около нуля градусов. После нормализации с температуры 1000°С она приобретает структуру нестабильного аустенита. В этом состоянии она обладает наибольшей пластичностью и легко, обрабатывается давлением.
Шарикоподшипниковые стали
(ШХ6, ШХ9, ШХ15) применяют для изготовления шариков и роликов подшипников. По химическому составу (ГОСТ 801—60) и структуре эти стали относятся к классу инструментальных сталей. Они содержат около 1% Сu 0,6—1,5% Сr Для деталей размером до 10 мм применяют сталь ШХ6 (1,05—1,15% С и 0,4—0,7% Сr), а для деталей размером более 18 мм — сталь ШХ15 (0,95—1,05% С и 1,3—1,65% Сr). Термическая обработка шарикоподшипниковых сталей с небольшим содержанием хрома заключается и закалке и низком отпуске (до 200°С), в результате чего обеспечивается твердость HВ 600—660.
Графитизированную сталь (высокоуглеродистую, содержащую 1,5—2% С и до 2% Сr) используют для изготовления поршневых колец, поршней, коленчатых валов и других фасонных отливок, работающих в условиях трения. Графитизированная сталь содержит в структуре ферритоцементитную смесь и графит. Количество графита может значительно меняться в зависимости от режима термической обработки и содержания углерода. Графитизированная сталь после закалки сочетает свойства закаленной стали и серого чугуна. Графит в такой стали играет роль смазки.
Высокомарганцовистую сталь Г13Л, содержащую 1,2% С и 13% Мn, применяют для изготовления железнодорожных крестовин, звеньев гусениц и т. п. Эта сталь обладает максимальной износостойкостью, когда имеет однофазную структуру аустенита, что обеспечивается закалкой (1000-1100°С) при охлаждении на воздухе. Охлажденная сталь имеет низкую твердость (НВ 200), после закаленного наклепа ее твердость повышается до НВ 600.
Антифрикционные сплавы
Антифрикционные сплавы предназначены для повышения долговечности трущихся поверхностей машин и механизмов. Трение происходит в подшипниках скольжения между валом и вкладышем подшипника. Поэтому для вкладыша подшипника подбирают такой материал, который предохраняет вал от износа, сам минимально изнашивается, создает условия для оптимальной смазки и уменьшает коэффициент трения. Исходя из этих требований, антифрикционный материал представляет собой сочетания достаточно прочной и пластичной основы, в которой имеются опорные (твердые) включения. При трении пластичная основа частично изнашивается, а вал опирается на твердые включения. В этом случае трение происходит не по всей поверхности подшипника, а смазка удерживается в изнашивающихся местах пластичной основы.
Антифрикционными сплавами служат сплавы на основе олова, свинца, меди или алюминия, обладающие специальными антифрикционными свойствами. Антифрикционные свойства сплавов проявляются при трении в подшипниках скольжения. Это, в первую очередь, низкий коэффициент трения, хорошая прирабатываемость к сопрягаемой детали, высокая теплопроводность, способность удерживать смазку и др. Из антифрикционных сплавов наиболее широко применяют баббит, бронзу, алюминиевые сплавы, чугун и металлокерамические материалы.
Антифрикционные сплавы хорошо прирабатываются в парах трения благодаря мягкой основе — олову, свинцу или алюминию. Более твердые металлы (цинк, медь, сурьма), вкрапленные в мягкую основу, способны выдерживать большие нагрузки. После приработки и частичной деформации мягкой основы в ней образуются углубления, способные удерживать смазку, необходимую для нормальной работы пары.
Баббиты — антифрикционные материалы на основе олова или свинца. Их применяют для заливки вкладышей подшипников скольжения, работающих при больших окружных скоростях и при переменных и ударных нагрузках. По химическому составу баббиты классифицируют на три группы: оловянные (Б83, Б88). оловянно-свинцовые (БС6. Б16) и свинцовые (БК2, БКА). Последние не имеют в своем составе олова.
Лучшими антифрикционными свойствами обладают оловянные баббиты. Микроструктура оловянносурьмяномедного баббита Б83 состоит из мягкой основы, представляющей собой твердый раствор на базе олова.
Баббиты на основе свинца имеют несколько худшие антифрикционные свойства, чем оловянные, но они дешевле и менее дефицитны. Свинцовые баббиты применяют в подшипниках, работающих в легких условиях. В марках баббитов цифра показывает содержание олова.
Расшифровка: БС6 содержит по 6% олова и сурьмы, остальное — свинец.
Для оловянных и оловянно-фосфористых бронз характерны высокие антифрикционные свойства: низкий коэффициент трения, небольшой износ, высокая теплопроводность, что позволяет подшипникам, изготовленным из этих материалов, работать при высоких окружных скоростях и нагрузках.
Алюминиевые бронзы, используемые в качестве подшипниковых сплавов, отличаются большой износостойкостью, но могут вызвать повышенный износ вала. Их применяют вместо оловянных и свинцовых баббитов и свинцовых бронз.
Свинцовые бронзы в качестве подшипниковых сплавов могут работать в условиях ударной нагрузки.
Латуни по антифрикционным свойствам уступают бронзам. Их используют для подшипников, работающих при малых скоростях и умеренных нагрузках.
Из-за дефицитности олова и свинца применяют сплавы на менее дефицитной основе. Алюминиевые сплавы обладают хорошими антифрикционными свойствами, высокой теплопроводностью, хорошей коррозионной стойкостью в масляных средах и достаточно хорошими механическими и технологическими свойствами. Их применяют в виде тонкого слоя, нанесенного на стальное основание, т. е. в виде биметаллического материала. В зависимости от химического состава различают две группы сплавов.
1. Сплавы алюминия с сурьмой, медью и другими элементами, которые образуют твердые фазы в мягкой алюминиевой основе. Наибольшее распространение получил сплав АСМ, содержащий сурьму (до 6,5%) и магний (0,3— 0,7%). Этот сплав хорошо работает при высоких нагрузках и больших скоростях в условиях жидкостного трения, его широко применяют для изготовления вкладышей подшипников коленчатого вала двигателей тракторов и авто мобилей.
2. Сплавы алюминия с оловом и медью, например АО20-1 (20% олова и до 1,2% меди) А09-2 (9% олова и 2% меди). Они хорошо работают в условиях сухого и полужидкого трения и по антифрикционным свойствам близки к баббитам. Их используют для производства подшипников в автомобилестроении, транспортном общем машиностроении.
Для работы в подшипниковых узлах трения применяют специальные антифрикционные чугуны. Изготовляют три типа антифрикционного чугуна: серый с пластинчатым графитом, высокопрочный с шаровидным графитом и ковкий с хлопьевидным графитом. Антифрционный чугун идет на изготовление червячных зубчатых колес, направляющих для ползунов т. п. деталей машин, работающих в условиях трения.
ПРАКТИЧЕСКАЯ РАБОТА №5
|
|