Магнезиальные вяжущие вещества
Магнезиальные вяжущие вещества представляют собой тонкомолотые порошки, содержащие оксид магния и твердеющие при затворении водными растворами хлористого или сернокислого магния. Магнезиальные вяжущие вещества в зависимости от применяемого сырья разделяют на два вида: каустический магнезит и каустический доломит.
Каустический магнезит - порошок, состоящий в основном из оксида магния. Его получают обжигом горной породы магнезита MgCO3 - в шахтных или вращающихся печах при 700 - 800оС с последующим измельчением продукта обжига в тонкий порошок. При обжиге магнезит разлагается по реакции
О3 = MgO+СО2.
Готовое вяжущее упаковывают в стальные барабаны или бумажные мешки и направляют к месту применения. Из-за высокой гигроскопичности каустический магнезит не подлежит длительному хранению.
Каустический магнезит затворяют не водой, а водными растворами хлористого или сернокислого магния. Каустический магнезит твердеет сравнительно быстро. Схватывание его должно наступать не ранее 20 мин, а конец - не позднее 6 ч с момента затворения. Марки каустического магнезита - 400, 500 и 600.
Каустический доломит - порошок, состоящий из оксида магния и углекислого кальция, получаемый обжигом природного доломита СаMg(CО3)2 с последующим измельчением в порошок. В связи с содержанием инертного CaCO3 каустический доломит по качеству уступает каустическому магнезиту. Марки каустического доломита - 100, 150, 200 и 300.
Магнезиальные вяжущие вещества обладают способностью прочно сцепляться с древесными опилками, стружками и другими органическими заполнителями, которые в изделиях не подвергаются разложению и загниванию. Эти вяжущие применяют для изготовления теплоизоляционных материалов (фибролита и др.), устройства теплых и износостойких ксилолитовых полов, ступеней, плиток.
Жидкое стекло и кислотоупорный цемент
К воздушным вяжущим веществам относятся жидкое стекло и затворяемый им кислотоупорный цемент.
Жидкое стекло представляет собой натриевый Na2nSiO2 или калиевый силикат К2ОnSiO2 желтого цвета, который получают сплавлением в стекловаренных печах при температуре 1300 - 1400оC измельченного чистого кварцевого песка с содой Na2CO3 или поташем К2СО3. Образовавшиеся после быстрого охлаждения расплава прозрачные куски и глыбы синеватого, зеленоватого и желтоватого цвета под действием пара (в автоклаве) под давлением 0,4 - 0,6 МПа растворяются, превращаясь в вязкий раствор, обычно называемый жидким стеклом. На строительства жидкое стекло (преимущественно натриевое, как более дешевое) поступает с истинной плотностью 1,32 - 1,50 г/см3. Оно твердеет только на воздухе. Процесс твердения жидкого стекла значительно ускоряется за счет введения катализатора - кремнефтористого натрия Na2SiF6.
Жидкое стекло применяют для получения силикатных огнезащитных красок, предохранения естественных каменных материалов от выветривания, уплотнения (силикатизации) грунтов, а также для получения кислотоупорного цемента и жаростойкого бетона.
Кислотоупорный цемент - тонко измельченная смесь кварцевого песка и кремнефтористого натрия, затворенная жидким стеклом. Схватывание и твердение кислотоупорного цемента происходит при температуре не ниже 10оС, при этом начало схватывания должно наступать не ранее 30 мин, а конец - не позднее 6 ч с момента затворения. Кислотоупорный цемент неводостоек и сравнительно быстро разрушается от действия воды и слабых растворов кислот.
Растворы и бетоны, приготовленные на кислотоупорном цементе, обладают высокой стойкостью против действия ряда минеральных и органических кислот, но разрушаются в щелочах, а также в фосфорной, фтористоводородной и кремнефтористоводородной кислотах. Их применяют для футеровки химической аппаратуры, возведения резервуаров и других сооружений химической промышленности.
Гидравлическая известь
Гидравлическая известь - продукт умеренного обжига мергелистых известняков, содержащих 6 - 20% глинистых и тонкодисперсных песчаных примесей. Обжигают эти известняки в шахтных печах при 900 - 1100оС. При этой температуре углекислый кальций разлагается и часть оксида кальция соединяется с оксидами кремния и алюминия, которые содержатся в глине. В результате образуются силикаты и алюминаты кальция, придающие гидравлической извести способность твердеть в воде.
Гидравлическая известь, немного смоченная водой, полностью или частично гасится и рассыпается в порошок, а залитая достаточным количеством воды образует тесто, которое начав твердеть на воздухе, продолжает твердеть в воде, при этом физико-химические процессы воздушного твердения сочетаются с гидравлическими.
Негашенная гидравлическая известь представляет собой порошок. Прочность при сжатии гидравлической извести через 28 сут от 1,7 до 10 МПа.
Гидравлическую известь применяют для приготовления кладочных и штукатурных растворов, эксплуатируемых как в сухих, так и во влажных средах, а также для бетонов низких марок. Растворы и бетоны на гидравлической извести в первые сутки твердения необходимо защищать от воздействия воды, так как они легко размываются.
Гидравлическую известь следует хранить в сухих закрытых помещениях, а при перевозке предохранять от увлажнения.
Портландцемент
Портландцемент и его разновидности являются основными вяжущими веществами в современном строительстве. В Украине его производство составляет свыше 65% выпуска всех цементов.
Портландцементом называют гидравлическое вяжуее вещество, получаемое тонким помолом портландцементного клинкера с гипсом, а иногда и со специальными добавками.
Портландцементный клинкер - продукт обжига до спекания тонкодисперсной однородной сырьевой смеси, состоящей из известняка и глины и некоторых других материалов (мергеля, доменного шлака и пр.). При обжиге обеспечивается преимущественное содержание в клинкере высокоосновных силикатов кальция.
Для регулирования сроков схватывания портландцемента в клинкер при помоле вводят двуводный гипс в количестве 1,5 - 3,5% (по массе цемента в пересчете на SO3).
По составу различают портландцемент без добавок, портландцемент с минеральными добавками, шлакопортландцемент и др.
Исходным сырьем для производства портландцемента служат горные породы - мергели, известняковые (известняки, мел, ракушечник, известковый туф и др.) и глинистые горные породы. С известняком в состав цемента. вносится основной оксид CaO; с глиной - оксиды кремния, алюминия, железа; с мергелем - все необходимые оксиды.
В природе редко встречаются горные породы, химический состав которых обеспечивал бы получение после обжига портландцементного клинкера необходимого качества, поэтому сырьевую смесь составляют из двух или нескольких компонентов. Соотношение компонентов сырьевой смеси выбирают с таким расчетом, чтобы полученный при обжиге портландцементный клинкер имел следующий химический состав; 63 - 68% СаО; 4 - 8 % Al2О3; 19 - 24 %SiO2, 2 - 6% Fe2О3. Обычно сырьевая смесь состоит из 75 - 78% известняка и 25 - 22% глины.
Производство портландцемента состоит из следующих основных процессов: добычи сырья и подготовки сырьевой смеси, обжига смеси до спекания с получением клинкера, помола клинкера в тонкий порошок совместно с добавками.
В зависимости от свойства сырья и типа обжигательных печей сырье к производству готовят мокрым или сухим способом. При мокром способе компоненты измельчают и смешивают в присутствии воды, и смесь в виде жидкой массы (шлама) обжигают; при сухом способе сырьевые компоненты измельчают, смешивают и обжигают в сухом виде.
Производство портландцемента мокрым способом. Мягкие горные породы (глину и мел), применяемые в качестве сырьевых компонентов, предварительно дробят в валковых дробилках и измельчают в специальных бассейнах-болтушках в присутствии 36 - 42 % воды по массе. Суспензии глины и мела в заданных соотношениях поступают в шаровые мельницы для тонкого измельчения. Если в качестве известкового компонента применяют твердый известняк, то его подвергают двухстадийному дроблению на щековой и молотковой дробилках, а затем измельчают в шаровых мельницах совместно с глиняной суспензией, получаемой в болтушках.

Рис.1. Технологическая схема производства портландцемента мокрым способом
- приемный бункер для известняка; 1- дробилка для известняка;3 - вагонетка с глиной; 4 - дозатор для воды; 5 - бассейн-болтушка;6 - сырьевая мельница; 7 - шламбассейны; 8 - вращающаяся печь;9 - форсунка подачи топлива; 10 - склад клинкера; 11 - складгипсового камня; 12 - дробилка для гипсового камня; 13 - шароваямельница; 14 - силосы для цемента; 15 - вагоны с цементом)
Шаровая многокамерная мельница - стальной цилиндр длиной 8 - 15 и диаметром 1,8 - 3,5 м, внутренняя поверхность которого облицована стальными плитами. Мельница вращается на полых цапфах, через которые, с одной стороны, ее загружают, а с другой - разгружают. Смесь известняка, глины и воды проходит через все камеры мельницы и, измельчаясь под ударами стальных шаров и цилиндров, выходит из нее в виде сметанообразной массы - шлама.
Шлам перекачивают насосами в цилиндрические щламбассейны для корректировки его состава. При корректировке устанавливают химический состав шлама (в основном определяют содержание углекислого кальция) и в соответствии с полученными данными добавляют к нему строго определенное количество шлама другого состава (обогащенного или обедненного известняком). Скорректированный таким образом шлам перекачивают в шламбассейны для хранения. В этих бассейнах шлам постоянно перемешивают. По мере необходимости шлам насосами подают на обжиг.
Сырьевую смесь обжигают во вращающихся печах (рис.2), представляющих собой сварной цилиндр диаметром 4 - 5 и длиной 150 - 185 м, футерованный изнутри огнеупорным материалом. Печь расположена под небольшим уклоном к горизонту и медленно вращается вокруг своей оси. Питатели-дозаторы подают шлам в верхний конец печи. Вследствие вращения печи и наклона ее к горизонту обжигаемый материал перемещается к нижнему концу печи. Навстречу ему движутся горячие топочные газы, образовавшиеся при сгорании топлива (пылевидный уголь, мазут, газ), подаваемого через форсунку в нижней части печи.
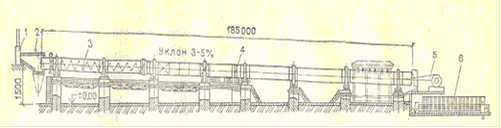
Рис.2. Вращающаяся печь для обжига цементного клинкера
- дымосос; 2 - питатель для подачи шлама; 3 - барабан; 4 - привод;5 - форсунка подачи топлива; 6 - холодильник)
Шлам омывается горячими газами и подсушивается, образуя комья. По мере продвижения материала при 500 - 750оС выгорают органические вещества и начинается дегидратация - выделение химически связанной воды из глинистой составляющей, сопровождаемая потерей пластичности и связующих свойств. Комья материала распадаются в подвижный порошок. При 750 - 800оС и выше в материале начинаются реакции в твердом состоянии между его составляющими. Их интенсивность возрастает с повышением температуры. Происходит сцепление отдельных частичек порошка и образование гранул разного размера. При прохождении зоны с температурой 900 - 1000оС происходит диссоциация карбонатов кальция с выделением оксида кальция и углекислого газа, который уносится с продуктами горения. Оксид кальция СаО вступает в химическое взаимодействие с глиноземом, оксидом железа и кремнеземом. Реакции химического связывания СаО протекают в твердом состоянии достаточно интенсивно при 1200 - 1250оС, при этом образуются следующие химические соединения: 2CaОSiO2 (двухкальциевый силикат), 3CaOAl2О3 (трехкальциевый алюминат) и 4СаОAl2О3Fе2О3 (четырехкальциевый алюмоферрит) . При температуре свыше 1300оС 3CaOАl2О3 и 4СаОAl2О3Fе2О3 переходят в расплав, в котором частично растворяются СаО и 2CaO SiO2 до насыщения раствора; в растворенном состоянии они реагируют между собой, образуя трехкальциевый силикат ЗСаО SiO2 - основной минерал портландцемента. Процесс образования трехкальциевого силиката, выделяющегося из жидкой фазы в виде кристаллов, способных расти, обычно происходит около 1450оC. При понижении температуры до 1300оС жидкая фаза застывает, процесс спекания заканчивается.
Клинкер - гранулы серовато-зеленого цвета размером 15 - 25 мм для охлаждения до 80 - 100оC направляют в холодильник, откуда он поступает на склад, где его выдерживают в течение 1 - 2 недель. В результате вылеживания содержащийся в клинкере в небольшом количестве свободный оксид кальция гасится влагой воздуха, а также уменьшается твердость зерен клинкера, что, в свою очередь, облегчает его помол и обеспечивает равномерность изменения объема цемента при твердении.
Клинкер измельчают в многокамерных шаровых мельницах. В процессе помола к нему добавляют 2 - 5 % гипсового камня для регулирования сроков схватывания портландцемента и различные, предусмотренные технологическим процессом, добавки. Из шаровых мельниц портландцемент пневмотранспортом подают в силосы - железобетонные башни цилиндрической формы емкостью до 6000 т каждая, где цемент перед отправкой потребителю выдерживается в течение 10 - 14 сут. За это время нагретый при помоле цемент охлаждается и оставшаяся в нем свободная известь гасится, что улучшает свойства цемента. Из силосов цемент поступает в упаковочные машины для расфасовки в многослойные бумажные мешки по 50 кг или направляется в специально оборудованные средства железнодорожного, автомобильного или водного транспорта.
Сухой способ производства портландцемента применяют в том случае, когда сырьевыми материалами являются мергели или смеси твердых известняков и глин влажностью 8 - 10 %. По этому способу сырьевые материалы после предварительного дробления и сушки совместно измельчают в шаровых мельницах. Сухую сырьевую муку с остаточной влажностью 1 - 2% гранулируют в зерна размером 20 - 40 мм или формуют, добавляя молотый на механических прессах уголь в брикеты.
Гранулы обжигают в циклонных теплообменниках, конвейерных кальцинаторах, вращающихся печах, а брикеты - в шахтных. Дальнейшие производственные операции осуществляют в той же последовательности, что и при мокром способе.
При сухом способе на обжиг клинкера расходуется значительно меньше топлива, чем при мокром.
Наряду с рассмотренными выше основными способами производства в последнее время применяют комбинированный способ, совмещающий достоинства мокрого и сухого способов. Сущность его заключается в том, что сырьевую смесь подготовляют по мокрому способу, после чего шлам обезвоживают на специальных установках и в виде гранул, как и при сухом способе, обжигают во вращающихся печах.
Минералогический состав клинкера. Клинкер состоит из следующих основных клинкерных минералов: трехкальциевого силиката ЗСаОSiO2 (алит), двухкальциевого силиката 2СаО . SiO2 (белит), трехкальциевого алюмината 3СаО. Аl2О3, четырехкальциевого алюмоферрита 4CaOАl2О3 Fe2O3. Часто используют их сокращенное обозначение: соответственно C3S, C2S, С3А и C4AF. Содержание этих минералов в портландцементном клинкере обычно колеблется в следующих пределах: 40 - 65% C3S; 15 - 40 % C2S; 2 - 15 % C3A и 10 - 20% С4АF. При увеличении содержания указанных выше минералов портландцемент получает специальное название. Так, при большом содержании C3S (более 56%) его называют алитовым; C2S (более 38% ) - белитовым; С3А (более 12%) - алюминатным и пр. Если в клинкере содержится повышенное количество двух минералов, его соответственно называют алитоалюминатным и пр. Каждый из клинкерных минералов имеет свои специфические свойства.
Трехкальциевый силикат (алит) является химически активным минералом, он оказывает решающее влияние на прочность и скорость твердения цемента. Взаимодействие его с водой происходит с большим тепловыделением. Алит обладает способностью быстро твердеть и набирать высокую прочность, поэтому повышенное содержание трехкальциевого силиката обеспечивает получение из данного клинкера высокомарочного портландцемента.
Двухкальциевый силикат (белит), затворенный водой, в начальный период твердеет медленно, при этом выделяется очень мало теплоты. Продукт твердения в течение первого месяца обладает невысокой прочностью, но затем на протяжении нескольких лет при благоприятных условиях прочность его неуклонно возрастает.
Трехкальциевый алюминат характеризуется высокой химической активностью, в первые сутки твердения он выделяет наибольшее количество теплоты гидратаци и быстро твердеет. Однако продукт его твердения имеет низкую долговечность и малую стойкость против воздействия сернокислых соединений.
Четырехкальциевый алюмоферрит характеризуется умеренным тепловыделением, твердеет он значительно медленнее, чем алит, но быстрее, чем белит. Прочность продуктов его гидратации несколько ниже, чем у алита.
Располагая данными о минералогическом составе портландцементного клинкера и зная свойства клинкерных минералов, можно заранее составить представленге об основных свойствах портландцемента и особенностях его твердения в различных условиях.
Твердение портландцемента. При затворении портландцемента водой сначала образуется пластичное клейкое цементное тесто, которое затем постепенно густеет, переходя в камневидное состояние. Твердение и есть процесс превращения цементного теста в цементный камень.
При смешивании портландцемента с водой в начальный период происходит растворение клинкерных минералов с поверхности цементных зерен, взаимодействие минералов с водой и образование насыщенного по отношению к клинкерным минералам раствора. По достижении насыщения растворение клинкерных минералов прекращается, но реакции между ними и водой продолжаются. Реакции присоединения воды к клинкерным минералам называют реакциями гидратации, а реакции разложения клинкерных минералов под действием воды на другие соединения - реакциями гидролиза.
Во втором периоде в насыщенном растворе идут реакции гидратации клинкерных минералов в твердом состоянии, т. е. происходит прямое присоединение воды к твердой фазе вяжущего без предварительного его растворения. Продуктами этих реакций являются гидратные новообразования в коллоидном виде. Период коллоидации сопровождается повышением вязкости цементного теста, обусловливающим схватывание цемента.
В третьем периоде протекают процессы перекристаллизации мельчайших коллоидных частиц новообразований, т.е. растворение мельчайших частиц и образований крупных кристаллов. Кристаллизация сопровождается твердением цементного теста и ростом прочности образовавшегося цементного камня.
Взаимодействие клинкерных минералов с водой протекает по следующим реакциям:
CaO . SiO2 + (n+1)Н2О = 2CaO . SiО2 . пН2О + Са(ОН)2;
2СаО . SiO2 + nH2O = 2CaO . SiO2 . nH2O;
СаО . Аl2О3 + 6H2O = 3CaO . Аl2О3 . 6H2O;
CaO . Аl2О3 . Fe2O3 + nH2O = 3CaO . Аl2О3 . 6H2O + CaO . Fe2O3(n - 6)Н2О
Приведенные химические реакции показывают, что в результате взаимодействия клинкерных минералов с водой образуются новые соединения - гидросиликаты, гидроалюминаты и гидроферриты кальция. Минералы C3S и C4AF, взаимодействуя с водой, подвергаются гидролизу, т.е. разложению, и минералы C2S и С3А гидратируются, т. е. присоединяют воду.
По скорости взаимодействия с водой клинкерные минералы располагаются в следующей последовательности: С3А, C4AF, C3S и C2S. Скорость гидратации клинкерных минералов в значительной мере определяет и скорость их твердения. Чем быстрее гидратирует минерал, тем быстрее происходит его схватывание и твердение.
В случае твердения цемента на воздухе рассмотренные выше процессы дополняются карбонизацией гидроксида кальция: Са(ОН)2 + СО2 = CaCO3 + H2O. Она происходит главным образом на поверхности цементного камня с образованием тонкой корки из углекислого кальция, способствующей повышению стойкости и прочности цементного камня.
В результате процессов коллоидации, кристаллизации, уплотнения гидратных новообразований и карбонизации образуется прочный цементный камень. Прочность цементного камня нарастает довольно быстро в течение первых 3 - 7 сут, затем в интервале 7 - 28 сут рост прочности замедляется. В дальнейшем повышение прочности относительно невелико, но может продолжаться в течение многих лет, особенно во влажной и теплой среде. В сухой среде или при отрицательных температурах процессы твердения цементного камня приостанавливаются и рост прочности прекращается. Замерзший цементный камень обладает способностью после оттаивания продолжать набирать прочность.
Твердение портландцемента можно ускорить за счет повышения температуры окружающей среды и введения химических веществ - ускорителей твердения (хлористого кальция, хлористого натрия и др.) в количестве 1 - 2% по массе цемента.
Твердение портландцемента сопровождается выделением теплоты. Это свойство портландцемента является положительным при бетонировании монолитных конструкций в зимних условиях и отрицательным в тех случаях, когда разогрев массивных бетонных конструкций (плотины, массивные фундаменты и т. п.) может привести к появлению в них трещин от температурного расширения.
Свойства портландцемента. К основным свойствам портландцемента относятся средняя плотность, истинная плотность, тонкость помола, водопотребность, сроки схватывания, равномерность изменения объема и прочность.
Средняя плотность портландцемента в рыхлом состоянии равна 1000 - 1100 кг/м3, а в уплотненном - 1400 - 1700 кг/м3. Истинная плотность портландцемента 3,05 - 3,15 г/см3.
Тонкость помола цемента характеризуется остатком на сите №008 (размер ячейки в свету 0,08 мм) не более 15% или удельной поверхностью - величиной поверхности зерен (в см) в 1 г цемента. Удельная поверхность портландцемента должна быть 2500 - 3000 см2/г. С увеличением тонкости помола цемента до 4000 - 4500 см2/г возрастает скорость твердения и повышается прочность цементного камня.
Водопотребность портландцемента определяется количеством воды (в %), которое необходимо для получения цементного теста нормальной густоты, т. е. заданной стандартной пластичности.
Нормальной густотой цементного теста считается его консистенция, при которой игла прибора Вика, погружаясь, не доходит до дна (стекла) кольца на 5 - 7 мм. Водопотребность портландцемента обычно колеблется в пределах 22 - 26% и зависит от минералогического состава и тонкости помола.
Сроки схватывания цементного теста нормальной густоты определяют на приборе Вика по глубине проникания иглы. Начало схватывания должно наступить не ранее чем через 45 мин, а конец схватывания - не позднее 10 ч от начала затворения. У портландцемента обычно начало схватывания наступает через 1- 2 ч, а конец - через 4 - 6 ч. На сроки схватывания портландцемента влияют его минералогический состав, тонкость помола и другие факторы. Равномерность изменения объема цемента устанавливают на образцах-лепешках, изготовленных из цементного теста нормальной густоты, при кипячении их в воде и выдерживании над паром. Цемент считают доброкачественным, если на лицевой стороне лепешек, подвергнутых испытаниям, нет радиальных, доходящих до краев трещин или сетки мелких трещин, видимых в лупу или невооруженным глазом, а также каких-либо искривлений. Одной из причин неравномерного изменения объема цементного камня при твердении является наличие в цементе свободных СаО и MgО, которые гидратируются с увеличением объема в уже затвердевшем цементном камне, разрушая его.
Прочность портландцемента характеризуется его маркой. Марку цемента устанавливают по пределу прочности при изгибе образцов призм размером 40х40х х160 мм и при сжатии их половинок, изготовленных из цементно-песчаного раствора состава 1:3 (по массе) на стандартном вольском песке при водоцементном отношении В/Ц=0,4 и испытанных через 28 сут. Предел прочности при сжатии в возрасте 28 сут называют активностью цемента, по ее величине устанавливают марку цемента. Например, если при испытании цемента установлена активность 43 МПа, то его относят к марке 400.
Портландцементы разделяют на марки 400, 500, 550 и б00.
Коррозия цементного камня. Возведенные с применением портландцемента бетонные сооружения могут подвергнуться разрушению (коррозии) под действием природных вод и агрессивных жидкостей. Разрушение обычно начинается с цементного камня, как наиболее подверженного коррозии.
Различают три основных вида коррозии цементного камня. Коррозия первого вида возникает при действии на цементный камень бетона проточных пресных вод (с малой временной жесткостью). Эти воды растворяют и вымывают гидроксид кальция, выделяющийся при гидролизе трехкальциевого силиката. В результате такого выщелачивающего действия воды повышается пористость цементного камня и снижается его прочность, что, в свою очередь, приводит к постепенному разрушению бетона.
Для повышения стойкости цементного камня в пресных водах рекомендуется вводить в портландцемент гидравлические добавки, которые связывают гидроксид кальция в малорастворимые соединения - гидросиликаты кальция.
Коррозия второго вида происходит при действии на цементный камень бетона минерализованных вод, содержащих химические соединения, которые вступают в обменные реакции с составляющими цементного камня. Образующиеся при этом продукты реакции либо легко растворяются и уносятся водой, либо выделяются в виде аморфной массы, не обладающей связующими свойствами.
Морская вода, вода соленых озер и лиманов, а также некоторые грунтовые воды, содержащие MgCl2, MgSO4, NaCI и другие соли, разрушающе действуют на цементный камень. Так, при воздействии на цементный камень вод, содержащих хлористый магний, последний взаимодействует с гидроксидом кальция цементного камня:
Са(ОН)2 + MgCl2 = CaCl2 + Mg(OH)2.
Образовавшийся в результате реакции хлористый кальций обладает хорошей растворимостью и быстро вымывается из бетона; остающийся гидроксид магния представляет собой аморфное вещество, не обладающее связующими свойствами.
Природные грунтовые воды обычно содержат свободную углекислоту СО2 и ее соли, главным образом Са(НСО3)2. Эти соли не опасны для цементного камня, но свободная (агрессивная) угпекислота разрушает его. Вначале растворенная углекислота взаимодействует с гидроксидом кальция, образуя труднорастворимый углекислый кальций, который уплотняет поверхность цементного камня. Однако при высоком содержании в воде свободная углекислота вступает в реакцию с углекислым кальцием: СаСО3 + СО2 + Н2О = Ca(НСО3)2. В результате образуется легкорастворимый в воде бикарбонат кальция, который вымывается из бетона.
Таким образом, основной причиной данного вида коррозии является присутствие в цементном камне свободного гидроксида кальция. Поэтому в состав цемента необходимо вводить активные минеральные добавки, которые связывают его в труднорастворимые соединения.
В качестве активных минеральных добавок к цементу чаще всего применяют трепелы, опоки, диатомиты, а также доменный гранулированный шлак, тоже способный связывать гидроксид кальция.
Коррозия третьего вида возникает при действии на цементный камень бетона сульфатных вод. Сульфаты CaSO4, МgSO4, Na2SO4 и др. входят в состав большинства природных грунтовых, а также сточных вод. В результате обменной реакции сульфатов с гидроксидом кальция в порах цементного камня образуется двуводный сернокислый кальций (гипс), который взаимодействует с гидроалюминатом кальция:
2(СаSО4 2H2О) + 3CaO Аl2О3 6H2O + 19Н2О = ЗСаО Аl2О3 3CaSО4 31Н2О.
Образующийся при этом труднорастворимый гидросульфоалюминат кальция, кристаллизуясь с большим количеством воды, увеличивается в объеме в 2,5 раза, что влечет за собой растрескивание бетона. Для предотвращения сульфатной коррозии бетона при его приготовлении следует применять сульфатостойкий портландцемент.
Безвредны для цементного камня соли кремниевой, кремнефтористоводородной и угольной кислот, слабые растворы щелочей, а также нефть, бензин, керосин и другие нефтепродукты, если в них нет остатков серной кислоты и значительного количества нафтеновых кислот.
Защиту цементного камня от коррозии осуществляют за счет применения цементов определенного минералогического состава, введения необходимого количества активных минеральных добавок, создания плотных бетонов, а также применения защитных покрытий и облицовок. Битумная изоляция, покрытие полимерными пленками, облицовка из стекла и керамики должны исключать воздействие агрессивной среды на бетон.
Применение портландцемента. Портландцемент используют в качестве вяжущего при изготовлении монолитного и сборного бетона и железобетона. Изделия и конструкции, изготовленные на портландцементе, можно применять в надземных, подземных и подводных условиях, а также в случае попеременного воздействия воды и отрицательных температур.
Портландцемент невысоких марок используют для приготовления кладочных и штукатурных растворов. Не следует изготовлять из портландцемента конструкции, подвергающиеся воздействию морской, минерализованной или даже пресной воды,- проточной или под сильным напором. В этих случаях рекомендуется применять цемент сиециальных видов - сульфатостойкий, пуццолановый портландцемент, шлакопортландцемент и др.
Портландцемент - высококачественное и дефицитное вяжущее, его необходимо расходовать экономно, заменяя, где это технически возможно, другими, более дешевыми, вяжущими веществами - известью, смешанными цементами и др.
|