МЕТОДИКА ВЫЯВЛЕНИЯ РЕЗЕРВОВ ИСПОЛЬЗОВАНИЯ ПРОИЗВОДСТВЕННОЙ МОЩНОСТИ ПИЩЕВЫХ ПРЕДПРИЯТИЙ Под резервами использования производственной мощности понимают возможности увеличения выпуска продукции. Резервы и степень их возможной реализации выявляются в процессе анализа использования производственной мощности. Действенность анализа зависит от того, насколько он конкретен и в какой мере является комплексным.
Первое требование обеспечивается в том случае, когда объектом анализа являются не только предприятие или цех, но и каждая входящая в их состав поточная линия. Второе требование направлено на то, чтобы выявить причины неполного использования мощности, для чего анализ использования мощности каждой поточной линии должен производиться по факторам, определяющим ее величину.
Анализ следует начинать с определения величины резервов и общего (интегрального) коэффициента использования мощности, для чего применяют следующие формулы: RM=M–A,
где Rm— резервы использования мощности; М — величина производственной мощности; А — величина выпуска продукции в натуральном выражении;
Км = A / M,
где Км— интегральный коэффициент мощности.
Интегральным (общим) этот коэффициент называется потому, что при его определении не выделяются отдельные направления использования оборудования (интенсивное и экстенсивное), а учитывается в совокупности их общее влияние.
Как величина резервов, так и коэффициент использования мощности могут быть плановыми или фактическими: в первом случае они характеризуют резервы, предусмотренные планом выпуска, а во втором — фактическую величину резервов и степень использования мощности в отчетном периоде.
Затем переходят к анализу факторов, определяющих мощность отдельной поточной линии, для чего изучают использование ведущих машин в двух направлениях: интенсивном и экстенсивном.
Максимальная величина интенсивного использования, т. е. выпуска в единицу времени, выражается технической нормой производительности машины NT. Резервы интенсивного использования мощности Rинт можно выразить формулой
Rинт = NT — q
где q— производительность ведущей машины в единицу времени (т. е. фактическая или плановая величина интенсивного использования). Коэффициент интенсивного использования оборудования Кинт можно выразить отношением
Кинт= q/NT.
Надо иметь в виду, что фактическая выработка в единицу времени (смену, сутки) не всегда может быть одинакова с фактической производительностью, а только в том случае, когда отсутствовали внутрисменные нерегламентированные простои. При наличии таких простоев выработка характеризует не только интенсивное, но и экстенсивное использование машины. В этом случае определить фактическую величину интенсивного использования можно двумя способами:
1) рассчитать производительность при действующих значениях переменных факторов (продолжительность рабочего цикла, величины брака и отходов, регламентированные перерывы);
2) увеличить фактическую выработку в единицу времени на то количество продукции, которое могло быть выработано за время выявленного нерегламентированного перерыва.
Для большей достоверности величины интенсивного использования оборудования рекомендуется определять средние (за несколько смен) фактические значения переменных факторов (при первом способе определения фактической производительности) и выработки в смену (сутки) и нерегламентированных простоев за это время (при втором способе).
Например, были выявлены следующие средние фактические значения переменных факторов производительности карамелеформующего агрегата
скорость цепи V— 66 м/мин; возвратные отходы а— 3 %; регламентируемые простои tn— 40 мин в смену.
Условно-постоянные факторы производительности имели следующие значения:
продолжительность смены Т — 480 мин; количество штук изделий в 1 кг К— 110; шаг цепи m— 38 мм.
Подставляя эти данные в формулу расчета производительности агрегата, получим следующую величину
Несовпадение полученных разными способами величин фактической производительности возможно при недостаточно полном учете результатов работы, особенно внутрисменных простоев.
Из рассмотренных способов определения фактической величины интенсивного использования оборудования (т. е. фактической производительности) лучшим является первый, при котором конкретизированы условия работы ведущей машины, что важно для выявления причин образования резервов и возможного уровня их использования в очередном плановом периоде и в перспективе.
Эти причины выявляются путем сравнения величины переменных факторов машины, принимаемой при расчете технической нормы производительности, с достигнутой или намечаемой планом величиной.
Скорость, движения рабочих органов (или продолжительность рабочего цикла), брак и регламентируемые простои являются общими для большинства пищевых производств переменными факторами производительности.
Если в приведенном выше примере NT = 7460кг в смену, то, используя вышеприведенные формулы, получим
Таблица 1
Показатели
| Значения переменных факторов
| V, м/мин
| t , мин
| а, %
| Техническая норма производительности
Фактическая производительность
|
|
|
|
Из данных табл. 1 видно, что величина резерва интенсивного использования 721 кг в смену (9,7%) объясняется меньшей скоростью, более длительными регламентированными простоями и более высокой величиной возвратных отходов, чем предусмотрено технической нормой.
Так, анализ скорости формования выявил возможность повышения ее на 2 м/мин без ухудшения качества продукции. Изучение методов чистки, смазки, регулировки агрегата показало возможность сокращения регламентированных простоев на 10 мин в смену, анализ причин возвратных отходов дал основание снизить их величину до 2 %.
При этих условиях проектируемая величина интенсивного использования агрегата составит (qп— пооектируемая производительность ):
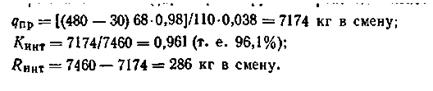
Таким образом, результатом анализа интенсивного использования явилось повышение производительности на 435 кг в смену, или на 5,8 %, в результате чего резерв интенсивного использования уменьшился, т. е. сократился разрыв между намечаемой производительностью и ее лучшим отраслевым показателем.
При обеспечении достаточной пропускной способности машин в поточной линии и осуществлении организационно-технических мероприятий для достижения намеченных условий производительность 7174 кг в смену может быть принята в качестве технико-экономической нормы использования поточной линии и использована при расчете производственной программы.
Анализ интенсивного использования должен быть проведен по каждому виду изделий, выпускаемому поточной линией, так как степень освоения технических норм производительности и условия, ее определяющие, могут быть различными. Для обобщения результатов анализа интенсивного использования поточной линии, выпускающей несколько видов изделий, следует применить формулу для определения технической нормы производительности в этих условиях, затем определить фактическую и проектируемую производительность по ассортименту, после чего найти резервы и коэффициенты интенсивного использования мощности данной поточной линии.
Сумма выявленных таким образом резервов интенсивного использования поточных линий составит величину резервов соответствующего цеха (предприятия).
Важное значение имеет улучшение экстенсивного использования оборудования, т. е. использование по времени работы. Максимальной величиной экстенсивного использования является фонд времени, принятый при расчете производственной мощности. Поэтому резервы экстенсивного использования оборудования Rэкст в абсолютном выражении (плановые и фактические) определяют по формуле

Анализ экстенсивного использования следует проводить по каждой поточной линии, после чего могут быть получены сводные результаты по цеху или предприятию.
Объектом анализа являются все виды простоев оборудования: плановые и внеплановые, целодневные и внутрисменные. Для выявления конкретных причин потерь времени простои должны быть классифицированы по видам (технические, организационные, технологические). Каждый вид простоев должен быть тщательно изучен, в результате чего должны быть разработаны и проведены мероприятия по устранению нерегламентированных простоев и возможному сокращению плановых простоев.
В качестве материалов для анализа используются акты о простоях оборудования за отчетный период. Достоверность величины выявленных резервов экстенсивного использования оборудования определяется полнотой учета простоев оборудования, которая не всегда является достаточной. Наибольшая полнота учета достигается при применении автоматических средств. Большую роль при анализе экстенсивного использования оборудования играют фотографии рабочего времени, которые позволяют полностью выявить не только все виды простоев, но и периодичность и причины их возникновения. Единственным, но весьма существенным недостатком этого метода является его большая трудоемкость, которая значительно снижается при переходе к самофотографиям рабочего дня. Уменьшение или полное устранение простоев оборудования по техническим причинам достигается в результате улучшения качества ремонта и периодического осмотра оборудования.
Для сокращения времени на наладку или устранения поломки машины участки основного производства должны быть оснащены средствами связи и сигнализации, позволяющими быстро вызвать работника технической службы. Важное значение для сокращения простоев по техническим причинам имеет материальная заинтересованность дежурно-ремонтного персонала в сокращении и устранении простоев.
Широкое распространение на предприятиях пищевой промышленности бригадного метода работы, повышающего заинтересованность всех членов бригады в улучшении конечных результатов работы, выдвигает более высокие требования к качеству ремонтного обслуживания.
В том случае, когда отчетные данные о простоях оборудования вследствие их неполноты не позволяют выявить достоверную величину резервов экстенсивного использования, может быть использована следующая зависимость между коэффициентами использования мощности для определения коэффициента экстенсивного использования:
Поскольку Км и Кинт всегда могут быть определены по приведенным выше формулам,
можно найти Кэст.
Однако этот метод определения Кэстявляется условным, он не позволяет выявить причины простоев и должен применяться совместно с основным. Цель применения этого метода — выявить (хотя бы приближенно) потери времени и направить внимание работников предприятия на глубокий и подробный анализ экстенсивного использования оборудования.
Например, в результате анализа использования производственной мощности получены следующие коэффициенты: Км = 78,9%; Кинт = 91,3%; Кэкст = 98,1 %. При этих данных создается видимость почти полного использования оборудования по времени. Определим Кэкст, используя указанную зависимость: Кэкст = 78,9/91,3* 100 = 86,4 %, т. е. главной причиной неполного использования мощности явились как раз простои оборудования. Их величина составила 13,6% вместо учтенной 1,9% (100— 98,1).
Таким образом, комплексный анализ использования производственной мощности позволяет не только выявить полную величину резервов, но и предусмотреть использование их в возможном размере.
|