Краткие теоретические сведения по теме. Пример выполнения контрольного задания №2
На практике для обеспечения требуемой точности замыкающих звеньев сборочных размерных цепей применяют следующие методы:
− полной взаимозаменяемости;
− неполной взаимозаменяемости;
− групповой взаимозаменяемости;
− пригонки;
− регулирования.
Рассмотрим перечисленные методы на конкретном примере: необходимо обеспечить зазор ε между торцом зубчатого колеса и простановочным кольцом механизма (рис. 23, а).
Замыкающим звеном в этой цепи является зазор ε, величина которого обусловливается точностью выполнения размеров зубчатого колеса А1 = 80 мм, корпуса А2 = 90 мм и кольца А3 = 10 мм.
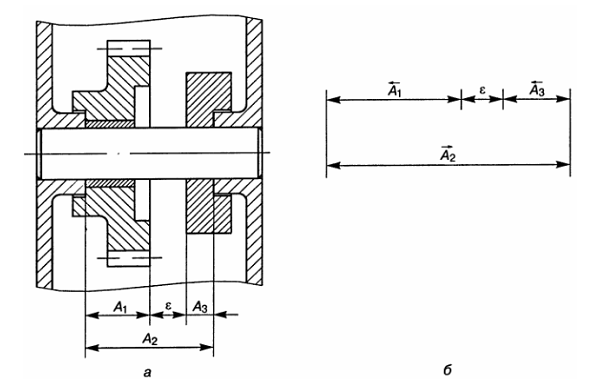
Рисунок 23. Эскиз сборочной единицы: а – размерная схема процесса сборки по обеспечению зазора ε; б – размерная цепь
Из служебного назначения рассматриваемой сборочной единицы следует, что наименьший зазор εнм = 0 (EIε = 0), а наибольший εнб = 0,2 (ESε = 0,2). Следовательно, поле допуска на зазор
Тε = ESε – EIε = 0,2 – 0 = 0,2
а координата середины поля допуска
Eсε = 0,5 (EIε + ESε) = 0,5 (0 + 0,2) = +0,1 мм
Схема размерной цепи, замыкающим звеном которой является зазор, представлена на рис. 23, б. Размеры А1 и А3 – уменьшающие, а размер А2 - увеличивающий. Основное уравнение размерной цепи в этом случае:
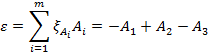
где m – число увеличивающих и уменьшающих звеньев цепи, m = 3;
ξАi – передаточное отношение (для плоских линейных цепей с параллельными звеньями ξАi = +1 для увеличивающих и ξАi = -1 для уменьшающих составляющих звеньев).
Метод полной взаимозаменяемости. При этом методе должно быть выполнено условие
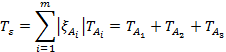
Учитывая, что размеры деталей механизма контролируются калибрами и скобами, устанавливаем допуски на размеры А1, А2 и А3 по 9-му квалитету точности: T’A1 = 0,074 мм; T’A2 = 0.087 мм; T’A3 = 0.036 мм (штрих означает здесь и далее производственное значение допуска). Очевидно, что
Данное неравенство позволяет сделать вывод о возможности выполнения размеров данной цепи с точностью по 9-10-му квалитету. Если неравенство ложно, необходимо ужесточить допуски на составляющие размеры в соответствии со среднеэкономической точностью выполнения размера.
Назначаем отклонения, ориентируясь на вид поверхностей (охватываемые или охватывающие), на размеры А1 и А2, кроме А3, как правило наиболее легко выполнимого (ES’A1=0, EI’A1=-0,074 мм и ES’A2=0, EI’A2=-0,087 мм), и определяем координаты середин их полей допусков: Ec’A1 = -0.037 мм и Ec’A2 = 0.0435 мм. Координату середины поля допуска третьего звена находимо из уравнения, по структуре совпадающего с основным уравнением размерной цепи:

или, подставив значения,
0,0985 = - (- 0,037)+0,0438 – Ес´А3
Таким образом, Ес´А3 = - 0,018 мм. Следовательно,

Проверка уравнений
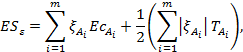

подтверждает правильность расчетов.
Итак, предельные отклонения составляющих звеньев: А1 = 80-0,074 мм, А2 = 90+0,087 мм и А3 = 10-0,036 мм.
Метод неполной взаимозаменяемости. При этом методе должно быть выполнено условие
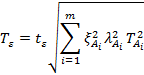
где tε – коэффициент риска;
- коэффициент, учитывающий закон распределения отклонений размеров цепи Аi.
Принимая tε = 3 (риск в данном случае Р = 0,27% и =1/9; условия изготовления деталей таковы, что распределения отклонений размеров будет близким к закону Гаусса), получим
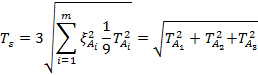
В соответствии с данным методом представляется возможным расширить поля допусков на изготовление деталей. Приняв по 10-му квалитету точности TA1=0,12 мм, TA2=0,14 мм, TA3=0,058 мм, будем иметь
Координаты середин полей допусков размеров А1 и А2: Ес´А1=-0,06мм и Ес´А2=0,07мм, тогда
Ес´ε = -Ес´А1 + Ес´А2 - Ес´А3 = -(-0,06) + 0,07 - Ес´А3 = 0,1 мм.
Отсюда находим Ес´А3 = 0,3мм и, соответственно, ES´A3 =0,059 мм и EI′A3 =0.001 мм. Проверка уравнений
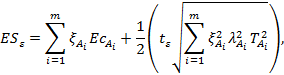
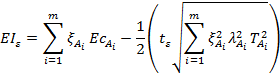
подтверждает правильность расчетов и возможность принять, например, стандартизированные отклонения ЕS´А3 = 0,05 мм и EI´A3 = 0,028 мм. Предельные отклонения составляющих размеров: А1 = 80-0,12 мм, А2 = 90+0,14 мм и мм.
Метод групповой взаимозаменяемости. Групповую взаимозаменяемость (селективную сборку) применяют, когда полная взаимозаменяемость недостижима или экономически нецелесообразна.
При расчете допусков должно быть соблюдено условие
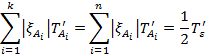
где k, n - соответственно число увеличивающих и уменьшающих звеньев размерной цепи (k + n= m).
Для рассматриваемой задачи
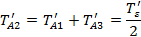
Допустим, число групп z, на которые должны быть рассортированы детали после изготовления, равно 3. Тогда мм и мм.
Учитывая степень точности изготовления деталей, установим и Устанавливаем для размеров А1 и А2 поля допусков каждой группы на размер , для чего вначале определяем координаты их середин.
Используя уравнение Есε = -ЕсА1 + ЕсА2 - ЕсА3, для I, II и III групп соответственно имеем:
Тогда
Схематически поля допусков для шестерни, корпуса и простановочного кольца изображены на рис. 24. Видно, что при сопряжении деталей из одноименных групп обеспечивается необходимый зазор Тε = 0,2 мм и его среднее значение Есε = +0,1 мм.
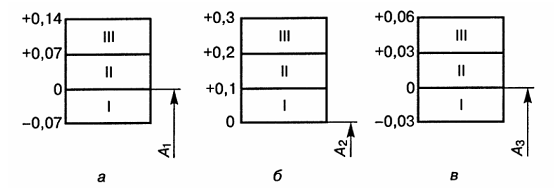
Рисунок 24 – Поля допусков I, II и III групп сортировки для шестерни (а), корпуса (б) и простановочного кольца (в) сборочной единицы, изображенной на рис. 23
Метод пригонки. Необходимой точности замыкающего звена можно добиться путем снятия слоя металла с компенсирующей детали. При пригонке рассчитывают предельные отклонения компенсирующего звена с учетом того, что на нем должен остаться достаточный слой металла, подлежащий удалению в процессе сборки. Величину ∆k необходимого для пригонки слоя металла определяют методом полной взаимозаменяемости как очевидную разность наибольшего расчетного и наибольшего эксплуатационно допустимого значения замыкающего звена:

Для принятых отклонений составляющих звеньев A′1 = 80-0,21 мм, А′2 = 90+0,3 мм и А′3 = 10-0,09 мм найдем:
мм
мм
тогда
∆k = 0,3 + 0,5 (0,6 – 0,2) – 0,1 = 0,4.
Из этого следует, что компенсирующий размер А3 должен быть задан в виде А3 = мм. Предельные отклонения составляющих размеров: А1=80-0,21 мм, А2=90+0,3 мм и А3 = мм.
Если компенсирующее звено входит в число уменьшающих звеньев размерной цепи (размер компенсатора при пригонке уменьшается), то поправку ∆k вносят со своим знаком, а если в число увеличивающих звеньев (размер компенсатора при пригонке увеличивается), то поправку ∆k вносят с обратным знаком.
|