Ремонт насосного оборудования
В объем ремонтных работ входят следующие мероприятия. При профилактическом осмотре [7]:
‒ проверка осевого разбега ротора;
‒ очистка и промывка картеров подшипников, смена масла, промывка масляных трубопроводов;
‒ ревизия сальниковой набивки и проверка состояния защитных гильз;
‒ проверка состояния полумуфт, промывка и смена смазки.
При текущем ремонте:
‒ полная разборка с проверкой зазоров в уплотнениях ротора в корпусе насоса, проверка биения ротора;
‒ ревизия и замена деталей торцевых уплотнений.
При капитальном ремонте:
‒ ревизия всех сборочных единиц и деталей;
‒ замена рабочих колес, валов, уплотняющих колец корпуса, грундбукс, распорных втулок.
Перед отправлением в ремонт насос подвергается наружному осмотру и контролю. Проверяется наружное состояние насоса, его комплектность и проводятся следующие замеры, оформляемые актом:
‒ смещение положения ротора в корпусе насоса в радиальном направлении;
‒ осевой разбег ротора;
‒ несовпадение осей насоса и привода в радиальном направлении.
Насосы сдаются в ремонт в собранном виде, полностью укомплектованные деталями вне зависимости от степени их износа.
При отсутствии базовых деталей или при наличии сквозных трещин в стенках корпуса или днища насос списывается. Допускается восстановление таких насосов по разовой калькуляции.
Разборка насоса. После наружной промывки насос разбирается в такой последовательности:
‒ выпрессовываются полумуфты, вынимается шпонка, предварительно открепляется и снимается шайба;
‒ открепляется и снимается кронштейн;
‒ отворачиваются гайки, крепящие корпус насоса к крышке, снимается крышка вместе с корпусом подшипника, ротором и другими деталями;
‒ снимается рабочее колесо (для двухступенчатых насосов после снятия диафрагмы с прокладкой снимается второе рабочее колесо);
‒ снимаются крышка насоса, втулка сальника, фонарь сальника, грундбукса и другие детали торцового уплотнения;
‒ вынимается защитная гильза;
‒ снимаются крышки подшипника с прокладками и втулками;
‒ из корпуса подшипника вынимается ротор, который затем разбирается.
Промывка и очистка деталей. Перед дефектацией детали очищаются от загрязнения, промываются, обезжириваются и высушиваются. Детали, покрытые тяжелыми маслянистыми отложениями (детали проточной части насоса), подвергаются промывке в ванне с 8—10% раствором каустической соды при 100 °С в течение 30—40 мин. Детали с довольно сильной коррозией подвергаются травлению согласно инструкции по их химической очистке.
Промытые и очищенные детали помещаются на 10—15 мин в водный раствор пассиватора для предохранения от коррозии. После пассивирования (раствор содержит 20 г/л воды каустической соды и 50 г/л воды хромпика) детали просушиваются при нормальной температуре. Срок хранения деталей, обработанных пассиватором, составляет 5—10 суток.
Технические требования на дефектацию и ремонт. Дефектация деталей осуществляется на специальном рабочем месте, оснащенном картами дефектации и необходимым комплектом приборов и измерительных инструментов.
Карты дефектации (дефектные ведомости) являются основным техническим документом, на основании которого проводятся осмотр, измерение, а при необходимости испытание деталей и сопряжений с последующей сортировкой их на три группы:
‒ детали, годные в сопряжении с новыми деталями;
‒ детали, подлежащие ремонту;
‒ детали, непригодные для дальнейшего использования.
Контроль подшипников качения включает осмотр, проверку на шум и легкость вращения, измерение осевого и радиального зазоров, измерение размеров колец. Диаметры колец измеряются только в случае сдвига обойм на валу или корпусе, а также при наличии следов коррозии, ожогов и появлении черноты.
В подшипниках качения не допускаются:
‒ трещины или выкрашивание металла на кольцах и телах качения, цвета побежалости в любом месте подшипника;
‒ выбоины и отпечатки (лунки) па беговых дорожках колец;
‒ шелушение металла, чешуйчатые отслоения;
‒ коррозионные раковины, забоины, риски и вмятины на поверхности качения, видимые невооруженным глазом;
‒ надломы, сквозные трещины на сепараторе, отсутствие или ослабление заклепок сепаратора;
‒ забоины и вмятины на сепараторе, препятствующие плавному вращению подшипника;
‒ заметная на глаз и на ощупь ступенчатая выработка рабочей поверхности колец;
‒ осевой зазор более 0,08 мм и радиальный зазор более 0,1 мм;
‒ при проверке на легкость вращения ‒ резкий металлический или дребезжащий звук, а также заметное притормаживание и заедание.
Пружинные шайбы не должны иметь трещин или надрывов. Бывшие в употреблении пружинные шайбы используются повторно, если они не потеряли упругости. При этом нормальный развод шайбы должен быть равен ее толщине.
Большинство насосов химических производств перекачивают коррозионно-активные продукты. В связи с этим стенки корпуса изнашиваются.
Износ отдельных мест внутренней полости корпуса должен быть устранен наплавкой металла с помощью электросварки. Риски, забоины и вмятины на плоскостях разъема корпуса устраняются зачисткой шабером или заваркой. Значительно изношенные привалочные поверхности протачиваются или фрезеруются. Можно также осуществлять расточку изношенных мест и запрессовку втулок с последующей расточкой до номинальных размеров.
При вращении роторов в корпусе насоса возможен износ шеек и резьбы, искривление или поломка вала. Искривление валов происходит в результате выхода из строя подшипников или ударов частей ротора о неподвижные детали насоса.
Износ шеек валов может происходить из-за появления рисок, задиров, коррозионных каверн и по другим причинам с последующим выходом из строя подшипников качения или скольжения.
Как правило, поломка вала наблюдается в местах перехода вала с диаметра посадочного места под защитную гильзу на диаметр шейки вала. Поломка происходит в результате концентрации местных напряжений.
Восстановление изношенных шеек вала в зависимости от степени износа осуществляется следующими способами:
‒ до 0,3 мм ‒ электролитическим хромированием;
‒ от 1,5 до 2,0 мм ‒ электролитическим железнением;
‒ от 2,0 до 3,0 мм ‒ автоматической вибродуговой наплавкой;
‒ от 3,0 до 4,0 мм ‒ ручной газовой наплавкой;
‒ свыше 4,0 мм ‒ ручной электродуговой наплавкой.
Нарушенная резьба на валу восстанавливается резцом. Если повреждения значительны, то этот участок вала протачивается до основания резьбы, а затем наплавляется, обрабатывается и на нем нарезается новая резьба.
Рабочие колеса выходят из строя вследствие коррозионного и эрозионного износа, сильного осевого сдвига ротора в результате неправильной сборки насоса или разрушения радиальноупорных подшипников, попадания в насос посторонних предметов.
При ремонте колеса восстанавливаются наплавкой поврежденных мест с последующей проточкой. Для некоторых конструкций возможна замена поврежденного диска. В этом случае неисправный диск срезается, а вместо него с помощью электрозаклепок приваривается новый диск.
Чугунные колеса заменяются новыми или наплавляются медным электродом с последующей проточкой.
Торцовые уплотнения. К быстроизнашивающимся деталям торцовых уплотнений относятся пара трения, пружины, уплотнительные кольца из резины или фторопласта. Износ пары трения проявляется в повышенной утечке агента. Если она обусловлена задиром трущихся поверхностей, то возможна притирка пары трения. При необходимости пара трения заменяется. В комплекте запасных частей к торцовому уплотнению имеются все быстроизнашивающиеся детали. Одно из колец пары трения может быть изготовлено из следующих материалов: углеграфита2П-1000, пропитанного фенолофор-мальдегидной смолой, силицированного графита ПГ-50С, фторопласта-4 и композиции на основе фторопласта и кокса ‒ ФКМ-105 и 4К.-20.
Второе кольцо обычно изготавливается из металла.
Торцовые уплотнения выходят из строя из-за износа пар трения и коррозии. Ремонт торцового уплотнения заключается в изготовлении и замене вышедших из строя деталей. Для возможности изготовления при ремонте колец трения поставляются углеграфитовые заготовки в форме цилиндров определенных размеров, из которых кольца вытачиваются на токарном станке. Углеграфитовые заготовки поставляются пропитанными или непропитанными. Пористость углеграфита доходит до 30%. Графит, предназначенный для торцовых уплотнений, без пропитки клеящим составом непригоден для изготовления графитовых колец торцовых уплотнений. Пропитка обработанных колец осуществляется эпоксидным клеем холодного отверждения следующего состава (по массе).
Пропитка проводится в специальном приспособлении (рисунок 4), в котором на пропитывающий состав после его заливки создается давление 0,5 ‒ 0,6 МПа с помощью сжатого воздуха. Продолжительность пропитки ‒ 15 ‒ 20 мин. После пропитки эпоксидный состав полимеризуется при комнатной температуре в течение 24 ч или в термошкафу при 50 °С в течение 3 ч.
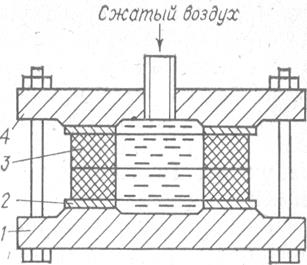
1,4 ‒ фланцы; 2 ‒ прокладка; 3 ‒ кольца
Рисунок 4 ‒ Приспособление для пропитки углеграфитовых колец
Пропитка может осуществляться также компаундом, состоящим (по массе) из 10 частей эпоксидной смолы ЭД-6, 2 частей дибутилфталата, 1 части полиэтиленполиамина и 15 частей толуола, добавляемого для увеличения глубины пропитки. Глубина пропитки увеличивается также при применении вакуума. Заготовки колец после промывки в ацетоне и сушки закладываются в контейнер с компаундом, а контейнер устанавливается в камеру низкого давления, где при давлении 0,015 МПа заготовки выдерживаются 1,5 ч.
После шлифовки доводка рабочих поверхностей пар трения осуществляется на плите-притире. Испытание собранного уплотнения может выполняться с использованием сверлильного станка, шпиндель которого служит для вращения одного из колец. Обкатка без давления проводится в течение 1 ч, затем при вращении одного из колец создается давление от баллона сжатого воздуха. Падение давления, которое контролируется по манометру, не должно превышать 0,05 МПа в 1 ч.
Чрезмерный нагрев уплотнения может быть вызван выходом из строя системы охлаждения и циркуляции и работой уплотнения в условиях отсутствия смазки. При ремонте система охлаждения должна быть прочищена.
Поломанные пружины заменяются. Уплотнительные резиновые кольца при эксплуатации теряют эластические свойства или набухают. Поэтому при проведении ремонта насоса их следует заменить.
Разборка-сборка торцовых уплотнений проводится квалифицированными рабочими, имеющими опыт ремонта сложных машин. Это связано с тем, что ремонт торцовых уплотнений является ответственной операцией. Детали торцового уплотнения требуют бережного обращения. Перед сборкой они должны быть тщательно очищены и промыты в керосине.
Испытания и прием насоса из ремонта. После внешнего осмотра и установки насоса на испытательном стенде проводится его испытание, которое включает в себя следующие этапы:
‒ кратковременный пуск;
‒ прогрев насоса;
‒ испытание на рабочем режиме.
Кратковременный пуск (до 3 мин) насоса осуществляется при закрытой задвижке на напорном трубопроводе. При этом проверяются:
‒ направление вращения ротора;
‒ показания приборов;
‒ смазка подшипников.
ЗАКЛЮЧЕНИЕ
В отчете рассмотрена абсорбционно-газофракционирующая установка (АГФУ-1), которая предназначена для сбора, компремирования жирных газов, стабилизации рефлюксов и бензинов термических крекингов, бензинов с установок 21-10, ЛЧ-24-7, факельных конденсатов, конденсата прямогонного газа.
Технологический процесс абсорбционно–газофракционирующей установки (АГФУ) связан с применением и переработкой жидких и газообразных углеводородов при относительно высокой температуре и повышенном давлении.
Характерной особенностью абсорбционно–газофракционирующих установок (АГФУ) является сочетание предварительного разделения газов на легкую и тяжелую части абсорбционным методом с последующей их ректификацией.
АГФУ используются повсеместно: на газобензиновых заводах для переработки попутных нефтяных газов и продуктов стабилизации нефти, на нефтеперерабатывающих и нефтехимических предприятиях для разделения разнообразных нефтезаводских газовых смесей.
|