Структура основного производства. Состав оборудования цеха. Общецеховые проектные решения
Производственная программа
Производственная программа приведена в таблице 4.
В соответствии с заданием в планируемом цехе будут выпускаться следующие виды продукции:
- прокат тонколистовой холоднокатаный из низкоуглеродистой качественной стали для холодной штамповки по ГОСТ 9045-93, толщиной 0,40 –1,5 мм, шириной до 1250 мм, общая доля в производстве – 0,37;
- прокат тонколистовой холоднокатаный горячеоцинкованный с полимерным покрытием с непрерывных линий по ГОСТ Р 52146-2003, толщиной 0,35-1,0 мм шириной до 1250 мм, общая доля в производстве – 0,33;
- прокат холоднокатаный оцинкованный по ГОСТ Р 52246-2004, толщиной 0,30-1,0 мм шириной до 1250мм, общая доля в производстве - 0,30;
Требования к готовой продукции проектируемого цеха.
ГОСТ 9045-93[1]распространяется на тонколистовой холоднокатаный прокат из низкоуглеродистой качественной стали толщиной до 3,9 мм, предназначенный для холодной штамповки.
Производимая продукция по ГОСТ 9045-93 в проектируемом цехе является:
- рулоны;
- по качеству отделки поверхности – I (особо высокой отделки поверхности), II (высокой отделки). Описание характеристики качества отделки поверхности I и II группы приведены в таблице 1;
- по способности к вытяжке (прокат толщиной до 2 мм) – весьма особо сложной (ВОСВ), особо сложной (ОСВ), сложной (СВ).
- по геометрии - предельные отклонения по толщине проката не должны превышать для толщин: ( 0,35 0,03 ) мм,(0,5-0,9 0,05) мм,(0,9-1,2 0,06) мм.
Разнотолщинность проката в одном поперечном сечении не должна превышать половины суммы предельных отклонений по толщине. Предельные отклонения по ширине проката не должны превышать (+4 мм при повышенной, +6 мм при нормальной точности). Серповидность полосы не должна превышать 3 мм на длине 1 м. Телескопичность рулонов не должны превышать 60 мм.
Прокат изготовляют в термически обработанном и дрессированном состоянии, при этом допускаются полосы - линии скольжения, пятна слипания сварки и перегиб, а показатели по пределу текучести, глубине сферической лунки, относительному удлинению, плоскостности и шероховатости не нормируются [1].
Таблица 1. Характеристика качества отделки поверхности производимой продукции
Группа отделки
| Характеристика качества отделки поверхности
| I
| На лицевой стороне проката не допускаются дефекты, кроме отдельных рисок и царапин длиной менее 20мм.
На обратной стороне проката не допускаются дефекты, глубина которых превышает ¼ суммы предельных отклонений по толщине, а также пятна загрязнений, цвета побежалости и серые пятна.
| II
| На обеих сторонах проката не допускаются дефекты, глубина которых превышает 1/2 суммы предельных отклонений по толщине и выводящие за минимальные размеры по толщине, а также цвета побежалости на расстоянии, превышающем 50 мм от кромок. На лицевой стороне (лучшей по качеству поверхности) не допускаются риски и царапины длиной более 50 мм
| ГОСТ Р52146-2003[2]- распространяется на прокат холоднокатаный и холоднокатаный горячеоцинкованный с полимерным покрытием нанесенным валковым методом в агрегатах непрерывного действия, предназначенный для применения в строительстве, приборостроении, при производстве внешних панелей бытовой техники. Стандарт может быть распространен на окрашенный прокат, применяемый в других отраслях промышленности.
Производимая продукция в проектируемом цехе по ГОСТ Р 52146-2003 является рулоны с лакокрасочным покрытием холоднокатаного горячеоцинкованного проката (ЛКПОЦ).
По виду покрытий подразделяется на:
-одностороннее – I;
-двустороннее – II.
Прокат с односторонним полимерным покрытием – это прокат с двухслойным полимерным покрытием на лицевой стороне и однослойным полимерным покрытием на обратной стороне. Двустороннее с двухслойным покрытием с обеих сторон.
По способности к вытяжке основы:
- СВ – сложной;
- ВГ – весьма глубокой;
- Г – глубокой;
- Н – нормальной.
По внешнему виду поверхности качество покрытия подразделяют на два класса: 1 и 2. Описание классов приведено в таблице 2.
Таблица 2. Характеристики качества полимерного покрытия расчетного профиля.
Класс покрытия
| Характеристика внешнего вида покрытия на лицевой стороне проката
|
| Поверхность покрытия должна быть однатонной.
Поверхность покрытия должна быть сплошной, без дефектов, проникающих до металлической основы.
На поверхности не должен визуально наблюдаться узор кристаллизации цинка.
Допускаются отдельные дефекты размером не более 3 мм, не проникающие до металлической основы, или небольшие группы таких дефектов.
Допускаются дефекты покрытия на расстоянии не более 5 мм от кромки рулона.
|
| Кроме дефектов, указанных для 1-го класса покрытия, допускаются:
участки разнооттеночности;
участки с различным блеском;
шагрень;
оспины;
царапины, не проникающие до металлической основы;
отпечатки, надавы;
Допускаются дефекты покрытия на расстоянии не более 10 мм от кромки рулона.
| По плоскостности на:
- ПВ – высокой;
- ПУ – улучшенной;
- ПН – нормальной.
В рулонах проката с полимерным покрытием 1-го класса допускается до 5% проката с полимерным покрытием 2-го класса.
Цвет полимерного покрытия на лицевой и обратной стороне, и дополнительные требования к покрытию обратной стороны проката устанавливают по согласованию между изготовителем с потребителем.
Для защиты полимерного покрытия от механических повреждений при транспортировке и переработке допускается нанесение на лицевую сторону проката легко удаляемой полимерной пленки [2].
ГОСТ Р 52246-2004[3]. Настоящий стандарт распространяется на листовой прокат из низкоуглеродистой стали, оцинкованный в агрегатах непрерывного горячего цинкования, предназначенный для изготовления изделий методами изгиба и соединения в замок, а также профилированных, штампованных и сварных металлических изделий.
Производимый прокат с цинковым покрытием подразделяют по назначению на марки:
- 01 – для изготовления плоских изделий и плоских изделий методом изгиба;
- 02 – для изготовления посудохозяйственных изделий, изделий методом изгиба и соединением в замок;
- 03 – для изготовления штампованных изделий весьма глубокой вытяжки и сложных профилей;
- 220,250,280,320,350 – для изготовления профилированных изделий.
Цинковое покрытие нанесенное с двух сторон проката, подразделяется в зависимости от массы покрытия на классы: 60, 80, 100, 140, 180, 220, 225, 275, 350.
Покрытие оцинкованного проката по узору кристаллизации и отделке поверхности подразделяют:
- с нормальным узором кристаллизации цинка – Н;
- с нормальным узором кристаллизации цинка дрессированное – НД;
- с минимальным узором кристаллизации цинка – М;
- с минимальным узором кристаллизации цинка дрессированное МД.
По характеру кромки: с обрезной кромкой (О), и не обрезной кромкой (НО).
По способу консервации поверхности подразделяется: пассивированный, промасленный, пассивированный с промасливанием.
Оцинкованный прокат изготавливается в рулонах шириной от 900 до 1250 мм. Толщиной, включая толщину цинкового покрытия от 0,3 до 1,0мм.
Прокат для выпускаемой продукции должен быть с регламентированным химическим составом.
Химический состав стали по плавочному анализу должен соответствовать требованиям таблице 3.
Таблица 3. Химический состав стали 08Ю и 08пс.
Марка стали
| Массовая доля элементов, %
| углерода
| марганца
| серы
| фосфора
| кремния
| Алюминиякислотораство-римого
| не более
| 08Ю
| 0,07
| 0,35
| 0,025
| 0,020
| 0,03
| 0,02 - 0,07
| 08пс
| 0,09
| 0,45
| 0,300
| 0,025
| 0,04
| 0,02 - 0,07
|
Таблица 4. Производственная программа.
Наименование продукции
| Условия поставки
| Характерные
потребительские свойства
|
Выпуск,
тыс.т.
| 1. Прокат тонколистовой холоднокатаный из низкоуглеродистой качественной стали для холодной штамповки
h =0,40-1,50мм
B от 900 до 1250мм.
| ГОСТ 9045-93
| Категория вытяжки
| sТ, МПа не более
| sВ, Мпа
| d4, %, не менее при h
|
| Менее 0,7 мм
| От 0,7 до 1,5 мм
|
ВОСВ
ОСВ
СВ
|
| 250-350
250-350
250-380
|
|
| 2. Прокат тонколистовой холоднокатаный и холоднокатаный горячеоцинкованный с полимерным покрытием с непрерывных линий
h =0,35-1,5мм
B от 900 до 1250мм.
| ГОСТ Р 52146-2003
| Механические свойства при способности к вытяжке СВ - по
ГОСТ 9045-93, при способности к вытяжке ВГ, Г, Н – по ГОСТ 14918-80.
|
| Покрытие двустороннее грунтом и одностороннее полиэфирной эмалью ПЭ. Толщина покрытия, мкм
| Грунт
| Полиэфирная эмаль
| 5-7
| 20-30
| 3.Прокат листовой горячеоцинкованный, h =0,30-1,5мм
B от 900 до 1250мм
| ГОСТ Р 52246-2004
| Марка проката
| sв, МПа не менее
| sТ, МПа не менее
| d4, %, не менее при h
|
| Менее 0,7 мм
| От 0,7 мм
|
| -
270-500
270-420
| -
-
-
| -
| -
| Масса двухстороннего покрытия m, г/м2,
| От 60 до 350
| Всего
|
|
| | | | | | | | | | | | |
Выбор расчетных профилей.
Расчетные профили выбираются из сортамента, и по условиям их обработки определяют технологию и характеристику оборудования (основные параметры): установленную мощность, номинальную скорость и пределы ее регулирования, производительность, нормы расхода ресурсов и услуг, себестоимость и приведенные затраты. При этом определяющее внимание на параметры оборудования оказывает не только выбор профилей, но и соотношение между объемами их производства.
Выбор расчетных профилей основан на следующих положениях:
- среди расчетных представлены профили со средними, максимальными и минимальными характеристиками - размерами, объемами обработки;
- средние профили являются представительными, т.е. доля в сортаменте представляемых реальных профилей значительна;
- расчетному профилю приписывается не собственная доля в сортаменте, а доля представляемой группы.
Расчетные профили выбираются из сортамента обрабатывающих фаз, по условиям обработки которых определяют технологию и характеристики процесса обработки (основные параметры): мощность, производительность, нормы расхода ресурсов и услуг, себестоимость и приведенные затраты [6,7].
Для проектирования по ГОСТ 9045-93 выберем сталь марки 08Ю размером 0,60х1250 мм со следующими условиями поставки:
- отгрузка в рулонах;
- I группа качества отделки поверхности;
- 5 категория по нормирующим характеристикам;
- способность к вытяжке – ВОСВ;
- состояние поверхности матовое (шероховатость Ra=0,6-1,6);
- обрезная кромка – О;
- в части сортамента прокат должен соответствовать требованиям ГОСТ 19904-97.
Механические свойства расчетного профиля по ГОСТ 9045-93:
- способность к вытяжке – ВОСВ;
- предел текучести неболее - 185 МПа;
- временное сопротивление разрыву – 250-350 МПа;
- относительное удлинение не менее - 38;
- твердость (HRT15) не более – 76.
Для проектирования по ГОСТ 52246-2004выберем сталь марки 08пс размером 0,35х1220 мм со следующими условиями поставки:
- отгрузка в рулонах,
- прокат с цинковым покрытием;
- марка 03 – для весьма глубокой вытяжки и сложных профилей;
- повышенной точности – категории А;
- с не обрезной кромкой – НО
- класс цинкового покрытия - 140;
- с минимальным узором кристаллизации дрессированное – МД;
- пассивированный – ПС.
Для проектирования по ГОСТ 52146-2003 выберем сталь марки 08пс размером 0,50×1250 мм и установим для неё условия поставки:
- отгрузка в рулонах;
- прокат тонколистовой холоднокатаный горячеоцинкованный;
- лакокрасочное покрытие холоднокатаного горячеоцинкованного
проката (ЛКПОЦ);
- одностороннее покрытие;
- весьма глубокая вытяжка основы – ВГ;
- с необрезной кромкой – НО.
Для получения требуемого качества готовой продукции, а также, исходя из технических возможностей цеха со станом горячей прокатки, норм расхода металла на обрезку, выбираются суммарные обжатия при холодной прокатке и соответствующие им размеры подкатов.
Ширина подката выбирается с учётом обрезки кромок и концов полос на непрерывном травильном агрегате и на агрегатах резки. Обрезка кромок в непрерывном травильном агрегате по данным [4] для подката толщиной до 2,5 мм составляет мм, а для более толстого мм. Обрезка кромок на агрегатах резки: для проката, подвергающегося отжигу в колпаковых печах, принимается мм, ввиду травмирования кромок.
Суммарное обжатие при холодной прокатке углеродистых и низколегированных конструкционных сталей в большинстве случаев находится в пределах 70-80%.
На основании выбранных суммарных обжатий определяем толщину подката по следующей формуле [7]:
где h – толщина готовой полосы, мм; e - суммарное обжатие.
Расчетные профили для продукции проектируемого цеха представлены ниже в таблице 5.
Таблица 5. Расчетные профили.
Вид продукции по заданию
| Типоразмер, мм
| Толщина подката, мм
| Суммарное обжатие, %
| 1. Прокат холоднокатаный из углеродистой качественной стали общего назначения марки 08Ю.
| 0,60/1250
| 2,7
| 78%
| 2. Прокат холоднокатанный горячеоцинкованный из стали марки 08пс.
| 0,35/1220
| 1,8
| 80%
| 3. . Прокат холоднокатанный горячеоцинкованный с полимерным покрытием из стали марки 08пс.
| 0,50/1250
| 2,3
| 78%
|
Информационный поиск
Для производства холоднокатаной листовой стали в зависимости от её марки и назначения применяют различные схемы технологического процесса, которые характерны только для данного вида проката, а цехи часто именуются по их специализации (цехи углеродистых сталей, динамной стали, жести и др.). Тем не менее для всех цехов холодной прокатки листа имеются общие для всех технологические операции: удаление окалины с поверхности горячекатаной полосы, прокатка, термическая обработка полосы, отделка готового проката, упаковка и отгрузка.
Исходным материалом для производства холоднокатаной листовой стали является полоса (толщиной 1,8-6,0 мм), полученная на полунепрерывных или непрерывных станах горячей прокатки.
Наиболее существенным изменением в комплексе НТА-НСХП, следует считать создание совмещенных линий «травление-прокатка». Совмещение в единый комплекс НТА и НСХП возникло в начале 90-х годов прошлого века. На конец 1999 г. из действовавших в мире более чем 200 НСХП около 70 из них совмещены с НТА. Причем чаще всего совмещенные линии НТА НСХП создают на уже действующих НСХП путем их реконструкции [6].
На предприятиях фирм «Arcelor Sidmar», «Тhyssen Krupp Steel» и «VOEST-Alpine» объединение агрегатов сопровождалось модернизацией оборудования как на НТА, так и на НСХП.
Поскольку расположение НТА и НСХП не меняли, то схемы их соединения между собой различаются. Лишь на одном предприятии удалось объединить НТА и НСХП без поворота движения полосы, а в остальных комплексах их пришлось применить один, два и даже три раза. Наиболее сложная схема комплексе (с тремя поворотами движения полосы) — на заводе фирмы «ФЕСТ-Альпине Шталь». Головная часть объединенного комплекса аналогична головной части НТА, включая входное накопительное устройство. Далее следует устройство правки полос растяжением, с помощью которого правят плоскостность полос и одновременно разрушают окалину. Из этого устройства полоса поступает в традиционные травильные и промывочные ванны и в сушильное устройство. Промежуточное петлевое накопительное устройство предназначено как для накопления запаса полосы перед НСХП.
После промежуточного накопителя полоса поступает в выходной накопитель, расположенный непосредственно перед НСХП. Наличие двух петлевых накопителей (промежуточного и выходного)необходимо для создания запаса полосы, обеспечивающего стабильную работу комплекса даже в случае аварийных или плановых кратковременных остановок (например, на перевалку валков) НСХП.
За выходным накопителем расположена натяжная станция, обеспечивающая стабильное натяжение полосы на входе в НСХП. На НСХП установлена новая клеть, диаметры рабочих валков которой на 20% меньше, чем не прежних клетях, оборудованная осевой сдвижкой и системой противоизгиба рабочих валков, а также их секционным охлаждением. Далее следует традиционная прокатка и смотка холоднокатаных полос.
В результате авторы работы [6] делают заключение, что реконструкции, проведенные фирмами «Axcclor Sidmar», «Thyssen Krupp Steeb и «VOEST-Alpine Stahl», позволили получить высококачественный прокат и снизить себестоимость продукции.
Еще одним примером строительства нового НСХП 1700, совмещенного с НТА, может служить комплекс на заводе фирмы «Tata Steel». Оборудование стана изготовлено фирмой «Hitachi». Стан введен в эксплуатацию в 2000 г. и предназначен для прокатки полос толщиной 0,25-2,54 и шириной 800-1580 мм из низкоуглеродистой стали и стали IF с защитными покрытиями. Стан пятиклетевой, все клети шестивалковые с осевой сдвижкой промежуточных валков.
Диаметры валков: рабочих 425, промежуточных 490, опорных 1300 мм, длина бочки 1700 мм. Максимальная скорость прокатки на НСХП 20 м/с, максимальная скорость движения полосы в ванне травления 3 м/с.
Схема размещения оборудования на головном участке НТА традиционна. Травильная ванна секционная (4 секции). Особенность комплекса — строгое регулирование натяжения полосы в среднем и выходном петлеобразователях и на входном участке НСХП, которое создается регулятором натяжения с помощью роликови поддерживается в заданном режиме трехроликовым устройством.
Магнитогорский металлургический комбинат (ММК) в 2011 году ввел в эксплуатацию стан 2000 для холодной прокатки металла. Это оборудование является на сегодня уникальным для России и включает непрерывную линию, обеспечивающую турбулентное травление металла в соляной кислоте, и пятиклетевой стан, имеющий производительность до 2,3 миллиона тонн металла в год. Сортаментом выпускаемой продукции является холоднокатаный лист в рулонах массой до 43,5 тонн, толщиной полосы 0,28-3,0 мм и шириной 850-1880 мм [6].
В 1984 году фирма МДЗ «Маннесман Демаг Зак Гмбх» разработала технологию травления полос в турбулентном потоке, являющуюся развитием идеи травления в плоских ваннах. Отсек травления в турбулентном потоке выполнен в виде горизонтального канала, размещенного в травильной ванне. Верхнее перекрытие канала исключает свободную поверхность испарения кислоты. Создание турбулентного потока осуществляется с каждой стороны входа и выхода каждого отсека травильной ванны. При этом устройства для создания турбулентного потока служат одновременно в качестве динамического уплотнения для кислоты. Отработанная кислота через боковые спускные каналы, расположенные по обе стороны от турбулентной камеры, поступает в спускные камеры на входе и выходе из отсека. Туда же поступают дренажные стоки от динамического уплотнения турбулентной камеры. Отсюда кислота самотеком возвращается в сборник. Между сборником кислоты для каждого из отсеков ванны осуществляется каскадная циркуляция растворов. Турбулентное травление является наиболее перспективным при создании совмещенных линий, такие как НТА-СХП.
Современная металлургия стремится к повышению объемов производства, улучшению качества продукции в соответствии с растущими требованиями потребителей, уменьшению обслуживающего персонала и травильно-прокатный агрегат полностью соответствует этим тенденциям.
В результате создания объединенных комплексов НТА - НСХП и выполненной на них модернизации достигнуто:
- повышение производительности на 20-50%;
- снижение обрези на концах полос;
- снижение брака по дефектам, возникающим при заправке и выходе полосы из валков НСХП с 1,4 до 0,45%;
- уменьшение числа перевалок и перешлифовок валков на 45%, а следовательно, и парка валков;
- снижение численности обслуживающего персонала на участке травления и прокатки на 30-50%;
- уменьшение расходов на ремонты на 25%;
- сокращение длительности цикла производства продукции до двух суток. Отмечено также улучшение качества продукции, условий труда и сокращение числа несчастных случаев.
К этому следует добавить, что при объединении НТА и НСХП существенно снижается площадь, занимаемая цехом, за счет промежуточных складов, которые были необходимы для хранения протравленных рулонов, снижается число крановых операций по снятию травленых рулонов с НТА, транспортировке их на склад и со склада к НСХП, а главное, устраняется трудоемкая операция заправки полосы в стан [6].
Обзор показывает, что общее мировое направление усовершенствования оборудования для производства холоднокатаного металла – это объединение оборудования в единый комплекс, что позволяет значительно увеличить качество продукции и производительность, при этом существенно уменьшая производственные затраты на его эксплуатацию. Поэтому в данной работе считаю необходимым рассмотреть объединенный травильно-прокатный агрегат как наиболее перспективный.
Для снятия наклепа, получения необходимых структур и свойств металл после холодной прокатки подвергают рекристаллизационному светлому отжигу в колпаковых печах или проходных печах. Режим отжига зависит от химического состава и чистоты металла, структуры металла горячекатаной полосы и степени холодной деформации. Высокие пластические свойства низкоуглеродистой стали можно достичь рекристаллизацией и перерекристаллизацией холоднокатаной стали. Интенсивность и завершенность этих процессов определяются скоростью нагрева, температурой рекристаллизации, продолжительностью выдержки при этой температуре и скоростью охлаждения [7].
Для подавляющего большинства сталей оптимальные условия рекристаллизации соответствуют низкотемпературному отжигу в интервале температур собирательной рекристаллизации от 580 – 590 °С до точки Режим отжига характеризуется медленным нагревом 10 – 35 °С/ч до температуры рекристаллизации 650 – 720 °С, выдержкой при данной температуре в течении 12 – 22 ч для выравнивания температуры по сечению рулона и длительным охлаждением 5 – 15 °С/ч [7].
На неподвижном стенде устанавливается стопа из 3 – 5 рулонов, которая накрывается муфелем, изготовленным из жаропрочной стали. Внизу муфель герметизируется резиновым уплотнителем. Нагрев рулонов осуществляется с помощью переносного колпака, в нижней части которого по периметру расположены горелки. Колпак футерован легковесным огнеупорным кирпичом. Топливом для горелок служит природный или смеси коксового и доменного газа с теплотой сгорания 35,7и 6,7 МДж/м2 соответственно. Продукты сгорания омывают муфель, нагревают его и через дымовые окна отсасываются эжектором. Перед нагревом подмуфельное пространство, где расположены рулоны, заполняется защитным (нейтральным) газом, в качестве которого используется водород. Защитный газ предотвращает окисление поверхности металла при нагреве.
С целью выравнивания температуры металла по высоте стопы и ускорения процесса нагрева вентилятором осуществляется принудительная циркуляция защитного газа в подмуфельном пространстве. Для прохождения газа между рулонами устанавливаются конвекторные (ребристые) прокладки.
Сокращение площадей термоотделения, количества незавершенной про- дукции, цикла обработки при обеспечении равномерности свойств дости- гается использованием агрегатов непрерывного отжига. Проходные печи башенного и горизонтального типа начали применять в 40-х годах для от- жига жести. Полоса подвергалась ускоренному нагреву до 720 — 730 °С, выдержке, замедленному до 500 °С и ускоренному охлаждению до 120- 180 °С в атмосфере защитного газа и окончательному охлаждению воз- духом до 60°С. При продолжительности отжига менее 100 с получали по- лосу с равномерными свойствами по длине. Однако температурно-ско- ростной режим отжига не был отработан для сталей, предназначенных для глубокой вытяжки, и не обеспечивал ее получения.
Основное назначение установленного в цехе холодной прокатки угле- родистых сталей агрегата непрерывного отжига — термообработка холоднокатаных полос в режиме обезуглероживания, рекристаллизации и комбинированного отжига, получение рулонов различной вытяжки, СВ, ОСВ, повышенными требованиями к отдел- ке поверхности по ГОСТ 9045 — 93, а также получение конструкционной высокопрочной листовой холоднокатаной стали с временным сопротив- лением до 650 МПа [7].
После отжига металл подвергается дрессировке. Дрессировка — это небольшое (3 — 5%) обжатие полосы на дрессиро- вочном стане. Он представляет собой одноклетевой стан кварто с разматывате- лем и моталкой. Прокатка на нем осуществляется в один проход.
Основное технологи- ческое назначение дрессировки состоит в предотвращении появления линий скольжения при последующей штамповке изделий из отложенно- го металла. Для этого необходимо наклепать тонкие поверхностные слои полосы. Дрессированный металл при испытаниях на растяжение не имеет на кривой растяжения "площадки" и "зуба" текучести. Кроме того, дрес- сировка несколько снижает относительное удлинение и предел текучести, повышает твердость полосы [7].
Чтобы полу- чить определенную шероховатость листа, необходимо вести прокатку на вал- ках, имеющих шероховатость с несколько большим значением по показателю Ra . Рабочие валки дрессировочного стана первоначально шлифуют до зеркаль- ного блеска. Чтобы получить насеченные валки, необходимо на валках дрессировочного ста- на создать шероховатость до ≥ 4 мкм. Это осуществляется путем насечки валков на дробеметной машине за три-пять проходов [7].
В цехе холодной прокатки углеродистых сталей предусмотрено отделение покрытий, состоящее из агрега- тов горячего цинкования полос, электролитического цинкования и на- несения полимерных покрытий.
Главным свойством оцинкованного листа является его коррозионная стой- кость. Различают несколько разновидностей цинкосодержащих покрытий и методов их нанесения. Основным видом является двухстороннее покрытие из расплава цинка с одинаковым или разным по толщине покрытием с обеих сторон, а также лист с односторонним покрытием. Для экономии цинка, а также для улучшения коррозионной стойкости, свариваемости и других характеристик применяют покрытия в виде сплавов цинка с железом, с алюминием (гальвалюм), с полимерами (цинкрометалл).
1.3 Структура основного производства и загрузка цеха производственной программой
Структура основного производства. Состав оборудования цеха.
Технологические схемы основного производства.
Проектируемый цех состоит изследующих отделений: травильно-прокатного, термического, участка нанесения покрытий и участки отделки и отгрузки металла. Общая технологические схема производства представлена на рисунке 1.
h 9KnWvmzIGj9zPbFk326wJogdal0N5izlttNxFC20NS3LQmN6em6oPBRHi/BSbB7Wu5vtGE/l+0fx lhw2PL0iXl+NT4+gAo3h7xh+8QUdcmHauyNXXnUI98lcfgkIMSiJxYrYIyzmS9B5pv/z5z8AAAD/ /wMAUEsBAi0AFAAGAAgAAAAhALaDOJL+AAAA4QEAABMAAAAAAAAAAAAAAAAAAAAAAFtDb250ZW50 X1R5cGVzXS54bWxQSwECLQAUAAYACAAAACEAOP0h/9YAAACUAQAACwAAAAAAAAAAAAAAAAAvAQAA X3JlbHMvLnJlbHNQSwECLQAUAAYACAAAACEAEkb7+2kCAACEBAAADgAAAAAAAAAAAAAAAAAuAgAA ZHJzL2Uyb0RvYy54bWxQSwECLQAUAAYACAAAACEAiYCw690AAAAHAQAADwAAAAAAAAAAAAAAAADD BAAAZHJzL2Rvd25yZXYueG1sUEsFBgAAAAAEAAQA8wAAAM0FAAAAAA== " adj="-218687,-1,-218687"> Травление и прокатка на травильно-прокатном агрегате
| Обработка на агрегате продольной резки
| Склад горячекатаных рулонов
| Нанесение цинкового покрытия в линии АНГЦ
покрытия
| Нанесение полимерного покрытия в линии АПП
| Упаковка и отгрузка готовой продукции
|
Рисунок 1. Общая технологическая схема производства.
Схема 1. Производство низкоуглеродистой качественной стали.
1. Очистка от окалины горячекатаных полос на непрерывно-травильном агрегате и холодная прокатка горячекатаной травленой полосы на непрерывном пятиклетевом стане холодной прокатки.
2. Светлый отжиг холоднокатаных полос в колпаковых печах или отжиг в АНО.
3. Дрессировка холоднокатаных отожженных полос на одноклетьевом дрессировочном стане.
4. Подрезка кромок, упаковка рулонов на агрегатах резки.
5. Отгрузка потребителю готовой продукции.
Схема 2. Производство оцинкованной стали.
1. Очистка от окалины горячекатаных полос на непрерывно-травильном агрегате и холодная прокатка горячекатаной травленой полосы на непрерывном пятиклетевом стане холодной прокатки.
2. Обработка холоднокатаных полос в линии АНГЦ.
3. Упаковка и отгрузка потребителю готовой продукции.
Схема 3. Производство проката с полимерным покрытием.
Включает в себя все технологические операции, что и схема производства оцинкованной стали, только после нанесения цинкового покрытия в линии АНГЦ металл дополнительно проходит обработку на агрегате полимерного покрытия.
В состав цеха входят 4 отделения: травильно-прокатное, термическое отделения, отделение нанесения покрытий и отделение отделки.
В травильно-прокатном отделении располагается пятиклетевой травильно-прокатный агрегат (схема представлена на рисунке 2).
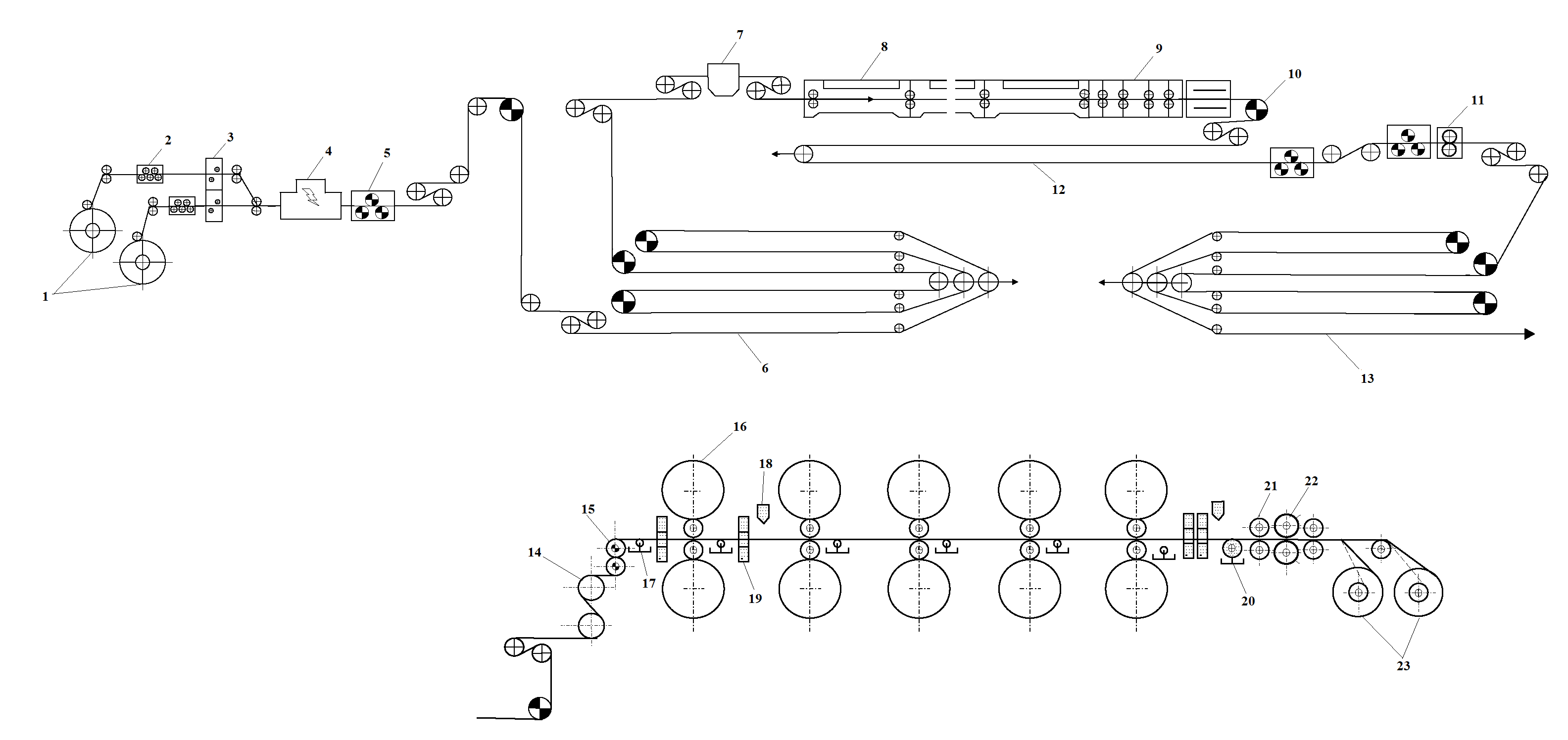
Рисунок 2. Схема непрерывно травильного агрегата совмещенного с 5-ти клетевым станом тандем: 1-разматыватель; 2-правильная машина; 3-ножницы; 4-сварочная машина; 5-направляющий блок роликов; 6-входной накопитель; 7-правильно растяжная машина; 8-травильные ванны; 9-сушильные камеры; 10-блок центрирующего ролика; 11-кромкообрезные ножницы; 12-промежуточный накопитель; 13-выходной накопитель; 14-управляющая станция; 15-натяжная станция; 16-прокатная клеть; 17-измеритель натяжения; 18-измеритель скорости; 19-измеритель толщины и профиля; 20-измеритель планшетности; 21-тянущие ролики; 22-барабанные ножницы; 23-моталки.
Травильная часть агрегата состоит из: двух разматывателей, автоматической стыкосварочной машины, входного петлевого устройства, машины правки растяжением, ванны травления и ванны промывки, сушильного устройства, выходного петлевого накопителя, дисковых ножей.
Прокатное оборудование стана: пять прокатных четырехвалковых клетей; гидравлические нажимные устройства; комплекты рабочих и опорных валков; эмульсионные коллекторы; цилиндры изгиба рабочих валков; главные приводы клетей; две моталки и барабанные ножницы.
Исходной заготовкой служат горячекатаные полосы. Размеры исходных рулонов: внутренний диаметр -750±5 мм, максимальный наружный диаметр – 2000 мм, масса рулона не более 30 т. Размеры исходных полос: толщина 1,5 – 4,5 мм, ширина – 900 – 1280 мм. Максимальная скорость прокатки 20 м/с.
Термическое отделение состоит из колпаковых печей, одного агрегата непрерывного отжига и дрессировочного стана.
Составными частями колпаковой печи являются: стенд, нагревательный колпак, муфель. Основные параметры одностопной водородной колпаковой печи «Эбнер» представлены в таблице 6.
Таблица 6. Техническая характеристика водородной колпаковой печи «Эбнер»
Наименование
| Величина
| Температура отжига, °С
| 650-710
| Время нагрева садки, ч
Время охлождения садки, ч
|
| Размеры садки, мм: диаметр
высота
|
| Масса садки (средняя), т
|
| Производительность стенда, т/ч:
| 1,05 – 1,20
| Топливо
| Природный газ
| Защитный газ
- состав, %
| водород
75% Н2; 25% N2 или 100% Н2
|
На дрессировку поступает металл после отжига в колпаковых печах. В состав оборудования дрессировочного стана входят: разматыватель, ножницы, S роликовая клеть, для создания натяжения между разматывателем, S – роликами и клетью, дрессировочная клеть, гидронажимные устройства, комплекты валков, устройство для смены валков, ножницы, S – роликовая клеть, для создания натяжения полосы между клетью и S – роликами, S – роликами и моталкой, стрессометрический ролик, моталка со сталкивателем и ременный захлестыватель.
Агрегат непpеpывного отжига. Назначение: термическая обработка холоднокатаных полос в режиме обезуглероживания, рекристаллизации, комбинированного отжига, обезуглероживания-рекристаллизации.
Размеры исходных полос:
- толщина от 0,35 до 1,00 мм;
- ширина от 700 до 1250 мм.
Размеры исходных рулонов:
- диаметр наружный от 1050 до 2300 мм,
- диаметр внутренний 600 мм.
Масса рулона - до 30 т.
Скорость транспортировки полосы на входном участке:
- максимальная до 100 м/мин,
- заправочная 30 м/мин.
Максимальная скорость полосы в печи 75 м/мин.
Максимальная скорость на выходном участке 100 м/мин.
Печь для отжига имеет две камеры нагрева, две камеры выдержки, камеру регулируемого охлаждения, камеру струйного охлаждения и воздушный холодильник.
Первая камера нагрева разделена на 4 зоны регулирования (длина камеры 32,85м).
Первая камера выдержки разделена на 9 зон регулирования (длина камеры 160,0 м).
Вторая камера нагрева - одна зона регулирования (длина камеры 10,8 м). Между первой камерой выдержки и второй камерой нагрева имеется разделительный тамбур длиной 2,3 м.
Вторая камера выдержки разделена на 3 зоны регулирования (длина камеры 25,2 м).
Камера регулируемого охлаждения имеет длину 13,7 м. Охлаждение осуществляется косвенным методом с помощью труб воздушного охлаждения. Между камерой регулируемого охлаждения и второй камерой выдержки имеется разделительный тамбур длиной 2,3 м.
Камера струйного охлаждения обеспечивает охлаждение за счет подачи азота вентиляторами (длина камеры 13,3 м).
Печь имеет 5 газовых свечей.
Две основные свечи установлены на входе первой и второй камеры нагрева.
Три продувочные свечи установлены на входе и в первую и во вторую камеры нагрева, на входе в камеру охлаждения.
Азото-водородный газ, подаваемый в первые камеры нагрева и выдержки может увлажняться в пяти увлажнителях.
Азото-водородный газ, подаваемый во вторые камеры нагрева и выдержки может увлажняться увлажняется в трех дополнительных увлажнителях.
Сухой азото-водородный газ, подается в камеры с помощью перфорированных труб.
Максимальная температура нагрева полосы - 850 0С.
Максимальный расход защитной атмосферы.
Сухой газ (от 7 до 15 % H2) до 300 м3/ч.
Сухой азот до 365 м3/ч.
Камера нагрева и выдержки разделена на 9 зон регулирования (длина камеры 43 м). Максимальная температура полосы 650 0С.
Камера охлаждения - длина 15,0 м.
|