Основными материально-техническими ресурсами
Для обеспечения беспрерывной работы специализированных потоков по строительству покрытия производственные предприятия выпускают смеси по специальному календарному графику (рис. 3). Сроки работы конкретного производственного предприятия должны быть увязаны со сроками строительства асфальтобетонных и цементобетонных покрытий. Построению календарного графика предшествует работа по определению производительности производственных предприятий, см. формулы (2), (3), (4).
Для построения календарного графика определяют сменный выпуск смеси на АБЗ или ЦБЗ, а также сменный и месячный расходы основных материалов для их производства по форме № 6 и 7 (на примере выпуска асфальтобетонной смеси).
Форма № 6
Ведомость потребности материалов для приготовления смеси
Вид смеси
| Материал
для приготовления смеси
| Сменный выпуск смеси, т
| Потребность материала для приготовления смеси
| в долях по массе
| на 1 т, т
| на 1 смену, т
|
|
|
|
|
|
|
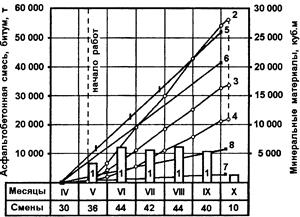
Рис. 3. Календарный график выпуска асфальтобетонной смеси
и заготовки материалов:
1 - месячный выпуск смеси; 2 - общий выпуск асфальтобетонной смеси;
3 -выпуск смеси для нижнего слоя покрытия;
4 - выпуск смеси для верхнего слоя покрытия;
5 - заготовка щебня; 6 - заготовка песка; 7 - заготовка минерального порошка;
8 - заготовка битума (пунктиром обозначены сроки начала
и окончания выпуска смеси)
Форма № 7
Ведомость месячной потребности в материалах
Для приготовления смеси в продолжении строительного сезона
Вид смеси
| Месяц
| Число
рабочих смен
в месяце
| Месячный выпуск смеси, т
| Месячная потребность в материале
для приготовления смеси
| щебень, м3
| песок, м3
| минеральный порошок, т
| битум, т
|
| май
|
|
|
|
|
|
|
| июнь
|
|
|
|
|
|
|
| июль
|
|
|
|
|
|
|
| август
|
|
|
|
|
|
|
| сентябрь
|
|
|
|
|
|
|
| октябрь
|
|
|
|
|
|
|
Раздел 6. Определение складских
Территорий и емкостей
Для единовременного хранения
Исходных материалов и сырья
Общие требования
При проектировании складов каменных материалов должно быть обеспечено выполнение следующих требований:
· прием каменных материалов из железнодорожных вагонов и автотранспорта в любое время года;
· продолжительность разгрузки вагонов любых типов в сроки, установленные МПС (обычно двенадцать 60-тонных вагонов за 1 ч. 20 мин.);
· раздельный прием и выдача каменных материалов различных фракций (без ухудшения их качества);
· механизация трудоемких работ (открывание и закрывание люков, очистка и перемещение вагонов, а в осенне-зимний период рыхление смерзшихся материалов);
· создание безопасных и нормальных условий работы обслуживающего персонала.
При проектировании складов цемента и минерального порошка должно быть обеспечено выполнение следующих требований:
· создание возможности приема цемента в нормативные сроки из всех транспортных средств (железнодорожных вагонов и автоцементовозов);
· размещение складов вблизи бетоносмесительного (асфальтосмесительного) отделения ЦБЗ (АБЗ) на оптимальном расстоянии от компрессорной станции;
· обеспечение транспортного подъезда к силосным емкостям;
· возможность дальнейшего расширения склада путем пристройки дополнительных силосов;
· раздельное хранение цемента по видам и маркам;
· применение для транспортирования порошкообразных материалов средств пневмотранспорта;
· предотвращение снижения активности цемента.
При организации складского хозяйства решают следующие основные вопросы:
· определяют запасы единовременного хранения материалов на складе;
· высчитывают площади и объемы складов, определяют их размеры и длину погрузо-разгрузочных фронтов;
· производят выбор способов выгрузки материалов из транспортных средств и подачи их к местам переработки;
· определяют способы хранения материалов и выбирают необходимое технологическое оборудование.
Запасы единовременного хранения материалов должны обеспечить бесперебойную работу предприятия. Величина их зависит от местных условий и вида транспорта. В курсовой работе можно принять следующие нормы запаса: битума – на 25-30 сут.; цемента и минерального порошка – на 20-25 сут.; щебня, гравия и песка – на 7-10 сут.
Для хранения цемента и минерального порошка на АБЗ и ЦБЗ наибольшее применение находят склады силосного типа, основные технические данные которых приведены в прил. 5.
Насыпные и навалочные материалы (песок, щебень) обычно хранят на открытых площадках в виде штабелей различной геометрической формы (призмы, пирамиды, конусы). Их геометрические размеры (длину, ширину, диаметр) определяют, исходя из заданной высоты отсыпки и угла естественного откоса отсыпаемого материала.
Типовые склады минеральных материалов различной вместимости разными способами их загрузки и транспортное оборудование приведены в прил. 5.
Склады каменных материалов
В настоящее время разработан ряд проектов складов каменных материалов различных типов вместимостью от 9 до 100 тыс. м3 [10], предназначенных для АБЗ и ЦБЗ дорожного строительства.
На прирельсовых АБЗ и ЦБЗ получили распространение склады каменных материалов с приемными устройствами в виде подрельсовых бункеров с радиально-штабелирующими конвейерами (РШК), с использованием самоходного разгрузчика ТР-2А, повышенного пути на железобетонной эстакаде.
Широкое применение повышенных путей для разгрузки каменных материалов объясняется простотой строительных конструкций склада и отсутствием технологического оборудования. Главное преимущество склада каменных материалов с повышенными путями – значительный фронт разгрузки, позволяющий одновременно разгружать несколько вагонов, увеличивая количество разгрузочных бригад. Однако при разгрузке каменных материалов происходит их смешивание, что вызывает необходимость дорогостоящей сортировки. Кроме того, большая протяженность склада (300-500 м) и разгрузка каменных материалов на обе стороны от железной дороги приводит к усложнению технологических процессов складской переработки, увеличению площади покрытия, используемой под склад, а также значительному увеличению длины подземных галерей или к использованию дефицитного технологического транспорта для погрузо-разгрузочных работ.
На складах каменных материалов осуществляется два основных технологических процесса: подача каменных материалов на склад, их выдача со склада в расходные бункеры смесительных установок или в транспортные средства.
Для подачи каменных материалов со склада наиболее целесообразно использовать пневмоколесные одноковшовые фронтальные погрузчики.
Склады с подрельсовыми бункерами и РШК имеют следующие преимущества:
· дают возможность оборудовать приемные устройства приспособлениями для рыхления каменных материалов, виброзачистки и закрывания люков полувагонов, наиболее удобные и безопасные в работе;
· позволяют механизировать и частично автоматизировать технологические процессы погрузки, складской переработки каменных материалов;
· обеспечивают четкое складирование материалов по видам и размерам с максимальным сохранением их качества, поскольку работы по перемещению щебня бульдозером сведены до минимума;
· размещаются на сравнительно небольших площадях благодаря высоким (до 20 м) и компактным штабелям;
· могут быть перебазированы в короткие сроки при значительных сокращениях бросовых работ и уменьшении трудовых затрат.
Выбор типа склада
Критериями оценки складов каменных материалов являются: расчетная вместимость, коэффициент использования, производительность по разгрузке вагонов, эксплуатационные расходы по объему, капитальные вложения, степень инвентарности.
Методика проектирования
Исходными данными для проектирования является расход каменных материалов, необходимых для обеспечения строительства проектируемого участка дороги. Зная вид выпускаемой асфальтобетонной или цементобетонной смеси, можно определить расход фракций щебня и песка в соответствии с разд. 4 и 5. Полученные данные необходимо занести в таблицу, составленную по форме № 8.
Форма № 8
|