Основные причины отказов, связанные с технологией изготовления изделий В настоящее время принято отказы, связанные с технологией изготовления изделия, классифицировать в соответствии со схемой [1,3], представленной на рисунке 11.
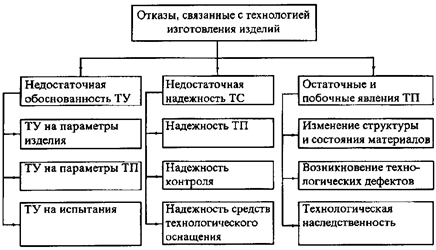
Рисунок 11 - Классификация отказов, связанных с технологией изготовления изделия
Первая группа причин связана с недостаточной обоснованностью технических условий на параметры изделия и его составляющие, на параметры технологических процессов и методы испытания на надежность изделия и его составляющих.
Технические условия на изделие и его составляющие должны отражать основные требования к надежности изделия. Но при выполнении технологических операций по изготовлению деталей и их последующей сборке измеряются не показатели надежности изделия, которые практически и невозможно измерить на данном этапе технологического процесса. Поэтому в чертежах задаются параметры, удобные для измерения и которые должны были бы однозначно обеспечить требуемый уровень надежности изделия. Однако, параметры чертежей по точности, допускам и шероховатости и твердости, оказывается, еще не определяют однозначно показатели надежности. Даже более жесткая регламентация технологического процесса с ссылками на соответствующие технологические инструкции, ОСТы и ГОСТы часто также не обеспечивает одинаковые показатели надежности изделий, изготовленных на разных предприятиях. Поэтому чем выше требования к надежности изделия, тем большее число параметров должно быть оговорено техническими условиями и тем достовернее должны быть определены основные взаимосвязи между эксплуатационными и технологическими параметрами (58). Практически же такие вопросы решаются в процессах доводки изделий на стадии серийного производства (п.2). В результате такой доводки происходит жесткая регламентация не только технологического процесса, а всей технологической системы конкретного производства, обеспечивающей необходимый уровень надежности изделий. При этом очень важную роль играют заданные технические условия на испытания. Сложность разработки методов и средств испытаний изделий на надежность привели к тому, что испытания стали самостоятельной областью в проблеме надежности.
Таким образом, обоснованность технических условий для обеспечения заданного уровня надежности изделий связана не только с техническими условиями на изделие, на технологический процесс и на испытания, но и с жесткой регламентацией всей технологической системы (в том числе и технологического процесса) изготовления и испытания изделий.
Следующая группа, приводящая к отказам по вине технологии, связана с остаточными и побочными явлениями технологических процессов.
При выполнении любой технологической операции материалы деталей подвергаются очень значительным силовым, тепловым, химическим и другим воздействиям. Уровень этих воздействий во много раз превышает уровень воздействий при эксплуатации изделий и создает объективные условия для возникновения в изделиях таких нежелательных воздействий, как изменение свойств и структуры материалов, образование пор, раковин, трещин и микротрещин. Особенно высоко такое воздействие на приповерхностный слой материала детали. В общем случае к технологическим дефектам относят любые несоответствия продукции требованиям, установленным нормативно-технической документацией. Поэтому к дефектам относят как отклонения свойств и состояний материалов (трещины, раковины, включения, структурные изменения, выход параметра качества за пределы допуска и т.д.), так и нарушения заданной точности формы и размеров. Обычно дефекты формы и размеров рассматривают отдельно как погрешности обработки, а к дефектам относят все остальные нарушения установленных требований к материалу и приповерхностным слоям.
Образование дефектов в изделии зависит от применяемого технологического метода, средств технологического оснащения, режимов обработки, систем автоматизации процесса и других характеристик. Для каждой технологической операции имеются, как правило, типичные виды дефектов, связанные как с нарушением хода процесса, так и с неблагоприятным сочетанием различных факторов при его выполнении.
Например, при отливке деталей из-за неравномерного остывания, окисления, попадания в материал различных включений и газа, могут появляться дефекты в виде трещин, раковин, пор, ликвации и неоднородности структуры. Кроме того, возникают остаточные напряжения, которые могут приводить к снижению эксплуатационных показателей деталей, а также к их короблению, как при последующей обработке, так и в процессе эксплуатации. Аналогичные дефекты возникают при сварке, термической и химико-термической обработке, нанесении покрытий.
Особое влияние на работоспособность изделий оказывает механическая и электрохимическая обработка, которая придает деталям окончательную форму и свойства рабочим поверхностям деталей. В результате такой обработки поверхность материала и приповерхностные слои переходят в особое состояние с комплексом свойств, существенно отличающимся от свойств материала в объеме детали.
Часто различные варианты технологии, приводящие к одинаковым, с точки зрения регламентированного качества параметра, результатам, при более глубоком изучении обнаруживают разные склонности к образованию дефектов. Так, шлифование, полирование и алмазное выглаживание позволяют получить одинаковую величину шероховатости поверхности, однако шлифованная поверхность имеет большее число рисок глубиной до 1 мкм, полированная существенно меньшее число рисок с глубиной до 0,05 мкм, а выглаженная -практически не имеет рисок, а радиусы скругленяи выступов и впадин шероховатости в этих методах отличаются до сотен раз. Это приводит к существенному отличию в таких эксплуатационных свойствах, как выносливость, износостойкость и коррозионная стойкость.
У никелевых и титановых сплавов после электрохимической полировки существенно снижается предел выносливости по сравнению с деталями после механической обработки с теми же параметрами шероховатости поверхности. Более того, на 10... 15% снижается предел прочности на растяжение и загиб, в то же время предел прочности на сжатие и кручение практически не изменяется. Снятие же припуска после электрохимической обработки механическим методом (от 0,15 до 0,3 мм) восстанавливает величины этих параметров. У ряда алюминиевых сплавов механическая и электрохимическая обработка незначительно изменяет значения пределов выносливости и прочности.
В пределах одного технологического метода на возможность возникновения дефектов основное влияние оказывают обычно выбранные средства технологического оснащения и режимы обработки. Например, широко известно, что в зависимости от режимов резания и геометрии режущего инструмента предел выносливости обрабатываемого материала может измениться более чем в два раза при практически одной и той же шероховатости поверхности. Еще более сильное влияние оказывает изменение режимов шлифования, особенно высокопрочных материалов.
Часто считают, что возникновение дефектов в процессе обработки является следствием нарушения технологической дисциплины, наличие оборудования с низкими техническими характеристиками, нарушение ритмичности работы предприятия, плохой организации труда и т.д. Такой взгляд является односторонним, так как фиксирует лишь грубые нарушения в ходе технологического процесса. Надо отметить, что по существующим данным 85% технологических дефектов связано с недостатками технологии, в основном из-за неправильного обоснования технологических систем, а только 15% являются следствием нарушения технологической дисциплины.
В действительности физико-химические воздействия, которые сопровождают любой технологический процесс, порождают в материале изделия отклонения от первоначального отклонения и изменение свойств материала. Выход этих отклонений (они существуют всегда) за установленные пределы и приводит к возникновению дефектов. Поэтому технологический процесс, бездефектный при одних требованиях к изделию, будет дефектным при повышенных нормативах на выходные параметры.
Хотя основную роль в формировании показателей качества выпускаемых изделий часто играют финишные операции технологического процесса, однако многие свойства передаются с промежуточных операций на последующие. Явление переноса свойств изделия от предыдущих операций к последующим получило название технологического наследования, а сохранение этих свойств -технологической наследственности [1,2,3]. Носителем информации о наследственности являются материал детали и её геометрическая форма.
Явный вид проявления отрицательной наследственности, связанный с отклонением геометрической формы детали от номинальной всегда может быть оперативно проконтролирован в технологическом процессе, а причины его возникновения и способы устранения достаточно хорошо известны в технологических подразделениях. Обычно геометрические поводки возникают в материале из-за перераспределения остаточных напряжений, наведённых в материале в ходе выполнения технологической операции, сразу при извлечении детали из закрепляющих технологических приспособлений, в которых проводилась эта операция. Однако такие поводки могут появляться постепенно в течение определённого времени по мере релаксации величины остаточных напряжений. В тоже время, латентное (скрытое) проявление отрицательной наследственности как, например, в случае снижения выносливости материала, неконтролируемое в ходе выполнения технологического процесса, оказывает значительное влияние на многие эксплуатационные характеристики и создает предпосылки для возникновения отказов изделий.
Физико-химическая природа возникновения многих видов латентной отрицательной наследственности получила убедительное объяснение в рамках кинетической теории прочности материалов [19] и связана с накоплением микроповреждений в материалах в ходе выполнения технологических процессов. Надо отметить, что основные положения этой теории успешно используются в расчётах конструкций на долговечность и остаточный ресурс при эксплуатационных воздействиях, в тоже время практически отсутствует использование этих положений при анализе влияния технологических воздействий на долговечность изготавливаемых изделий.
Основные положения этой теории, связанные с технологией, можно сформулировать следующим образом. В людом ненагруженном механическими усилиями материале из-за термофлуктуационного механизма протекают процессы разрыва и восстановления атомных связей в кристаллической решётке. В результате в любом материале при постоянной температуре устанавливается равновесная концентрация точечных дефектов, которая с ростом температуры быстро возрастает. При наложении на этот материал растягивающих напряжений, даже значительно меньших предела текучести, симметрия актов разрыва и восстановления атомных связей нарушается и в материале начитается процесс увеличения концентрации точечных дефектов. При их определённой концентрации начинается процесс коалесценции (слияния) точечных дефектов с образованием микроповреждений материала, количество и размер которых увеличиваются по мере действия растягивающей нагрузки. Следовательно, в обрабатываемых материалах даже вне зон действия значительных механических напряжений происходит латентное накопление микроповреждений, их объединение в субмикронные, а затем микротрещины, закритическое развитие которых ведёт к разрыву сплошности материала и его разрушению. Однако, обычно технологический процесс завершается на этапе латентного накопления определённой концентрации микроповредений, то есть возможные последствия этого в явном виде не проявляются на этапе производства.
В рамках кинетической теории прочности [19] материалов вводится понятие потенциальной долговечности материала τ(T, σ) как время до его разрушения при действии растягивающих напряжений, меньших предела его текучести. Установлено, что основной вклад в долговечность даёт период времени накопления микроповреждений (более 90%). Это послужило основанием для оценки времени гарантированной безотказности использовать величину потенциальной долговечности. Показано, что величина долговечности материала при постоянных растягивающих напряжениях σ<σs и постоянных температурах Т≤0,5Тпл (Тпл – температура плавления материала) определяется соотношением:
,
где величина U0равна энергии активации разрыва атомных связей в кристаллической решётке материала, τ0- период колебаний атомов, b- экспериментальная константа, зависящая от вида материала, технологии его получения и последующей обработки, но не зависящая от σ и Т, k-постоянная Больцмана. При прикладном применении этого соотношения обычно параметры τ0, U0и bопределяются из эксперимента.
В случае, когда величина σ и Т можно считать постоянными только в течение некоторого промежутка времени ∆ti, а также воздействия происходят в течение некоторого числа циклов N, гарантированный период безотказной работы материала tpопределяется из соотношения суммирования парциальных повреждений:
, (75)
где каждое слагаемое характеризует долю потерянной долговечности материала при каждом его нагружении.
Из соотношения (75) видно, что при изготовлении и эксплуатации изделия происходит парциальное повреждение материалов деталей и конструкций, из-за воздействия технологических и эксплуатационных факторов и, следовательно, происходит потеря определённой части потенциальной долговечности исходного материала. Причём, чем более жесткие условия обработки материалов и их дальнейшей эксплуатации, тем меньше величина остаточной долговечности материала.
Такая частичная потеря долговечности изделием отражается в широко известном факте наличия и постепенного увеличения количества микроповреждений и микротрещин докритического размера в материалах деталей эксплуатируемых изделий. При этом изделия с такими повреждениями могут иметь достаточно большие остаточные ресурсы безаварийной эксплуатации.
Понятие остаточный ресурс изделий, введенное на основе статистической обработки методами теории надежности экспериментальных данных по их эксплуатации, широко используется в современной технике. Кинетическая теория прочности дает физическое обоснование этого понятия.
Существенно реже понятие остаточной долговечности материалов используется для анализа технологических процессов изготовления изделий. Хотя очевидно, что в технологических процессах величина технологических факторов (напряжений и температур), воздействующих на материалы, значительно превышает величину этих же факторов, действующих на материалы при эксплуатации. Следовательно, при изготовлении изделия на каждом технологическом переходе происходит потеря потенциальной долговечности материала, из которого изготавливается деталь или элемент конструкции изделия. Это достаточно очевидное утверждение в рамках кинетической теории прочности материалов дает физическое обоснование одного из аспектов понятия о технологической наследственности в технологических операциях. Поэтому при недостаточно обоснованном выборе технологических методов и режимов обработки материалов такие потери потенциальной долговечности материалов бывают очень значительными, что приводит к необходимости назначения малых ресурсов эксплуатации изделий. Так, например, при изготовлении некоторых видов турбинных лопаток снижение предела их выносливости по сравнению с пределом выносливости исходных материалов может достигать 50% и более процентов, что снижает их потенциальную долговечность в сотни и тысячи раз из-за экспоненциальной взаимосвязи предела выносливости с долговечностью.
Надо отметить, что в настоящее время практически отсутствуют методы межоперационного контроля такой потери долговечности при выполнении технологических процессов. Разрабатываемые методы флюоресценции, ультразвукового контроля спектра колебаний и некоторые другие находятся только на стадии лабораторных испытаний. В основном используются методы контроля специальных образцов или деталей по определению в них распределения остаточных напряжений (косвенный метод) или по определению изменения предела их выносливости по сравнению с пределом выносливости исходных материалов. Однако эти методы обладают значительной трудоемкостью и требуют специального лабораторного оснащения.
Для восстановления долговечности материала после выполнения технологических операций используются некоторые технологические методы термообработки, приводящие к залечиванию микроповреждений и даже микротрещин, и методы поверхностного пластического деформирования (ППД) также частично залечивающие микроповреждения и создающие в опасных сечениях детали, сжимающие остаточные напряжения. Роль сжимающих остаточных напряжений в повышении долговечности материала связана с тем, что суммируясь с растягивающими напряжениями от внешних нагрузок они либо уменьшают действующие растягивающие напряжения, либо вообще зануляют их в соотношении (4.10). Однако, при наведении остаточных напряжений в материалах необходимо иметь в виду, что поле этих напряжений является самоуравновешенным. Следовательно, если в одних сечениях наводятся сжимающие остаточные напряжения, то в других сечениях всегда наводятся растягивающие, приводящие к снижению долговечности по этим сечениям. Поэтому при назначении методов ППД для повышения долговечности детали необходим также анализ отрицательных последствий применения этих методов.
Кинетическая теория прочности играет важную роль в обосновании ускоренных методов испытания материалов и изделий за счет ужесточения режимов испытания. Необходимость проведения ускоренных испытаний возникает тогда, когда требуется, например, назначить и подтвердить гарантированные ресурсы изделий, величина которых составляет годы или даже десятки лет. Очевидно, что проведение испытаний изделий в течение таких периодов времени, особенно для высокоответственных изделий, является фактически нереальной задачей.
В этом случае проводятся испытания изделия на долговечность при некоторых более высоких значениях температуры, чем температура эксплуатации изделия. Повышенные значения температуры выбираются таким образом, чтобы при этих температурах не происходило изменение свойств материалов испытываемого изделия.
Таким образом, кинетическая теория прочности материалов позволяет не только на более глубоком физико-химическом уровне понять сущность влияния эксплуатационных факторов на конструкционную прочность материалов, но и раскрывает физико-химическую природу влияния технологических методов, технологических факторов и режимов обработки на потенциальную долговечность изготавливаемых изделий и в определенной степени раскрывают сущность понятия «know how» технологических процессов.
Полученные на отдельных операциях дефекты (в том числе микротрещины) могут либо развиваться, либо залечиваться на последующих операциях. Поэтому технологическая наследственность может играть как положительную, так и отрицательную роль в зависимости от того, какие свойства сохраняются и передаются готовому изделию.
Технологическая наследственность в большинстве случаев оказывает все-таки отрицательное влияние на показатели качества и является побочным явлением при обработке деталей и их сборке. Поэтому необходимо технологический маршрут строить таким образом, чтобы исключить передачу дефекта или погрешности обработки с операции на операцию, сделать операции как бы независимыми в технологическом отношении. Считается, что наиболее благоприятным будет такой технологический процесс, где на начальных операциях происходит практически полная ликвидация отрицательных свойств и эти свойства не наследуются на финишных операциях.
Следующая группа причин, приводящая к недопустимым производственным отказам изделий, связана с недостаточной надежностью технологической системы изготовления изделия. Как было отмечено при анализе первой группы причин, в результате доводки (на стадии опытного или серийного производства) возникает необходимость в жесткой регламентации технологической системы производства изделия. Однако в процессе эксплуатации технологической системы её свойства изменяются и, более того, она сама, как любое техническое изделие, подвержена отказам. Следовательно, технологическая система должна характеризоваться таким важным свойством, как надежность, т.е. свойством сохранять во времени способность обеспечивать изготовление продукции в заданном объеме, с заданной производительностью и заданными параметрами качества. Чем выше заданная надежность изделия, тем выше должна быть надежность технологической системы.
Важной задачей обоснования и создания технологических систем производства ЛА является выявление наименее надежных элементов технологических систем (дающих наибольшие дисперсии показателей качества) и их совершенствование, а также сокращение числа элементов в системе, в том числе и за счет их кооперации.
На рисунке 12 представлена типовая схема повышения надежности технологической системы за счет создания обоснованных и полных технических условий на показатели качества деталей, сборочных единиц и изделия в целом. В связи с таким сильным влиянием надежности технологической системы на надежность изделия в последнее десятилетие активно развиваются методы формализованного описания технологических процессов с точки зрения науки о надежности технологических систем. При этом технология изготовления изделия представляется в виде технологической системы, которая должна обеспечить определенную вероятность выполнения задания по параметрам качества, параметрам производительности и параметрам затраченных ресурсов.
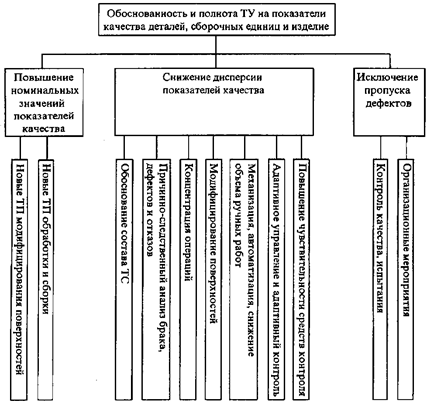
Рисунок 12 - Схема мероприятий повышения надежности технологических систем за счет обоснованности и полноты технических условий на показатели качества деталей, сборочных единиц и изделий
Основные понятия о технологических системах и методах оценки их надежности
Под технологической системой понимают совокупность функционально взаимосвязанных средств технологического оснащения, предметов производства и исполнителей для выполнения в регламентированных условиях производства заданных технологических процессов или операций.
Технологическая система является частью производственной системы и, как любая другая система, имеет свою структуру. Состав и структура технологической системы, условия производства, режим работы регламентируются конструкторской, технологической и другой технической документацией. Изменение этой документации приводит к соответствующему изменению системы.
Все технологические системы можно разделить на четыре иерархических уровня: технологические системы операций, технологические системы процессов; технологические системы производственных подразделений и технологические системы предприятий.
Технологическая система процесса включает в себя в качестве подсистем совокупность технологических систем операций, относящихся к одному методу (формообразования, обработки, сборки, контроля и испытаний) или к одному наименованию изготовляемой продукции. Следовательно, технологическая система операции является подсистемой технологической системы процесса.
Любая технологическая система может быть разбита на элементы, которые являются её частью и условно принимаются за неделимые на данной стадии анализа системы. Различают следующие виды технологических систем: последовательная, параллельная, комбинированная.
На рисунке 13 представлена технологическая система, состоящая из п технологических элементов, описывающих выполнение определенных технологических операций. На вход первого элемента подается полуфабрикат, характеризуемый xi(0) параметрами качества. После преобразования в первом элементе (выполнения первой технологической операции) эти параметры принимают с вероятностью P1(i, t) значения хi(1). Вероятность P1(i, t) является вероятностью выполнения технологического задания первым технологическим элементом по параметру хi. В связи с тем, что по мере эксплуатации технологического элемента его свойства изменяются, эта вероятность является функцией времени. Далее параметры xi(1) попадают на вход второго элемента и с вероятностью Р2(i, t) преобразуются в xi(2) и т.д.
Рисунок 13 - Структурная схема технологической системы
Некоторые параметры качества после первой, второй и т.д. операции могут не изменяться на последующих операциях и характеризовать готовую продукцию на выходе из n-го элемента. На рис. 12 это хе(1) - параметры после первой операции, хr(2) - после второй операции и хi(п) - после n-ой операции. Таким образом, готовая продукция будет характеризоваться набором параметров качества {хе(1), хr(2), ..., хi(n)}. Задача технологической системы - обеспечить значения параметров качества после каждого элемента и после выполнения последней операции в пределах допусков, заданных в технических условиях на детали, сборочные единицы и изделие в целом.
При этом, как показано в п.8.4, постоянный или выборочный контроль и подналадка технологической системы для минимизации отклонения среднего статистического значения показателя качества от его заданного номинального значения значительно повышает вероятность выполнения технологического задания по этому параметру качества.
Все технологические системы могут быть с жесткой и нежесткой связью подсистем или элементов. Причем, под технологической системой с жесткой связью понимают такие системы, у которых отказ хотя бы одной из подсистем вызывает немедленное прекращение функционирования технологической системы в целом. В технологической системе с нежесткой связью в этом случае не происходит немедленного прекращения функционирования всей системы.
Также отметим, что по уровню автоматизации выделяют: механизированную, автоматизированную и автоматическую технологические системы. Кроме того, по уровню специализации бывают специальные, специализированные и универсальные технологические системы.
Уровень и вид технологической системы является определяющим признаком для выбора критериев отказов и предельных состояний, показателей надежности и методов их оценки.
Для технологических систем, так же как и для технических систем, вводятся понятия работоспособное и неработоспособное состояние, исправные и неисправные состояния, а также предельное состояние. Например, под работоспособным состоянием технологической системы понимают такое её состояние, при котором значения параметров и показателей качества изготавливаемой продукции, производительности, материальных и стоимостных затрат на изготовление продукции соответствуют требованиям, установленным в нормативно-технической, конструкторской и технологической документации. Видно, что данное определение соответствует общему определению работоспособного состояния, однако конкретизирует способность технологической системы выполнять заданные функции по показателям качества, производительности и затрачиваемым ресурсам.
Математическая формулировка работоспособного состояния S(t) технологической системы может быть записана следующим образом:
,
где - множество допустимых состояний технологической системы; Q(t), R(t), c(t)- значения параметров качества, производительности и величин затрачиваемых ресурсов в момент t; - множество допустимых значений параметров качества, производительности и затрачиваемых ресурсов, при которых технологическая система в соответствии с нормативно-технической документацией считается работоспособной.
В связи с этим определением неработоспособное состояние технологической системы может возникать по параметрам качества, производительности или затрачиваемым ресурсам. Аналогично даются определения других состояний системы.
В технологической системе, также как и в любой технической системе, анализ работоспособности основан на анализе отказов. По характеру нарушения работоспособности выделяют функциональные и параметрические отказы.
Под функциональным отказом понимают прекращение функционирования технологической системы, не предусмотренное регламентированными условиями производства или конструкторской документацией. При этом возможно как полное, так и частичное прекращение функционирования. Примером частичного функционального отказа может служить поломка одного из инструментов при обработке детали на автоматической линии. При этом может происходить выпуск продукции, но без обработки соответствующих поверхностей.
Параметрический отказ характеризуется тем, что система продолжает функционировать, но как минимум один из параметров технологического процесса выходит за допустимые пределы. Например, выход значений показателей качества деталей за поле допуска на обработку, снижение ритма выпуска ниже заданного уровня, нерегламентированное изменение режимов обработки, превышение материальных и трудовых затрат, недопустимые загрязнения окружающей среды и т.д.
Оценка надежности технологических систем производится на стадии проектирования и её эксплуатации. Эта оценка проводится с целью оптимизации надежности вновь разрабатываемых или поддержания необходимого уровня надежности действующих систем. Оценка надежности проводится в результате определительной процедуры и проверяется с регламентированной периодичностью в результате контрольной процедуры.
Показатели надежности технологических систем и средств технологического оснащения выбирают из числа перечисленных в п. 3, а также используются специфические показатели, естественно, введенные на основе показателей п. 3. К ним относятся: установленная безотказная наработка (ресурс, срок службы); вероятность безотказной работы технологической системы по параметрам продукции (производительности, затратам); назначенная наработка технологического комплекса до подналадки; вероятность выполнения технологической системой задания по параметру качества, по объему выпуска и т.д.
Вероятность безотказной работы технологической системы по параметрам продукции (производительности, затратам) – это вероятность того, что в пределах заданной наработки не происходит отказа технологической системы по перечисленным параметрам.
Вероятность выполнения технологической системой задания - это вероятность того, что объем выпуска технологической системой годной продукции и затраты на её изготовление за рассматриваемый интервал времени соответствуют требованиям документации. В вероятности выполнения технологической системой задания по объему фактор затрат не учитывается.
Кроме единичных показателей надежности вводятся комплексные показатели: коэффициент использования технологической системы, коэффициент выхода годной продукции; коэффициент сохранения производительности технологической системы, коэффициент расхода i-го вида материальных (стоимостных) затрат.
Методы оценки надежности системы выбираются исходя из критериев отказов. При этом для оценки надежности по параметрам качества продукции рассматривают четыре группы показателей, характеризующие:
1. Точность технологического процесса и средств технологического оснащения.
2. Технологическую дисциплину.
3. Выполнение заданий по конкретным параметрам качества продукции.
4. Комплексные показатели.
Для оценки надежности технологической системы по параметрам производительности рассматривают группы показателей, характеризующие:
1. Снижение ритма выпуска ниже установленного уровня.
2. Невыполнение установленного объема производства годной продукции в установленные сроки.
3. Прекращение функционирования системы, обусловленное отказом одного из элементов средств технологического оснащения.
4. Превышение нормативных величин длительности простоя при техническом обслуживании, при смене инструмента, подналадке и т.д.
7.7 Оценка надежности выполнения задания технологической системой по параметрам качества продукции
Рассмотрим некоторый n-ый элемент технологической системы (рис. 12), который формирует параметры качества продукции хi(n). Индекс i относится к i-ому показателю качества детали после выполнения технологической операции, соответствующей n-ому элементу.
Величина хi зависит от свойств материала, режимов обработки, конструктивных особенностей обрабатывающей системы, точности настройки средств технологического оснащения, точности измерения самой величины и воздействия внешних факторов.
Свойства материала заготовки характеризуются не только средними значениями показателей качества, но и их рассеиванием, возникающим как в заготовках из одной плавки и партии, так и рассеиванием из-за наличия заготовок из разных плавок и разных партий.
Режимы обработки также характеризуются не только средними значениями, но и их рассеиванием из-за физико-химических флуктуации в зоне взаимодействия инструмента с деталью и наличия обратной связи в системе станок-приспособление-инструмент-деталь-приспособление-станок (система СПИД), а также рассеиванием из-за того, что система СПИД является нежесткой, теплопроводящей и т.д.
Точность настройки средств технологического оснащения и точность измерения параметра также характеризуются не только средними значениями, но и определенным рассеиванием, особенно в случае ручных операций.
Таким образом, любой параметр качества продукции хi является сложной функцией переменных, которые являются случайными величинами, зависящими от наработки технологического элемента:
, (76)
где zj - случайные величины, описывающие перечисленные выше факторы – показатели свойств материала, параметры режима обработки, параметры точности настройки средств технологического оснащения и т.д.
Для анализа влияния факторов zj на показатель качества хi необходимо знать в общем случае функции распределения случайных величин zj. Однако с целью упрощения задачи воспользуемся соотношениями (п.8.3), считая, что величины zj некоррелированы и характеризуются математическим ожиданием и стандартным отклонением . В этом случае параметр качества хi в окрестности своего математического ожидания может быть описан (см. также (59) и (64)) распределением с параметрами:
(77)
Таким образом, соотношение (77) устанавливает приближенную связь между характеристиками распределения параметра качества продукции и характеристиками распределений показателей свойств заготовки и показателей технологической системы элемента.
|