Технологічний процес нанесення гальванічних покриттів. Процес нанесення покриттів на деталі включає в себе три групи операцій - підготовку деталей до нанесення покриття, нанесення покриття та обробку деталей після покриття.
Підготовка деталей до нанесення покриття включає наступні операції: механічну обробку поверхонь, що підлягають нарощуванню; очистку деталей від окислів і попереднє знежирення; монтаж деталей на підвісне пристосування; ізоляцію поверхонь, що не підлягають покриттю; знежирення деталей з наступним промиванням у воді; анодний обробку (активацію).
Попередня механічна обробка деталей має мету надати відновлюваним поверхням правильну геометричну форму. Виробляється ця обробка відповідно до рекомендацій по механічній обробці відповідного матеріалу.
Очистку деталей від окислів з метою «пожвавлення» поверхні виробляють шляхом обробки шліфувальною шкуркою або м'якими колами з полировальной пастою. Попереднє знежирення деталей виробляють шляхом промивки в розчинниках (уайт-спірит, діхлоретане, бензині та ін.).
При монтажі деталей на підвісне пристосування необхідно забезпечити їх надійний електричний контакт з струмопровідної штангою, сприятливі умови для рівномірного розподілу покриття по поверхні деталі і для видалення бульбашок водню, що виділяються при електролізі. Для захисту поверхонь, що не підлягають нарощуванню, застосовують: цапонлак в суміші з нітроемалью у співвідношенні 1: 2 (його наносять в декілька шарів при пошарової сушці на повітрі); чохли з поліхлорвінілового пластикату товщиною 0,3 ... 0,5 мм; різні футляри, втулки, екрани, виготовлені з неелектропровідних кислотостійких матеріалів (ебоніт, текстоліт, вініпласт і т. п.).
Остаточне знежирення підлягають нарощуванню поверхонь деталей виробляють шляхом електрохімічної обробки в лужних розчинах наступного складу: їдкий натр -10 кг / м3, сода кальцинована - 25 кг / м3, тринатрийфосфат - 25 кг / м3, емульгатор ОП-7 3 ... 5 кг / м3. Режим знежирення: температура розчину 70 ... 80 ° С; щільність струму 5 ... 10 А / дм; тривалість процесу 1 ... 2 хв.
Після знежирення деталі промивають в гарячій, а потім в холодній воді. Суцільна без розривів плівка води на знежиреної поверхні свідчить про хорошу якість видалення жирів. Активацію (анодний обробку) виробляють для видалення найтонших окисних плівок з поверхні деталі та забезпечення найбільш міцного зчеплень гальванічного покриття з деталлю.

Підвісне пристосування для хромування шийок під підшипники на провідній шестерні заднього моста автомобіля ГАЗ-53А:
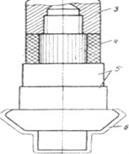
1. струмопідвідного штанга;
2. гачок;
3. гайка;
4. ізоляційна втулка;
5. хроміруемой поверхні;
6. захисний чохол.
Ця операція безпосередньо передує нанесенню покриття.
При хромування анодний обробку виробляють в основному електроліті. Деталі завішують у ванну для хромування і для прогріву витримують 1 ... 2 хв без струму, а потім піддають обробці на аноді протягом 30 ... 45 с при анодної щільності струму 25 ... 35 А / дм. Після цього, не виймаючи деталі з електроліту, перемикають їх на катода і наносять покриття.
При Осталювання активацію також виробляють шляхом анодної обробки деталей в спеціальній ванні з 30% -ним водним розчином сірчаної кислоти протягом 2 ... 3 хв, при температурі 18 ... 25 ° С і анодної щільності струму: для сталевих деталей 60 .. .70 А / дм2, для чавунних 10 ... 16 А / дм2 і для деталей з алюмінієвих сплавів 1 00 ... 120 А / дм2.
По завершенні активації деталі, що підлягають Осталювання, промивають спочатку в холодній, а зарахуємо в гарячій воді при температурі 50 ... 60 ° С, де їх одночасно підігрівають до температури, близької до температури електроліту для Осталювання. Підігріті деталі завантажують у ванну для Осталювання і після витримки протягом 10 ... 20 з включають струм. Нарощування покриття на початку протягом 2 ... 5 хв ведуть при катодного щільності струму 1 ... 5 А / дм2, а потім поступово (протягом 2 ... 10 хв) підвищують щільність струму до величини, встановленої режимом.
Обробка деталей після нанесення покриття включає наступні, операції: нейтралізацію деталі від залишків електроліту; промивку деталей у холодній і гарячій воді; демонтаж деталей з підвісного пристосування і видалення ізоляції; сушку деталей; термічну обробку (при необхідності); механічну обробку деталей до необхідного розміру.
Цей порядок виконання заключних операцій зберігається при нанесенні покриттів з будь-яких електролітів, проте конкретні процеси мають деякі особливості.
Так, якщо деталі піддаються хромуванню, то їх спочатку промивають у ванні з дистильованою водою (для уловлювання електроліту), а потім - - в проточній воді, після чого занурюють на 0,5 ...! мінв3 ... 5% -ний розчин кальцинованої соди (для нейтралізації залишків електроліту) і остаточно промивають у теплій воді. Потім деталі знімають з підвісних пристосувань, видаляють з них ізоляцію і сушать в сушильній шафі при температурі 120 ... 130 ° С. У деяких випадках для зняття внутрішніх напружень в хромових покриттях деталі проходять термообробку з нагріванням до 180 ... 200 ° С в масляній ванні і витримкою при цій температурі протягом 1 ... 2год.
Після Осталювання деталі промивають в гарячій воді, потім піддають нейтралізації від залишків електроліту в 10% -ому розчині каустичної соди при температурі 70 ... 80 ° С протягом 5 ... 10 хв, після чого знову промивають у гарячій воді і демонтують з підвісних пристосувань.
Хромування деталей.
З усіх гальванічних процесів, застосовуваних у авторемонтному виробництві, найбільш широке застосування отримало хромування, яке застосовується для компенсації зносу деталей, а також в якості антикорозійного та декоративного покриття. Широке застосування хромування пояснюється високою твердістю (НЦ = 4 ... 12ГПа) електролітичного хрому і його великий зносостійкість, яка в 2 ... 3 рази перевищує зносостійкість загартованої сталі 45. Електролітичний хром має високу кислотостійкість і теплостійкість, а також міцно зчіплюється майже з якими металами.
Поряд з достоїнствами процес хромування має і недоліки, до числа яких слід віднести: порівняно низьку продуктивність процесу (не більше 0,03мм / год) через малих значень електрохімічного еквівалента (0,324 г / А-ч) і виходу металу по струму (12 ... 15%); неможливість відновлення деталей з великим зносом, так як хромові покриття товщиною більше 0,3 ... 0,4 мм мають знижені механічні властивості; відносно високу вартість процесу хромування. В якості електроліту при хромування застосовується водний розчин хромового ангідриду (СгОз) та сірчаної кислоти. Концентрація хромового ангідриду може змінюватися в електроліті в межах 150 .. .400 кг / м3. Концентрація сірчаної кислоти повинна відповідати відношенню №SO4: Сюз = 1: 100 [1: (80 ... 125)].
У процесі хромування на катоді відбуваються відновлення шестивалентного хрому (СгОз) до тривалентного (Спозі), відкладення металевого хрому і виділення водню. На аноді при цьому протікають окислювальні процеси: окислення тривалентного хрому до шестивалентного і виділення кисню.
Склад електроліту при експлуатації ванни хромування безперервно змінюється за рахунок витрати хромового ангідриду на відкладення металевого хрому, тому його необхідно періодично контролювати і коригувати.
Хромові покриття знижують втомну міцність деталей на 20 ... 30%.
Осталювання деталей.
Осталюванням називається процес отримання твердих зносостійких залізних покриттів з гарячих хлористих електролітів.
В якості електроліту при Осталювання застосовують водний розчин хлористого заліза (РеС12-4Н2О), що містить невелику кількість соляної кислоти (НС1), і деякі інші компоненти, які вводяться для підвищення міцності зчеплення покриття з деталлю (хлористий марганець МпС12-4Н2О) або для поліпшення зносостійкості (хлористий нікель NiCl-4H2O).
Концентрація хлористого заліза в електроліті може змінюватися в межах 200 ... 700 кг / м3. Електроліти з низькою концентрацією хлористого заліза (200 ... 220 кг / м) забезпечують отримання покриттів невеликої товщини (до 0,3 ... 0,4 мм), але з високою твердістю. З електролітів високої концентрації (650 ... 700 кг / м3РеС12-4Н2О) можуть бути отримані покриття товщиною 0,8 ...! мм і більше, проте з меншою твердістю.
Вміст соляної кислоти в електроліті повинно бути в межах 1,2 ... 3 кг / м3. При більш низькому її змісті знижується вихід металу по струму, і в електроліті утворюється гідроокис заліза, яка, потрапляючи в покриття, погіршує його якість. Підвищення кислотності електроліту не погіршує якості покриття, але знижує вихід металу по струму.
Найбільш раціональним є електроліт середньої концентрації, що містить (400 + 200) кг / м3 РеС12-4Н2О, (2 + 0,2) кг / м3 НС1 і (10 + 2) кг / м3 МпСЬ * 4Н2О. Цей електроліт стабільний у роботі і майже не вимагає коригування складу за змістом основної солі, забезпечує отримання рівномірних покриттів з необхідною твердістю і товщиною, має високий вихід металу по струму і сприяє підвищенню міцності з'єднання покриттів з поверхнею деталі, тому що містить хлористий марганець.
Процес нанесення покриття при Осталювання проводиться в сталевих ваннах, внутрішня поверхня яких футерована кислотостойким матеріалом.
Враховуючи підвищену агресивність хлористих електролітів, як футерування для ванн застосовують графітові плитки, просочені смолою, хороша теплопровідність матеріалу яких дозволяє виробляти нагрів електроліту в таких ваннах через водяну сорочку.
Ванни для Осталювання виготовляють також з фаоліту. Цей матеріал володіє високою кислотостойкостью, але має погану теплопровідність, тому нагрів електроліту до необхідної температури в цьому випадку виробляють нагрівачами, поміщеними в електроліт.
|