Механічна обробка відновлених деталей При механічній обробці відновлених деталей застосовують такі технологічні операції: токарну, свердлильну, розточну, фрезерну, шліфувальну, полірувальну та хонінгувальну.
Механічна обробка деталей має ряд особливостей, які в основному пов’язані з вибором виду й режиму обробки. Вибір методу та режиму механічної обробки деталей значною мірою ускладнюють: висока твердість поверхонь, які обробляють, нерівномірність розподілу припусків на цих поверхнях, специфічні фізико-механічні властивості металопокриття.
При обробці деталей під ремонтний розмір, найбільш часто застосовують шліфування із зменшеними глибиною різання та подачею.
Значні труднощі виникають при обробці деталей під початковий розмір, які відновлюють наплавленням і напиленням.
Залежно від твердості наплавленого металу, обробку проводять як на токарному верстаті (при твердості наплавленого металу менше HRC 35…40), так і на шліфувальному (якщо твердість наплавленого металу перевищує HRC 35…40).
Особливості механічної обробки напиленого покриття пов’язані з його під вищеною хрупкістю, пористістю і твердістю. Залежно від твердості й величини припуску на механічну обробку напиленого покриття також виконують на токарному або шліфувальному верстатах. Токарний верстат при цьому повинен працювати на знижених режимах різання (швидкість різання не повинна перевищувати 60…80 м/хв., глибина різання – в межах 0,1…0,3 мм, подача – 0,1…0,2 мм/об), використовуючи різці з пластинками з твердих сплавів. Для шліфування деталей, котрі напилені зносостійкими покриттями з високою твердістю, використовують алмазне коло на вулканітовій зв’язці, а при його відсутності застосовують мало – або середньозернисте карборундове коло на керамічній зв’язці.
Деталі, покриті хромом, унаслідок його твердості обробляють шліфуванням, використовуючи електрокорундовий шліфувальний круг.
Основною особливістю механічної обробки деталей з покриттями із синтетичних матеріалів (пластмас) є їх низька теплопровідність і недопустимість нагрівання реактопластів до температури більше 150…160°С, а термопластів – до температури понад 120°С. Ці деталі обробляють на токарному верстаті, який повинен працювати з особливим режимом (швидкість різання висока – 250…300 м/хв., подача мала – 0,1…0,2 мм/об).
При механічній обробці відновлених деталей треба забезпечити такі технологічні параметри: шорсткість, точність, форму, розміри й взаємне розміщенн робочих поверхонь. Великі труднощі виникають при забезпеченні взаємного розміщення робочих поверхонь на деталі. Воно залежить від правильного вибору технологічної бази при її обробці. Технологічна база – це та поверхня деталі, яка визначає її положення під час виготовлення або ремонту. При виборі технологічної бази враховують наступні вимоги:
- вона повинна визначати положення деталі у складальній одиниці;
- вона повинна бути найбільш точно розміщена відносно поверхні, яку обробляють;
- вона має забезпечити обробку всіх поверхонь деталі, які її потребують;
- вона повинна забезпечити мінімальну деформацію деталі від зусиль при її обробці та закріпленні.
При відновленні деталей за технологічну базу приймають ту її поверхню, яку використовували при виготовленні. Якщо вона порушена, то обробку починають з відновлення технологічної бази.
Лекція _____
Тема: Відновлення деталей методом додаткових ремонтних деталей
План
1. Відновлення деталей встановленням додаткових ремонтних деталей.
2.Відновлення зміною частини деталі.
Відновлення деталей встановленням додаткових ремонтних деталей.
Це різновид способу ремонтних розмірів. Суть цього способу полягає в тому, що зношені поверхні деталей шляхом механічної обробки виправляють і встановлюють знову виготовлені додаткові ремонтні деталі, які і компенсують зношений і знятий метал (прокладки, втулки, шайби та ін.). Якщо деталь – вал, то для комплектації на нього насаджується втулка. Якщо отвір, то на нього запресовкою встановлюється втулка.
Для міцного і надійного з’єднання додаткової ремонтної деталі з основною необхідно правильно вибрати посадку і засіб закріплення (клей, зварювання, стопорні гвінти, штіфти та ін.). Після встановлення додаткова ремонтна деталь обробляється під номінальний розмір спряження. Так можна відновлювати сильно зношені шийки валів і отворів деталей під номінальний розмір, не змінюючи структуру та термообробку основної деталі, отримати високу якість відновлених деталей.
До недоліків такого відновлення відноситься:
- зменшення жорсткості та міцності конструкції при введенні допоміжної деталі у розмірний ланцюг;
- погіршення умов роботи з’єднання (теплові напруження);
- зменшення жорсткості допусків на знов встановлені ланцюги при введенні в розмірний ланцюг нових деталей.
Даний метод застосовується при поновленні отворів під підшипники в корпусних деталях (картерах, редукторах, коробках швидкостей, різноманітних посадочних поверхнях – поновлення гільзуванням).
Відновлення зміною частини деталі.
По суті метод подібний до розглянутого методу встановлення додаткових ремонтних деталей. Він складається із таких операцій:
- видалення деіектної частини і підготовка повехні з’єднання (термічно оброблені, складні деталі – каретки, блок шестерень, шліцові, карданні вали потребують місцевого відпуску перед віддаленням (механічною обробкою) дефектного елемента);
- виготовлення замінюваної частини (матеріал цієї частини такий самий, як і основної деталі, виготовляють її під нормальний розмір без припусків на наступну обробку, за винятком, коли необхідна співвісність або точність взаєморозташування, яке фіксується по цій частині деталі, термообробку до встановлення на основну деталь);
- з’єднання та закріплення зміненої частини (виконують посадкою на різьбі, запресовкою, зваркою тощо. Після зварювання для зняття напружень застосовують нормалізацію або відпалювання);
- кінцева механічна обробка та контроль (частину обробляють під номінальний розмір та у всіх деталей перевіряють співвісність та взаємне розташування всіх елементів).
Цим способом ремонтують, як правило, дороговартісні та складні деталі, наприклад, багатовінцеві зубчасті колеса і т.п.
Лекція _____
Тема: Відновлення деталей методом пластичного деформування
План
1. Технологічні прийоми відновлення деталей пластичним деформуванням.
2. Обтиснення
3. Осадження
4. Вдавлювання
5. Накатка
Технологічні прийоми відновлення деталей пластичним деформуванням.
Роздача застосовується для відновлення пустотілих деталей циліндричної форми (поршневих пальців, втулок і ін.). При цьому зовнішній – робочий розмір діаметра збільшується за рахунок зміни внутрішнього – неробочого (рис. 6.18). При роздачі напрямок тиску від дії зовнішньої деформуючої сили збігається з напрямком деформації.
Обтиснення
Обтиснення – застосовується для відновлення деталей (втулок), зношених по внутрішньому робочому отвору. При обтисненні, як і при роздачі, збігаються напрямки дії деформуючої сили (тиску) і деформації (рис. 6.18 б). Цим методом відновлюють втулки розподільних валів, вушка під пальці ланок гусениць і ін.
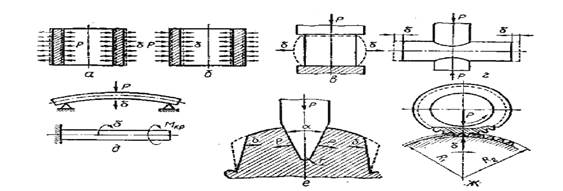
Рис. 6.18. Технологічні прийоми відновлення деталей пластичним
деформуванням:
а – роздача; б – обтиснення; в – осадження; г – витяжка; д – правка; е –
вдавлювання; ж – накатка (R1 – до відновлення; R2 – після відновлення)
На рис. 6.19 зображено пристосування для обтиснення бронзових втулок. Відновлювану деталь 2 за допомогою пуансона 1 проштовхують через матрицю 3, встановлену в основу штампа 4. При цьому за рахунок зменшення зовнішнього діаметра D відновлюється розмір внутрішнього діаметра d.
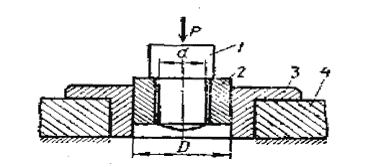
Рис. 6.19. Пристрій для обтиснення бронзових втулок
Після обтиснення, для одержання необхідної шорсткості поверхні і заданого розміру отвору, втулку розвертають або прошивають.
Осадження
Осадженням збільшують зовнішній діаметр суцільних деталей, а також зменшують внутрішній і збільшують зовнішній діаметр порожнистих деталей за рахунок зменшення їхньої довжини. При осадженні напрямок діючої сили перпендикулярний напрямку деформації δ (рис. 6.18 в). Осадженням відновлюють бронзові втулки верхньої голівки шатуна.
Вдавлювання
Вдавлювання застосовується для відновлення деяких шарових пальців, зубів шестерень, бічних поверхонь шліців і т.п. Воно поєднує в собі одночасно осадження і роздачу, а діюча сила спрямована під кутом до напрямку деформації δ (рис. 6.18 е).
Витяжка дозволяє подовжувати важелі, тяги, стрижні за рахунок місцевого звуження поперечного перерізу на неробочих ділянках (рис. 6.18 г). Витяжку проводять при місцевому нагріванні до температури 820...850 °С.
Накатка
Накатка (рис. 6.18 ж) застосовується для збільшення зовнішніх або зменшення внутрішніх розмірів за рахунок пластичного витиснення металу на окремих ділянках робочої поверхні. Накатку застосовують для відновлення розмірів посадочних поверхонь під підшипники кочення. Після накатки міцність деталей знижується, тому що западини, утворені накаточним інструментом, є концентраторами напружень. З метою підвищення несучої здатності ділянок валів під підшипники, залиті антифрикційним матеріалом, западини на останніх заливають бабітом.
В якості накаточного інструмента використовують зубчастий ролик, виготовлений з інструментальної або шарикопідшипникової сталі, загартованої до твердості 56...62 НRС. При накатці ролик встановлюється на державці в супорті токарного верстата.
Правка (рис. 6.18 д) – один з найпоширеніших технологічних прийомів усунення вигину, скручування, жолоблення і т.п. Правкою відновлюють вали, шатуни, рами та інші деталі. Залежно від величини деформації і фізико-хімічних властивостей матеріалу деталі правлять у гарячому і холодному стані.
При холодній правці в результаті місцевого пластичного деформування металу сильно змінюються його структура і фізико-механічні властивості, причому має місце значна неоднорідність властивостей і розподілу залишкових напружень по перерізу. У зв'язку з цим при правці необхідно прагнути до одержання меншої локальної пластичної деформації, а також її рівномірного розподілу в металі деталі.
Для вирівнювання внутрішніх напружень після правки деталь доцільно піддати стабілізуючому нагріванню до температури, рівної 0,8Тотп, де Тотп – температура відпуску нової деталі. Час витримки при цьому складає 0,5...1 год.
При більших деформаціях виконують гарячу правку деталей при температурі 600...800 °С. Прогин колінчастого вала один з найпоширеніших дефектів, що усувають правкою на пресі перед шліфуванням шийок. Правка під пресом викликає сильні структурні зміни і знижує втомну міцність валів.
Дуже ефективним методом є правка валів місцевим наклепом. Вона заснована на дії залишкових внутрішніх напружень стиску, що виникають при наклепі. Так, при наклепі колінчастого вала (рис. 6.20) створені на окремих ділянках залишкові напруження усувають прогин. При наклепі використовують пневматичний молоток із закругленим бойком.
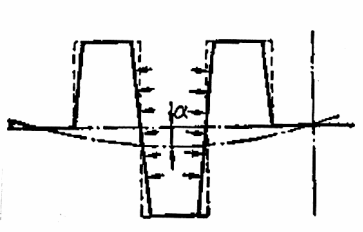
Рис. 6.20. Правка колінчастого вала місцевим наклепом
Контролюють вали і осі після виправлення в центрах за допомогою індикаторних пристосувань; плоскі деталі контролюють лінійками і щупами.
Лекція _____
|